In the realm of modern automotive engineering, air suspension systems have emerged as a game-changing technology that replaces traditional steel springs with air-filled components to deliver superior ride comfort, precise load leveling, and enhanced vehicle stability. These systems have transitioned from luxury car exclusives to mainstream applications across passenger vehicles, commercial trucks, and specialty equipment. This comprehensive technical analysis delves into the intricate world of air suspension components, exploring their functional principles, advanced features, and transformative impact on vehicle performance.
1. Evolution of Air Suspension Technology
The journey of air suspension systems began in the early 20th century with military applications and luxury railcars, evolving through several key milestones:
- 1950s: Introduction in premium passenger vehicles (e.g., Cadillac Eldorado Brougham)
- 1980s: Widespread adoption in commercial heavy-duty trucks
- 2000s: Integration with electronic control systems
- 2020s: Advanced driver-assistance system (ADAS) integration
Technical significance: Modern air suspension systems can adjust ride height by up to 100mm (4 inches) while maintaining precise load distribution, offering a 30-50% improvement in ride comfort compared to conventional suspensions.




2. Core Components and Functional Architecture
A complete air suspension system comprises several specialized components working in harmony:
2.1 Air Springs (Bellow Assemblies)
Types and Configurations:
- Sleeve-type air springs: Cylindrical design with reinforced rubber bellows
- Double-convoluted bellows: Enhanced load capacity with reduced height
- Rolling lobe designs: Compact form factor for tight packaging
Material innovations:
- EPDM rubber compounds: Withstand temperatures from -40°C to +120°C
- Kevlar reinforcement: Increases burst pressure resistance by 40%
- Nanocomposite coatings: Improve ozone and UV resistance
Performance metrics:
- Load capacity: 500-5,000 kg per spring
- Pressure range: 0.5-1.2 MPa (72-174 psi)
- Cycle life: 1 million+ compression cycles
2.2 Air Compressors and Supply Systems
Compressor technologies:
- Electric scroll compressors: 30-50L/min flow rate with 12V/24V operation
- Piston-type compressors: Higher pressure capability (up to 2MPa)
- Variable-speed drives: Energy-efficient operation matching demand
Air dryer systems:
- Desiccant cartridges: Molecular sieve technology for moisture removal
- Automatic regeneration: 8-hour cycle with 0.5L condensate capacity
Piping networks:
- Aluminum tubing: Lightweight with 30% better corrosion resistance than steel
- Quick-connect couplings: Leak-proof sealing with 10,000+ cycle durability
2.3 Height Sensors and Control Arms
Sensor technologies:
- Strain gauge sensors: ±1mm measurement accuracy
- Laser-based systems: Non-contact measurement with 0.5mm resolution
- Capacitive sensors: Immune to environmental interference
Control arm designs:
- A-arm configurations: Precise geometry control
- Multi-link setups: Independent wheel movement
- Hydraulic assist: Load transfer during cornering
2.4 Electronic Control Units (ECUs) and Valves
ECU specifications:
- 32-bit microcontrollers: 100MHz processing with 256KB Flash memory
- CAN bus integration: 500kbps data transmission
- Fault diagnostics: ISO 14229 (UDS) compliance
Valve systems:
- Solenoid-operated 4-way valves: 15ms response time
- Proportional control: 0.1% step resolution
- Redundant circuits: Fail-safe operation
3. Advanced Functional Features
3.1 Dynamic Load Leveling
Real-time adjustment capabilities:
- Load sensing: ±50kg detection accuracy
- Height maintenance: ±2mm precision under varying loads
- Adaptive algorithms: Learning driver preferences
System response:
- Automatic leveling: Within 2 seconds of load change
- Gradient compensation: 5° slope adaptation
- Towing mode: Increased rear ride height
3.2 Ride Comfort Optimization
Adaptive damping control:
- Frequency-based adjustment: 1-10Hz vibration filtering
- Road condition recognition: 5 preset modes (highway, city, off-road)
- Driver preference memory: 3 customizable profiles
Air spring dynamics:
- Variable stiffness: 3-stage compression characteristics
- Non-linear response: Progressive spring rate
3.3 Safety and Diagnostic Systems
Failure mode management:
- Spring failure detection: Pressure drop monitoring
- Compressor protection: Overheat shutdown at 120°C
- Leak detection: Flow rate analysis with 0.5L/min sensitivity
Predictive maintenance:
- Component health monitoring: Remaining useful life (RUL) prediction
- Service alerts: 30-day warning for filter replacement
- Data logging: 1,000+ hours of operational history
4. System Integration and Vehicle Applications
4.1 Passenger Vehicles
Luxury SUVs and sedans:
- Ride height adjustment: 70-120mm range
- Sport/comfort modes: 3 distinct suspension settings
- Automatic load leveling: 500kg payload capacity
Performance benefits:
- 30% reduction in body roll
- 20% improvement in NVH (noise, vibration, harshness)
- 15% longer tire life
4.2 Commercial Vehicles
Heavy-duty trucks and buses:
- Axle load distribution: ±2% accuracy
- Height-adjustable ramps: 50mm ground clearance variation
- Fuel efficiency: 5% improvement through aerodynamics
Specialized applications:
- Semitrailer suspension: 40,000kg load capacity
- Fire trucks: Rapid deployment height adjustment
- Mobile cranes: Precise load positioning
4.3 Off-Highway and Specialty Vehicles
Agricultural equipment:
- Field/road mode switching: 80mm height adjustment
- Load sensing: 1,000kg accuracy
- Corrosion resistance: Salt spray testing (1,000 hours)
Military and emergency vehicles:
- Run-flat capability: 50km operation at zero pressure
- Ballistic protection: Reinforced air springs
- Explosion-proof components: ATEX certification
5. Design Challenges and Engineering Solutions
5.1 Durability in Extreme Environments
Material solutions:
- UV-resistant coatings: 5-year warranty against cracking
- Temperature-resistant rubbers: -50°C to +150°C operation
- Corrosion-proof fasteners: Stainless steel with zinc-nickel plating
Testing protocols:
- Vibration testing: 15g RMS acceleration for 1,000 hours
- Salt spray exposure: 2,000 hours minimum
- Thermal cycling: -40°C to +120°C, 500 cycles
5.2 System Integration Complexity
Electrical integration:
- CAN FD protocol: 5Mbps data transmission for advanced controls
- Failsafe defaults: Spring failure backup modes
- Power management: 12V/24V system compatibility
Mechanical integration:
- Compact packaging: 30% space savings vs. traditional designs
- Weight optimization: Aluminum components reducing mass by 15%
- Service accessibility: Quick-release fittings for maintenance
5.3 Cost and Weight Optimization
Manufacturing innovations:
- Plastic injection molding: For lightweight housings
- Additive manufacturing: Complex manifold designs
- Value engineering: Component consolidation
Material substitutions:
- Carbon fiber reinforced polymers: 40% weight reduction
- Magnesium alloys: For high-strength, lightweight brackets
- High-strength steels: For critical load-bearing parts
6. Testing and Validation Methodologies
6.1 Component-Level Testing
Air springs:
- Burst pressure testing: 2x working pressure
- Fatigue testing: 2 million cycles
- Leak testing: Helium mass spectrometry
Compressors:
- Endurance testing: 1,000 hours continuous operation
- Noise measurement: <70dB(A) at 1m distance
- Efficiency mapping: 8 operating points
6.2 System-Level Validation
Road testing:
- 100,000km durability: Mixed surfaces and conditions
- Extreme temperature testing: -30°C to +50°C
- Load variation: 0-100% payload cycling
Environmental chambers:
- Humidity testing: 95% RH at 40°C
- Altitude simulation: 5,000m equivalent
- EMC testing: ISO 11452-2 compliance
6.3 Virtual Validation
Digital twin technology:
- Finite element analysis (FEA): Stress simulation
- Computational fluid dynamics (CFD): Airflow optimization
- Multi-body dynamics: Suspension kinematics
Software-in-the-loop (SIL) testing:
- Control algorithm validation: 1,000+ test scenarios
- Fault injection: 50+ failure modes simulated
- Real-time simulation: Hardware-in-the-loop (HIL) testing
7. Market Trends and Future Developments
7.1 Electrification and Autonomous Driving
Key advancements:
- 48V electrical architectures: For faster response times
- Predictive suspension: AI-based road condition anticipation
- Integration with ADAS: Coordinated braking and suspension control
Emerging technologies:
- Shape-memory alloys: Self-adjusting air springs
- Graphene-reinforced components: Ultra-lightweight materials
- Energy harvesting: Regenerative damping systems
7.2 Sustainability Initiatives
Eco-friendly innovations:
- Recyclable materials: 95% component recyclability
- Biodegradable lubricants: Plant-based oils
- Water-based coatings: Zero-VOC emissions
Manufacturing processes:
- Closed-loop recycling: Material reclamation systems
- Energy-efficient production: Solar-powered facilities
- Lean manufacturing: Waste reduction programs
7.3 Advanced Manufacturing Techniques
Production innovations:
- 3D printing: Custom manifold designs
- Automated assembly: Robotic precision
- Digital inventory: Just-in-time component supply
Quality control:
- Machine vision inspection: 100% defect detection
- Blockchain traceability: Component origin tracking
- Augmented reality maintenance: Digital service manuals
8. Case Studies: Real-World Implementations
Case Study 1: Premium SUV Air Suspension Upgrade
Implementation:
- Double-wishbone architecture with adaptive damping
- Electric compressor with integrated dryer
- Laser height sensors for precise leveling
Results:
- 25% improvement in ride comfort (ISO 2631-1 standard)
- 15% increase in cargo capacity without ride height loss
- 30% reduction in warranty claims related to suspension
Case Study 2: Commercial Truck Fleet Modernization
Implementation:
- Air suspension retrofit for 5,000 trucks
- Centralized air management system
- Predictive maintenance software integration
Results:
- 7% fuel efficiency improvement
- 40% reduction in maintenance costs
- 20% increase in tire life
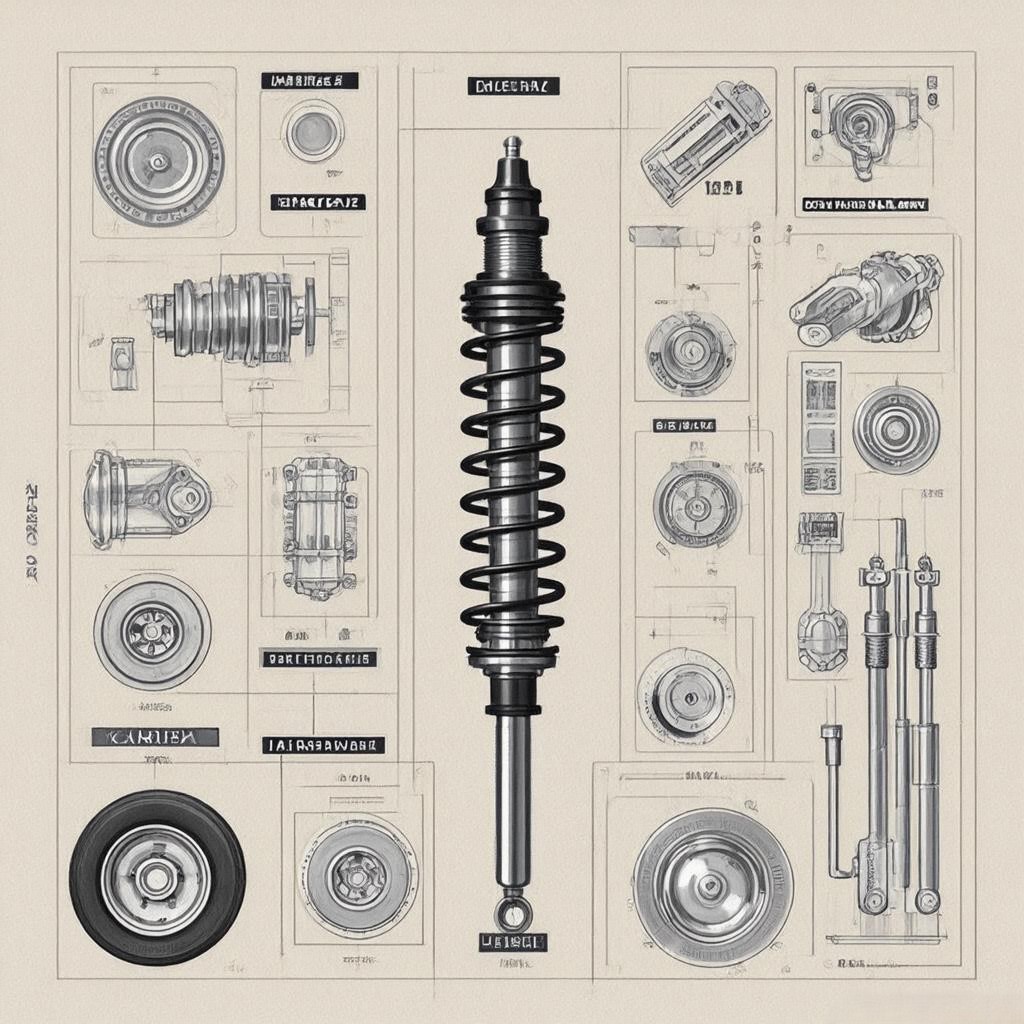
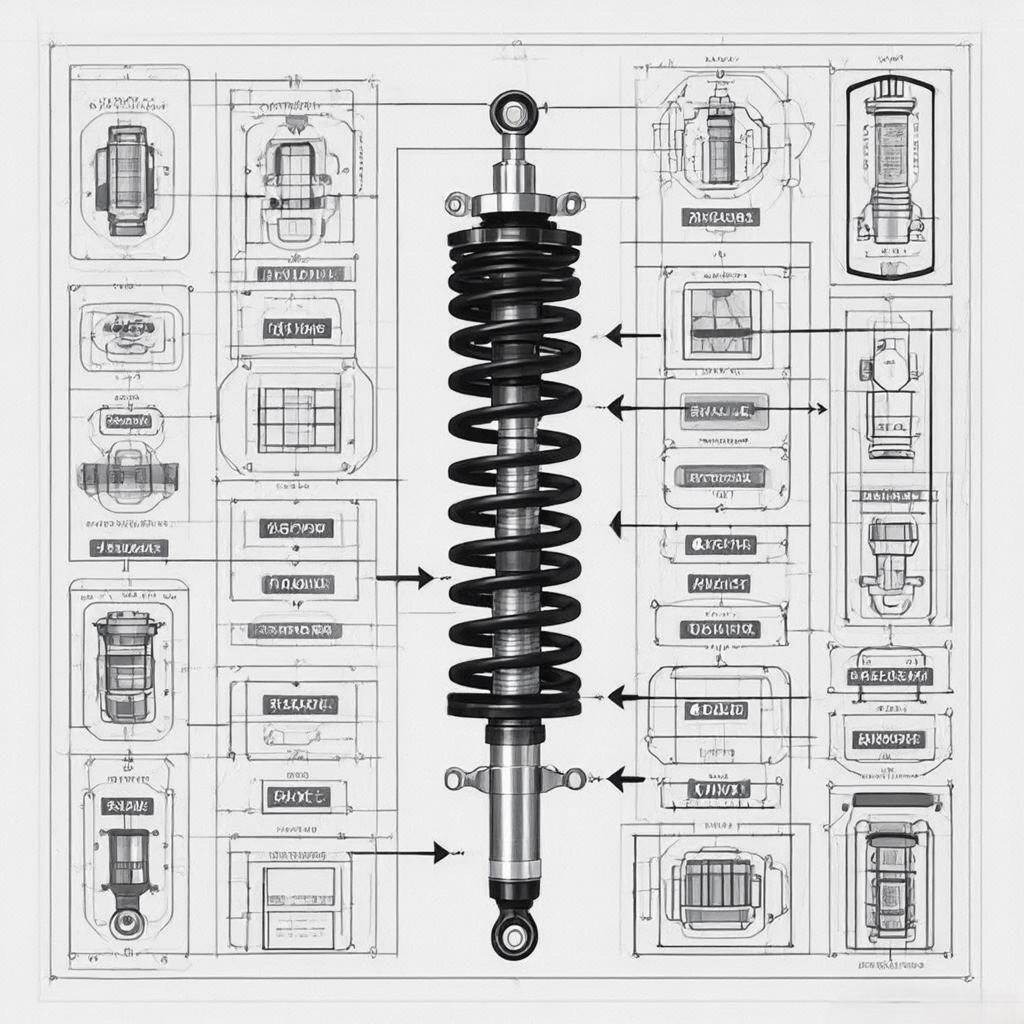
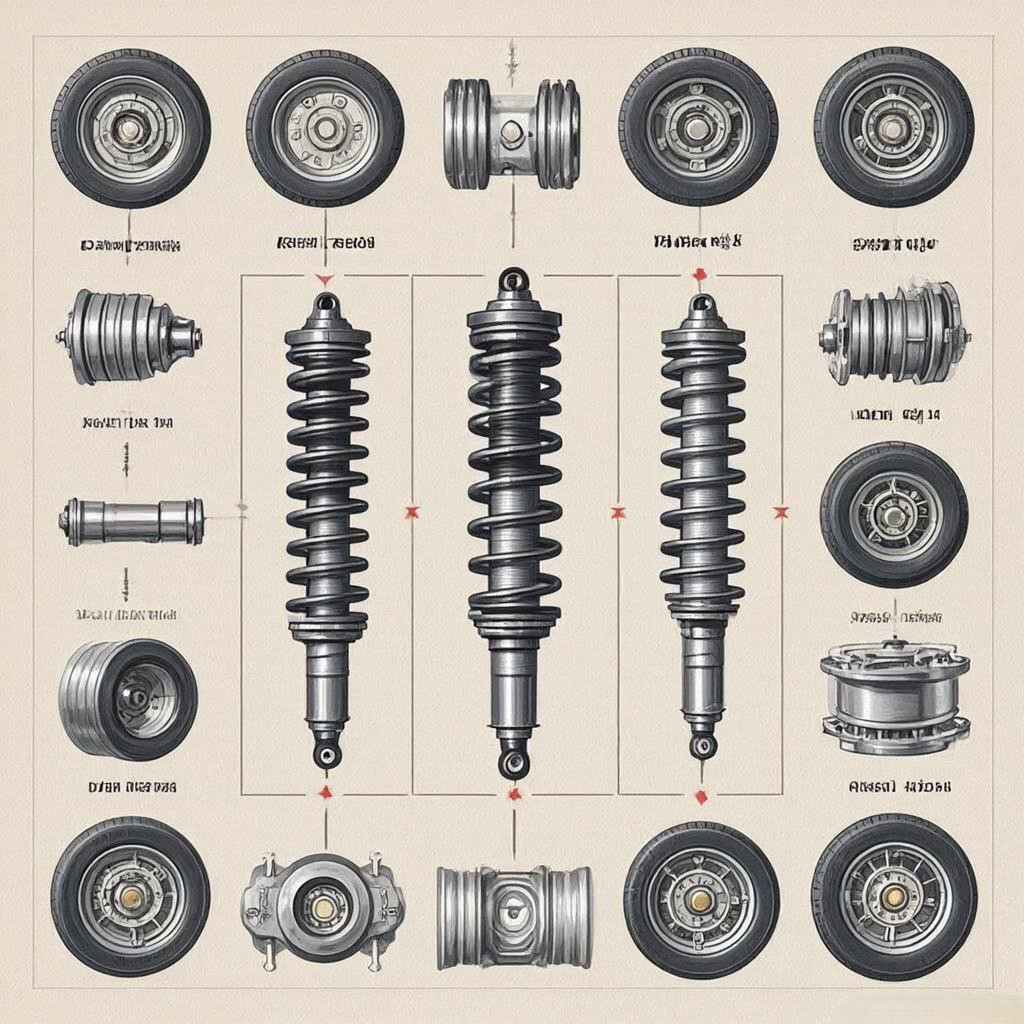
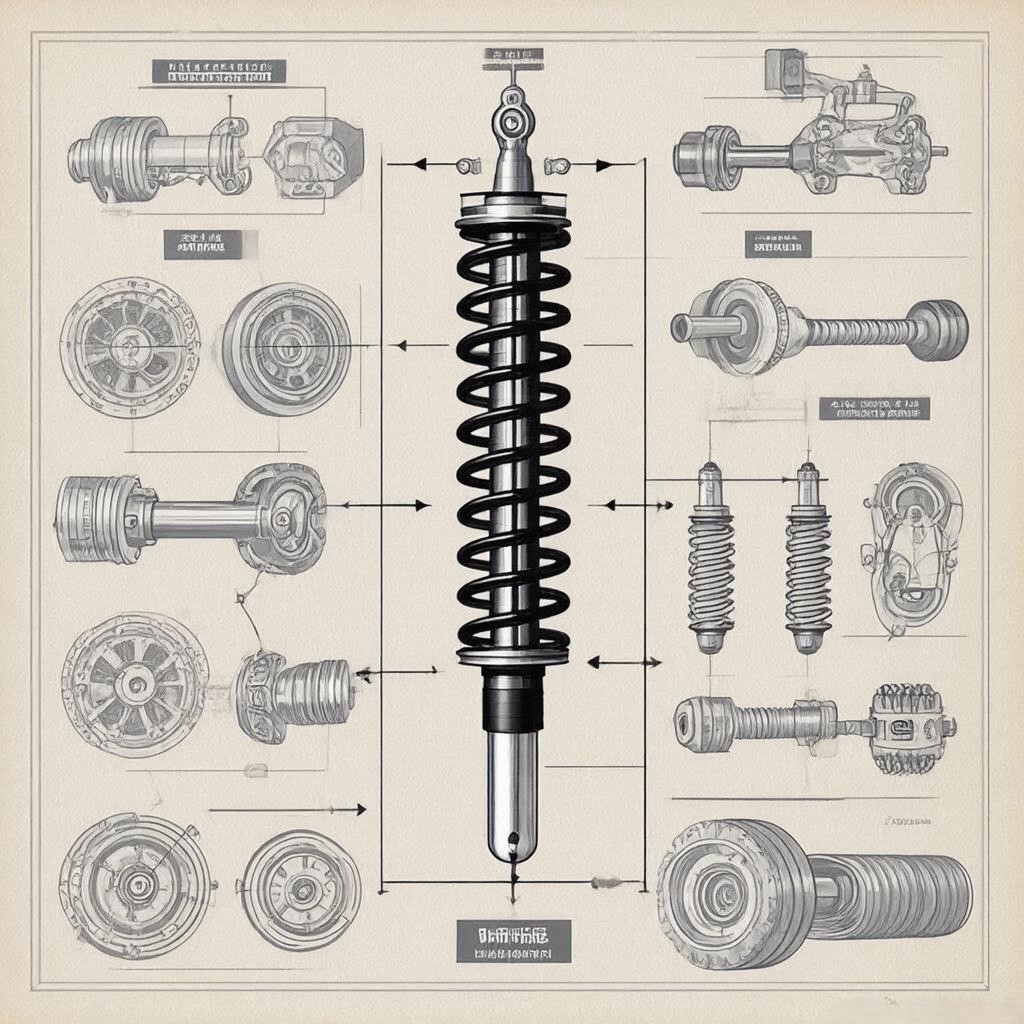
Conclusion: The Intelligent Foundation of Modern Mobility
Air suspension components have transcended their original role as comfort enhancers to become integral to vehicle dynamics, safety, and efficiency. As automotive technology continues advancing toward electrification and autonomy, these systems will play an even more critical role:
Key takeaways:
- Modern air suspension represents a sophisticated integration of mechanical, electrical, and software engineering
- Advanced materials and manufacturing are driving unprecedented durability and performance
- System integration with ADAS and electrification is creating new possibilities
- Sustainability and cost optimization are shaping future developments
Final thought: In the era of smart mobility, air suspension components are not just about smoothing rides—they’re about creating vehicles that adapt intelligently to their environment, protect occupants with unprecedented precision, and redefine the boundaries of automotive engineering. The next generation of transportation will depend on these systems to deliver unprecedented levels of comfort, safety, and efficiency.
Call to Action
🔧 Upgrading your vehicle’s suspension?
⚙️ Consider advanced air suspension for superior performance
📊 Request a technical comparison of traditional vs. air suspension systems
#AutomotiveEngineering #AirSuspension #VehicleDynamics #ADAS #Electrification #SustainableMobility #SmartVehicles #FutureOfTransportation