Introduction
Electronic Braking Systems (EBS) revolutionize commercial vehicle safety by blending pneumatic control with digital precision. Yet, improper valve installation can lead to erratic braking, fault codes, or even system lockouts. This guide breaks down EBS valve mounting, pneumatic/electrical integration, and ECU programming into 10 foolproof steps, ensuring your installation meets ISO 7638 and OEM standards. Perfect for fleet technicians and aftermarket retrofitters.
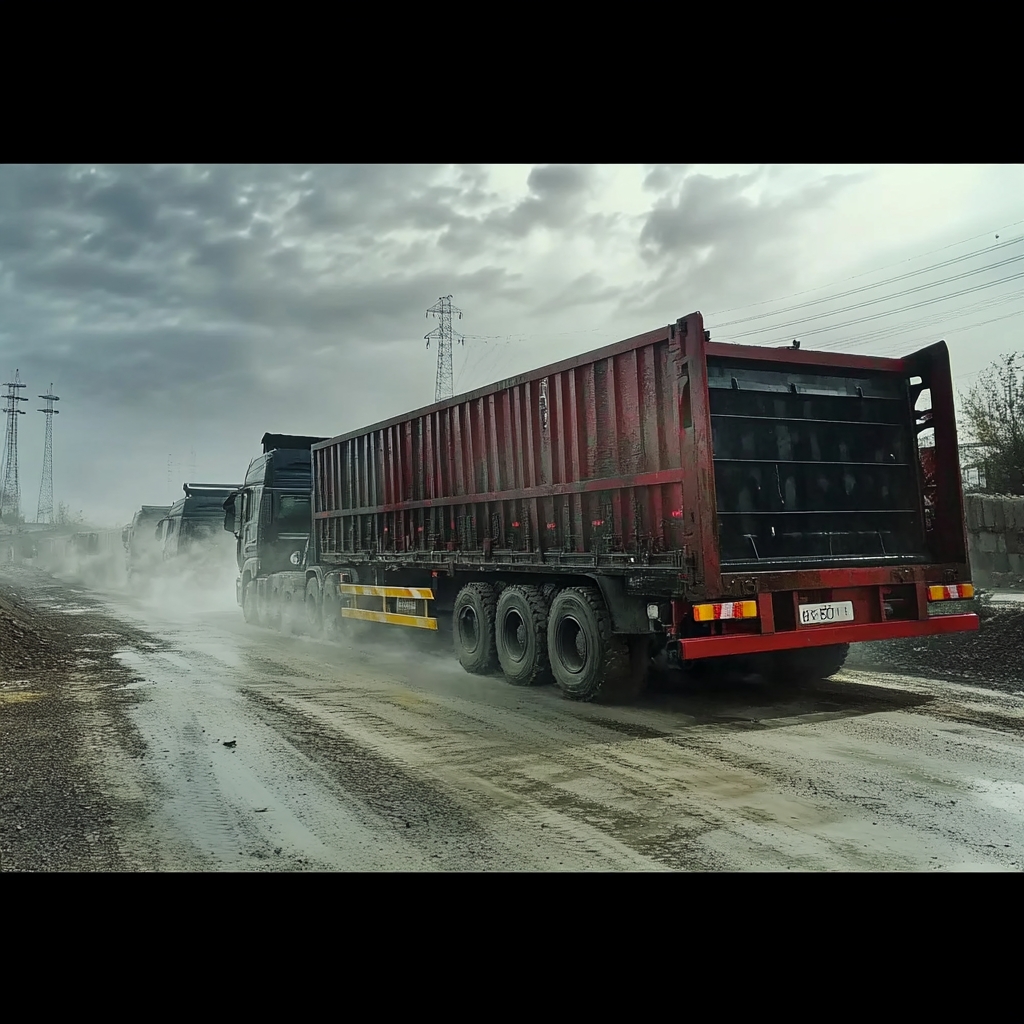
Section 1: Tools and Safety Precautions
Tools & Materials:
- EBS valve assembly (match ABS/EBS generation, e.g., WABCO EBS3 or Knorr-Bremse EBS 5).
- Torque wrench (5–25 Nm range).
- Pneumatic line crimper and DOT-approved tubing.
- 12V/24V compatible wiring harness (shielded, SAE J1128 rated).
- Diagnostic tool (e.g., ACME ProScan or Jaltest).
- Threadlocker (medium strength) and silicone grease.
Safety First:
- Depressurize air tanks and disconnect batteries.
- Wear safety glasses when handling high-pressure lines.
Section 2: 10-Step Installation Process
Step 1: Valve Positioning & Mounting
- Locate Mounting Points:
- Install near the brake chambers, avoiding heat sources (e.g., exhaust) and ensuring service access.
- Use OEM brackets or ACME universal brackets (adjustable for frame rails).
- Secure the Valve:
- Hand-tighten bolts, then torque to 15 Nm (e.g., Meritor EBS valves). Apply threadlocker.
Pro Tip: Leave 2+ inches between valves for heat dissipation and hose routing.
Step 2: Pneumatic Line Connections
- Primary/Secondary Circuits:
- Connect red lines (primary) and blue lines (secondary) to corresponding tank ports.
- Use ¼” tubing for control lines, ½” for supply lines.
- Crimp Fittings:
- Double-crimp all fittings and tug-test for security.
Critical Check: Verify O-rings are lubricated with silicone grease to prevent air leaks.
Step 3: Electrical Harness Wiring
- Pinout Verification:
- Match harness pins to valve connectors (e.g., CAN High/Low, 12V+, ground).
- Reference wiring diagrams (e.g., WABCO #12345678).
- Shielding & Grounding:
- Wrap harness in braided shielding, grounded to chassis (resistance <0.5 Ω).
Red Flag: Never route EBS wires parallel to alternator cables—cross at 90° angles.
Step 4: CAN Bus Integration
- Tap into Vehicle CAN:
- Locate the CAN bus connector (J1939 or J1708).
- Splice EBS valve CAN wires using solder-seal connectors.
- Termination Resistors:
- Confirm 120 Ω resistance across CAN lines (add resistors if missing).
Step 5: ECU Power-Up & Initialization
- Reconnect Batteries:
- Power on the ECU and wait 30 seconds for self-diagnosis.
- Clear Legacy Codes:
- Use the diagnostic tool to wipe previous fault codes.
Step 6: Upload Valve Configuration
- Load Valve Profile:
- Select the EBS valve’s firmware file (e.g., .VBF for WABCO).
- Flash Parameters:
- Set valve type (e.g., proportional/modulating), pressure limits, and response curves.
Pro Tip: For retrofits, use “Generic Truck” mode if OEM profiles are unavailable.
Step 7: Pneumatic Pressure Calibration
- Charge the System:
- Build air pressure to 120 PSI.
- Calibrate via Diagnostics:
- Follow tool prompts to set cut-in/cut-out pressures and balance primary/secondary circuits.
Step 8: Signal Validation
- Static Test:
- Command 50% brake application via the tool. Verify valve actuation (audible click).
- Dynamic Test:
- Drive at 20 mph and trigger emergency braking. Confirm ABS/EBS intervention.
Step 9: Leak-Down Test
- Parking Brake Test:
- Apply parking brake, then monitor pressure drop (<2 PSI per minute).
- Service Brake Test:
- Hold pedal for 2 minutes. Pressure drop >5 PSI indicates leaks.
Step 10: Final Documentation
- Print Calibration Report:
- Attach to the vehicle’s service history.
- Label Valves:
- Use heat-resistant tags (e.g., “EBS Primary – SN:12345”).
Section 3: Troubleshooting Common Issues
Problem 1: ECU Communication Failure
- Causes:
- CAN wiring incorrect or unshielded.
- Missing termination resistor.
- Fix: Recheck CAN resistance (60 Ω at each end) and shield grounding.
Problem 2: Delayed Brake Response
- Causes:
- Undersized pneumatic lines.
- Incorrect valve response curve.
- Fix: Upgrade to ½” lines and recalibrate valve ramp-up time.
Conclusion
Installing EBS valves demands precision in mechanical, electrical, and software domains—but the payoff is braking systems that blend safety with adaptability. By methodically following these 10 steps, you’ll dodge common pitfalls like signal noise or pressure leaks, ensuring compliance and driver confidence.
Upgrade Your Toolkit: Explore ACME’s EBS retrofit kits here, featuring pre-terminated harnesses and plug-and-play valve profiles.