Introduction:
A vehicle’s Anti-lock Braking System (ABS) relies on accurate wheel speed data to prevent wheel lockup during hard braking. Faulty ABS sensor installation or calibration can lead to erratic braking behavior, false error codes, or even system failure. This guide walks you through ABS sensor mounting, shielded wiring techniques, and diagnostic validation to ensure reliable signal integrity and compliance with OEM standards. Perfect for technicians and enthusiasts working on cars, trucks, or trailers.
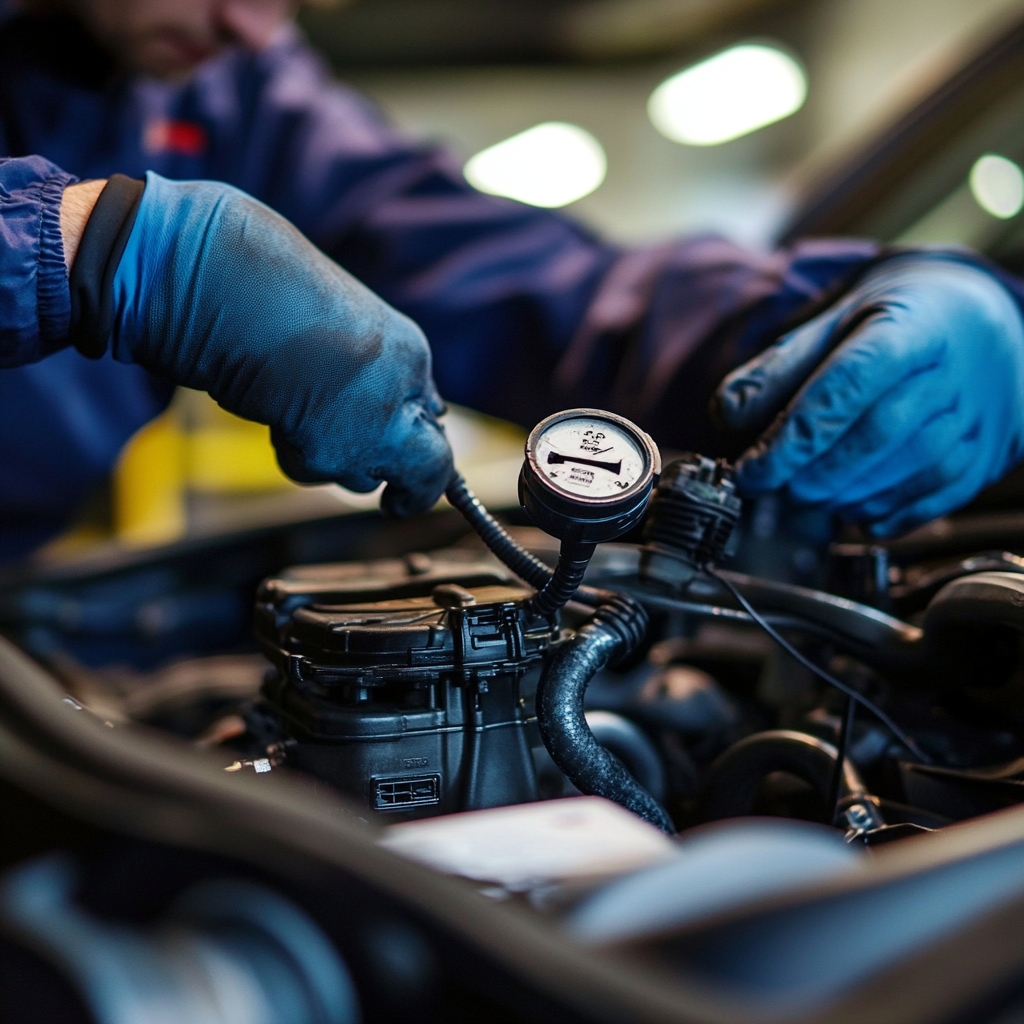
​Section 1: Tools and Safety Precautions
Tools Required:
- ABS sensor (active or passive type, matched to vehicle).
- Torque wrench (3–5 Nm range for sensor bolts).
- Oscilloscope or ABS-compatible diagnostic scanner.
- Wire strippers, soldering iron, and heat-shrink tubing.
- Shielding tape or braided conduit.
- Multimeter (for continuity and resistance checks).
- Wheel bearing play gauge (to measure sensor gap).
Safety First:
- Disconnect the vehicle battery to prevent electrical shorts.
- Use jack stands for wheel removal, never rely solely on a hydraulic jack.
​Section 2: Sensor Positioning and Mounting
​Step 1: Locate the Sensor Mounting Point
ABS sensors are typically mounted near the wheel bearing hub or tone ring. Common configurations:
- ​Passive Sensors: Use a magnetic pickup facing a toothed tone ring (common in older vehicles).
- ​Active Sensors: Hall-effect or magneto-resistive sensors paired with magnetic encoders (modern vehicles).
Key Tip: Refer to the vehicle’s service manual for sensor gap specifications (usually 0.3–1.0 mm). Incorrect gaps cause erratic signals.
​Step 2: Clean and Prep the Mounting Surface
- Remove rust or debris from the sensor mounting hole with a wire brush.
- Apply anti-seize compound to avoid corrosion (except on magnetic sensors).
​Step 3: Secure the Sensor
- Insert the sensor into the mounting bore by hand to avoid cross-threading.
- Tighten the bolt to OEM torque specs (e.g., 4 Nm for most passenger vehicles). Over-tightening can crack the sensor.
Pitfall Alert: Passive sensors require precise alignment with the tone ring teeth. Use a feeler gauge to verify clearance.
​Section 3: Shielding the Wiring Harness
​Step 4: Route Wiring Away from EMI Sources
- ​Avoid: High-current cables (e.g., alternator wiring), ignition coils, and electric motors.
- ​Ideal Path: Secure the harness along the vehicle frame using nylon ties, maintaining a 6-inch gap from noise sources.
​Step 5: Shielded Cable Techniques
For non-shielded factory harnesses:
- Wrap the ABS sensor wires with ​copper shielding tape (grounded at one end).
- Encase the bundle in ​braided conduit for physical protection.
Pro Tip: Splice shielding layers using solder and heat-shrink tubing—never use crimp connectors, which degrade EMI resistance.
​Step 6: Ground the Shield
- Connect the shielding layer to the vehicle chassis via a dedicated ground point.
- Check resistance: <0.5 Ω between shield ground and battery negative terminal.
​Section 4: Diagnostic Validation
​Step 7: Resistance and Continuity Checks
- ​Passive Sensors: Measure resistance between terminals (typically 800–1400 Ω). Replace if out of range.
- ​Active Sensors: Verify 12V supply voltage and ground continuity.
​Step 8: Oscilloscope Signal Analysis
- Connect the oscilloscope to the sensor output wires.
- Rotate the wheel by hand (or use a drill to spin the hub).
Healthy Signal Examples:
- ​Passive Sensors: AC sine wave (amplitude increases with wheel speed).
- ​Active Sensors: Square wave with consistent duty cycle.
Red Flags:
- Flatlined signal: Broken sensor or wiring.
- Irregular waveform: EMI interference or damaged tone ring.
​Step 9: Diagnostic Scanner Validation
- Use an ABS-compatible scanner (e.g., Autel MaxiCOM or Snap-on Verus).
- Check live data for all wheel speed sensors while driving at 20 mph.
Expected Result: All sensors report within ±2% of each other.
​Section 5: Troubleshooting Common Issues
​Problem 1: Erratic ABS Activation
- ​Causes:
- Sensor gap too wide or inconsistent.
- Damaged tone ring (chipped/missing teeth).
- ​Fix: Adjust gap or replace the tone ring.
​Problem 2: Intermittent Signal Loss
- ​Causes:
- Poor shielding grounding.
- Corroded connector pins.
- ​Fix: Clean connectors with contact spray and re-ground the shield.
​Problem 3: ABS Warning Light On
- ​Causes:
- Open/short circuit in wiring.
- Sensor mismatch (e.g., wrong frequency for the ABS module).
- ​Fix: Perform a continuity test and verify part compatibility.
​Conclusion
Proper ABS sensor installation isn’t just about bolting components in place—it demands precision in positioning, EMI-proof wiring, and thorough signal validation. Ignoring shielding or skipping diagnostic tests often leads to phantom ABS faults that frustrate technicians and endanger drivers. By following this guide, you’ll eliminate noise-induced errors and deliver braking systems that perform flawlessly in all conditions.
Upgrade Tip: For heavy-duty or high-vibration applications, consider ACME’s ruggedized ABS sensors with integrated shielding explore here, designed to withstand off-road and commercial vehicle abuse.
Hi, this is a comment.
To get started with moderating, editing, and deleting comments, please visit the Comments screen in the dashboard.
Commenter avatars come from Gravatar.