Introduction:
In sub-zero temperatures, air brake systems face a deadly threat: ice. Condensation in air lines can freeze, blocking pressure flow and crippling braking performance. For truckers and fleet managers operating in Arctic climates, a single frozen line can mean stranded cargo, costly downtime, or even accidents. This guide delivers battle-tested strategies to winterize air brake systems, combining heated air dryers, insulated lines, and freeze-resistant valves to ensure reliability at -40°F/C.
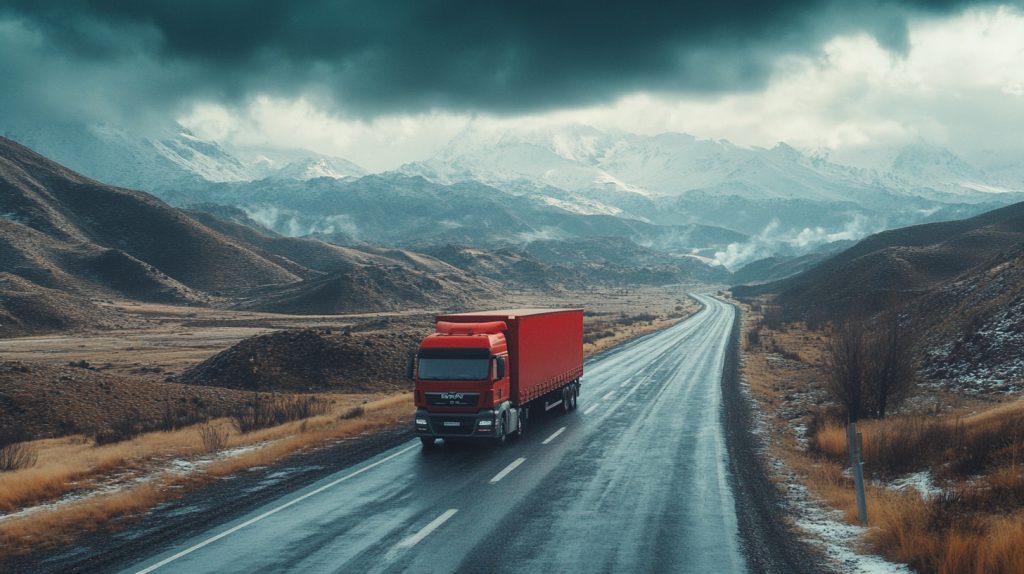
​Section 1: Tools and Materials Checklist
Winterization Essentials:
- ​Heated air dryer (e.g., ACME FrostGuard Pro with 12V/24V compatibility).
- ​Self-sealing foam insulation (1/2” wall thickness, rated for -50°F).
- ​Electric heated drain valves (auto-cycling or manual override).
- ​Silicone spray (for rubber component protection).
- ​Pressure tester (0–200 PSI range).
- ​Heat gun (for insulation adhesion in cold environments).
Safety Gear:
- Insulated gloves (to handle metal components at extreme temps).
- Circuit tester (to prevent electrical shorts during dryer install).
​Section 2: Installing a Heated Air Dryer
​Step 1: Choose the Right Dryer
- ​Compressor Compatibility: Match dryer CFM rating to the compressor’s output (e.g., 18 CFM dryer for a 15 CFM compressor).
- ​Power Source: Opt for 24V systems in heavy-duty trucks to handle higher amperage.
​Step 2: Mounting the Dryer
- ​Location: Install downstream of the compressor but before the wet tank. Avoid engine hotspots (>200°F).
- ​Secure the Bracket: Use vibration-damping mounts to prevent fatigue cracks.
- ​Wiring: Connect to a fused ignition-switched circuit. Use 10-gauge wire for runs >3 feet.
Pro Tip: Add a manual bypass valve for emergency operation if the dryer fails.
​Section 3: Insulating Air Lines
​Step 3: Select Insulation Materials
- ​Closed-cell foam: Prevents moisture absorption (critical for aluminum lines).
- ​Fiberglass sleeves: For high-heat zones near the exhaust.
- ​Adhesive-backed insulation: Simplifies application on curved surfaces.
​Step 4: Insulation Installation
- ​Clean Lines: Wipe lines with isopropyl alcohol to remove grease.
- ​Wrap Tightly: Spiral-cut insulation for bends and secure with UV-resistant zip ties.
- ​Seal Joints: Apply silicone tape at fittings to block cold air ingress.
Critical Areas:
- ​Gladhands: Double-layer insulation with removable covers for coupling.
- ​Brake Chambers: Use pre-molded neoprene covers with adhesive flaps.
​Section 4: Upgrading Drain Valves
​Step 5: Install Heated Drain Valves
- ​Electric Heating Elements: Ideal for automatic moisture expulsion (e.g., ACME AutoDrain 24V).
- ​Pneumatic Valves: Use compressed air to cycle drains (no electrical dependency).
Installation Steps:
- Replace OEM drain valves on wet tanks and reservoirs.
- For electric valves: Wire to a timer circuit (e.g., cycle every 30 minutes).
- For pneumatic valves: Connect to the parking brake circuit for post-trip draining.
Winter Mode: Adjust valve cycle frequency based on humidity (daily in coastal climates).
​Section 5: Anti-Freeze Additives and Lubrication
​Step 6: Apply Silicone Spray
- Spray on rubber hoses, O-rings, and diaphragm seals to prevent brittleness.
​Step 7: Use Alcohol-Based Air Line Antifreeze
- ​Methanol Injection: Add 1–2 oz. per 100 gallons of air tank capacity.
- ​Caution: Avoid isopropyl alcohol—it can degrade polyurethane components.
​Section 6: Post-Installation Testing
​Step 8: Pressure Drop Test
- Charge the system to 120 PSI.
- Let sit overnight in freezing temps.
- Acceptable drop: <5 PSI over 8 hours.
​Step 9: Ice Simulation Test
- Spray water on gladhands and valves, then freeze to -20°F. Verify no blockages during brake application.
​Section 7: Troubleshooting Frozen Brake Systems
​Problem 1: Frozen Gladhands
- ​Quick Fix: Use a portable heat blanket or engine coolant-fed thawing kit.
​Problem 2: Ice in Air Dryer
- ​Cause: Overloaded dryer or saturated desiccant.
- ​Fix: Replace desiccant and install a pre-cooler coil upstream.
​Conclusion
Winterizing air brake systems isn’t optional in extreme climates—it’s a lifeline. By integrating heated dryers, armored insulation, and smart drain valves, fleets can conquer ice-bound routes with confidence. Remember: Proactive winter prep costs far less than a single freeze-related breakdown.
Need Arctic-Grade Parts? Explore ACME’s winterization kits here, featuring plug-and-play heated dryers and NSF-certified insulation.