In the intricate symphony of internal combustion engines, timing kits serve as the conductor’s baton, precisely coordinating the opening and closing of intake and exhaust valves with piston movement. These critical assemblies determine the engine’s breathing efficiency, power output, and emissions performance. As modern engines push the boundaries of performance and efficiency, timing kits have evolved from simple mechanical components to sophisticated systems incorporating advanced materials, precision manufacturing, and electronic controls. This comprehensive technical analysis explores the complete ecosystem of timing kits, their functional principles, advanced technological implementations, and the transformative impact these systems have on contemporary engine design.
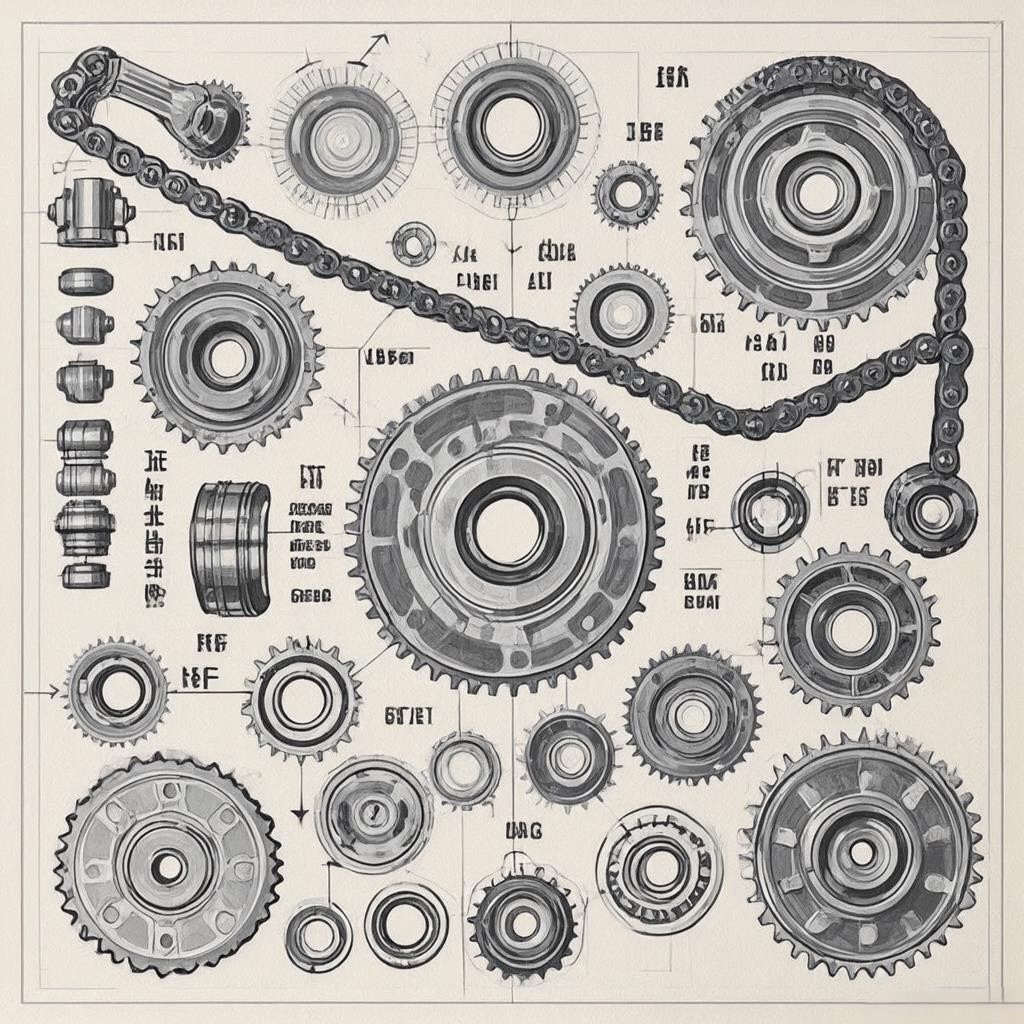
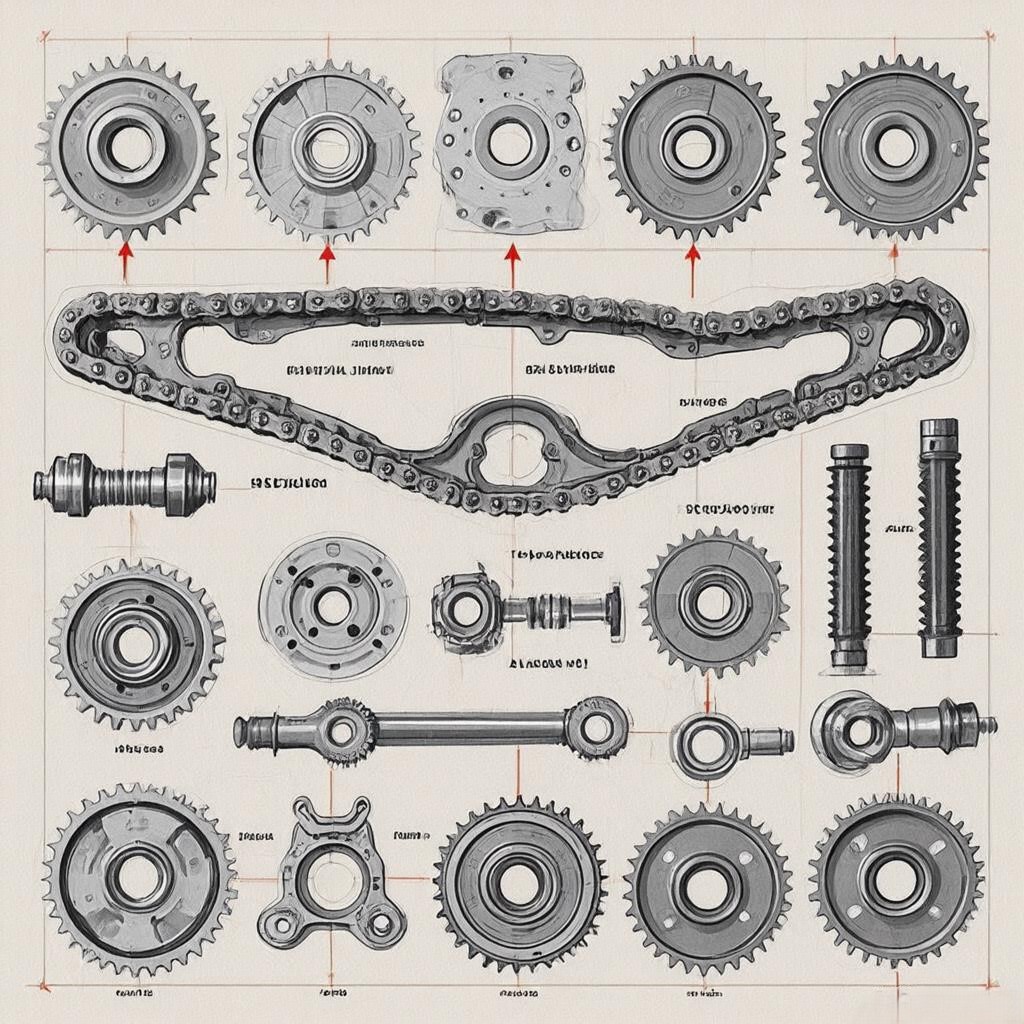
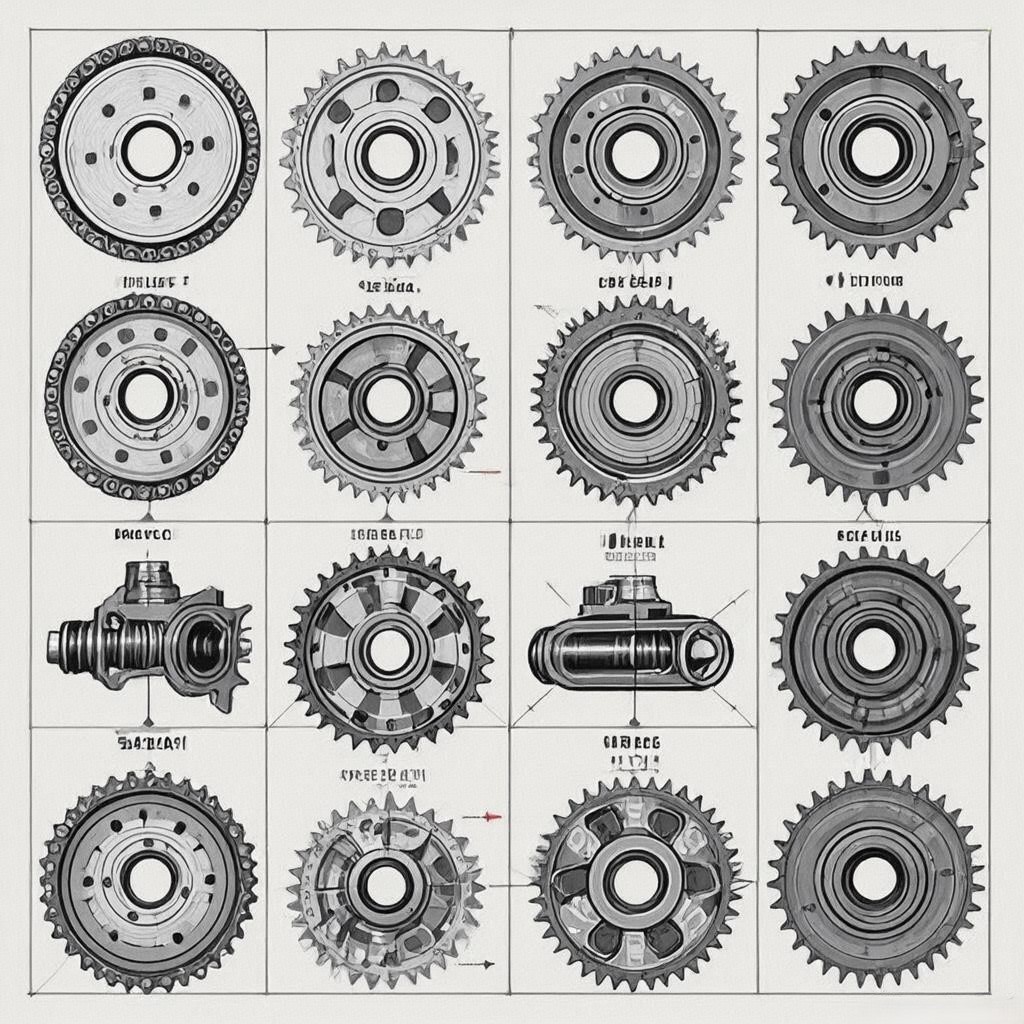
​​1. Fundamental Principles and Technical Significance​​
Timing kits represent the mechanical heartbeat of engine operation, synchronizing valve events with piston motion to optimize the four-stroke cycle. Their precision directly affects:
- ​​Volumetric efficiency​​: Proper timing maximizes air-fuel charge intake
- ​​Combustion quality​​: Accurate valve overlap enhances scavenging
- ​​Emission control​​: Optimized timing reduces unburned hydrocarbons
- ​​Mechanical efficiency​​: Minimizes pumping losses and friction
​​Technical specifications​​:
- Timing accuracy: ±0.5° crankshaft angle
- Component tolerances: 0.01mm for critical surfaces
- Operating temperature: -40°C to +150°C
- Service life: 200,000+ km under normal conditions
​​Industry impact​​: Modern timing kits contribute to 15-20% of an engine’s fuel efficiency improvements and enable compliance with Euro 6d and Tier 3 emission standards through precise valve control.
​​2. Core Components and Functional Architecture​​
​​2.1 Timing Chain/Belt Assemblies​​
​​Chain-driven systems​​:
- ​​Roller chains​​: Precision-machined with 0.1mm pitch accuracy
- ​​Hydraulic tensioners​​: Automatic pressure adjustment (0.5-3.0 bar)
- ​​Guide rails​​: Polymer-coated steel for noise reduction
​​Belt-driven systems​​:
- ​​Fiber-reinforced rubber​​: Aramid fibers with 3x steel strength-to-weight ratio
- ​​Synchronous pulleys​​: Hardened steel with 0.005mm surface finish
- ​​Automatic tensioners​​: Spring-loaded with hydraulic damping
​​Performance metrics​​:
- Tensile strength: 1,000-3,000MPa for chains
- Elongation: <0.2% for belts over service life
- Noise level: <65dB(A) at 2,000rpm
​​2.2 Camshaft Phasers​​
​​Variable timing mechanisms​​:
- ​​Hydraulic phasers​​: Oil-controlled vane-type actuators
- ​​Electric phasers​​: Brushless DC motors with 0.1° resolution
- ​​Mid-position locking​​: Mechanical detents for fail-safe operation
​​Control parameters​​:
- ​​Timing range​​: ±40° crankshaft angle adjustment
- ​​Response time​​: <50ms for hydraulic, <10ms for electric
- ​​Flow requirements​​: 1-5L/min oil supply at 3-5 bar pressure
​​Advanced features​​:
- ​​Closed-loop control​​: Cam position sensors with 0.1° accuracy
- ​​Adaptive learning​​: Self-adjusting for wear compensation
- ​​Fail-safe modes​​: Default timing positions
​​2.3 Tensioning and Guide Systems​​
​​Automatic tensioners​​:
- ​​Hydraulic dampers​​: Oil-filled chambers with orifice control
- ​​Spring-loaded designs​​: Progressive force characteristics
- ​​Wear indicators​​: Visual or electronic wear detection
​​Chain guides​​:
- ​​Polymer composites​​: PTFE-based materials with 0.3 coefficient of friction
- ​​Steel-backed designs​​: Reinforced with 1mm steel plates
- ​​Wear-resistant coatings​​: Diamond-like carbon for extended life
​​Performance metrics​​:
- Tensioner force: 5-20N dynamic range
- Guide wear rate: <0.01mm/10,000km
- Noise reduction: 3-5dB(A) improvement
​​3. Advanced Timing System Technologies​​
​​3.1 Variable Valve Timing (VVT) Systems​​
​​Continuous variable systems​​:
- ​​VANOS (BMW)​​: Hydraulic phaser with 60° adjustment range
- ​​VVT-i (Toyota)​​: Electric motor-driven with 0.1° resolution
- ​​VTEC (Honda)​​: Switchable cam profiles for high/low RPM
​​Discrete variable systems​​:
- ​​Cam switching​​: Dual-profile camshafts with solenoid actuation
- ​​Phase shifting​​: Limited-angle adjustment (10-20° range)
- ​​Lift modulation​​: Variable valve lift systems (e.g., Multi-Air)
​​Control strategies​​:
- ​​Load-based timing​​: MAP sensor-driven adjustments
- ​​Speed-dependent optimization​​: RPM-linked phasing
- ​​Thermal compensation​​: Temperature-corrected timing maps
​​Performance benefits​​:
- ​​Fuel economy​​: 5-10% improvement in light-load conditions
- ​​Power output​​: 8-15% increase at high RPM
- ​​Emissions​​: 15-30% reduction in cold-start HC emissions
​​3.2 Integrated Timing Chain Covers​​
​​Multi-functional designs​​:
- ​​Oil galleries​​: Integrated lubrication channels
- ​​Mounting provisions​​: Integrated accessory brackets
- ​​Acoustic damping​​: Sound-absorbing materials
​​Material innovations​​:
- ​​Magnesium alloys​​: Weight reduction of 30-40%
- ​​Long-fiber composites​​: Impact-resistant structures
- ​​Thermal barrier coatings​​: Reduced heat transfer
​​Sealing systems​​:
- ​​Multi-layer gaskets​​: Steel core with rubber coating
- ​​Laser-welded joints​​: Leak-proof construction
- ​​Form-in-place gaskets​​: Automated application
​​Performance metrics​​:
- Oil retention: <0.1mL leakage over 24 hours
- Vibration damping: 10-15% noise reduction
- Temperature resistance: Up to 150°C continuous operation
​​3.3 Smart Timing Systems​​
​​Sensor integration​​:
- ​​Camshaft position sensors​​: Hall-effect with 0.1° resolution
- ​​Chain wear sensors​​: Capacitive or inductive detection
- ​​Tensioner monitoring​​: Pressure and position feedback
​​Predictive maintenance​​:
- ​​Wear prediction algorithms​​: Based on operating conditions
- ​​Health monitoring​​: Real-time performance tracking
- ​​Service alerts​​: Predictive diagnostics
​​Electrification readiness​​:
- ​​48V system compatibility​​: Electric phaser integration
- ​​Hybrid system synchronization​​: Coordinated timing with electric motors
- ​​Over-the-air updates​​: Software calibration adjustments
​​4. System Integration and Engine Applications​​
​​4.1 Gasoline Engines​​
​​High-performance applications​​:
- ​​Dual overhead camshafts​​: Independent timing control for intake/exhaust
- ​​Variable intake manifolds​​: Synchronized with cam phasing
- ​​Turbocharger coordination​​: Boost pressure-timed valve events
​​Efficiency-focused designs​​:
- ​​Atkinson cycle adaptation​​: Late intake valve closing
- ​​Cylinder deactivation​​: Selective camshaft operation
- ​​Start-stop compatibility​​: Rapid timing resynchronization
​​Performance metrics​​:
- Redline capability: Up to 8,000rpm with chain systems
- Emission compliance: Euro 6d TEMP standards
- Fuel economy: 20-30% improvement in NEDC cycle
​​4.2 Diesel Engines​​
​​High-pressure common rail coordination​​:
- ​​Injection-timing synchronization​​: Precise valve-pump timing
- ​​EGR integration​​: Exhaust gas recirculation valve control
- ​​Turbocharger matching​​: Variable geometry turbine timing
​​Low-emission strategies​​:
- ​​Exhaust aftertreatment timing​​: SCR and DPF regeneration coordination
- ​​Cold-start optimization​​: Rapid warm-up valve sequences
- ​​Particulate control​​: GPF synchronization
​​Durability features​​:
- ​​Heavy-duty chain designs​​: Double-row roller chains
- ​​Enhanced lubrication​​: High-pressure oil jets
- ​​Thermal management​​: Advanced cooling passages
​​Performance metrics​​:
- Torque output: 500-1,000Nm range
- Emission reduction: 90% NOx reduction with SCR
- Service intervals: Up to 500,000km
​​4.3 Hybrid and Alternative Fuel Engines​​
​​Hybrid system integration​​:
- ​​Electric motor synchronization​​: Coordinated start-stop timing
- ​​Regenerative braking support​​: Optimal valve timing for coasting
- ​​Power-split management​​: Variable timing for hybrid modes
​​Natural gas adaptations​​:
- ​​High-octane timing maps​​: Optimized for CNG/LPG
- ​​Lean-burn compatibility​​: Extended valve overlap
- ​​Combustion stability​​: Specialized ignition timing
​​Hydrogen engine modifications​​:
- ​​Ultra-lean burn timing​​: Extremely early intake closing
- ​​Fast combustion cycles​​: Rapid valve opening/closing
- ​​Material compatibility​​: Hydrogen-resistant sealing materials
​​Performance metrics​​:
- Fuel efficiency: 10-15% improvement for hybrids
- Emission levels: Near-zero CO2 output
- Cold-start capability: -30°C startup without glow plugs
​​5. Design Challenges and Engineering Solutions​​
​​5.1 Precision Manufacturing Requirements​​
​​Machining tolerances​​:
- ​​Camshaft lobes​​: ±0.005mm surface finish
- ​​Chain pins​​: 0.001mm diameter control
- ​​Sprocket teeth​​: 0.01mm profile accuracy
​​Assembly processes​​:
- ​​Automated fitting​​: Robot-assisted component installation
- ​​Laser alignment​​: Precision timing verification
- ​​Torque management​​: Controlled fastener tightening
​​Quality control​​:
- ​​Coordinate measuring machines (CMM)​​: 3D dimensional inspection
- ​​End-of-line testing​​: Dynamic timing verification
- ​​Statistical process control​​: Six-sigma manufacturing
​​5.2 Durability and Reliability Enhancement​​
​​Material selection​​:
- ​​Chain components​​: Vacuum-melted steel alloys
- ​​Belt materials​​: EPDM rubber with aramid reinforcement
- ​​Phaser housings​​: Powder-forged steel
​​Protective coatings​​:
- ​​Diamond-like carbon​​: 0.1μm friction-reducing layer
- ​​Thermal barrier coatings​​: ZrO2-based ceramics
- ​​Corrosion protection​​: Electroless nickel plating
​​Testing protocols​​:
- ​​Endurance testing​​: 1,000-hour dynamometer runs
- ​​Temperature cycling​​: -40°C to +150°C, 1,000 cycles
- ​​Salt spray exposure​​: 2,000 hours for corrosion resistance
​​5.3 Noise and Vibration Control​​
​​Acoustic engineering​​:
- ​​Chain silencers​​: Polymer-coated guides
- ​​Balancer shafts​​: Counter-rotating weights
- ​​Mounting systems​​: Rubber-isolated brackets
​​Dynamic balancing​​:
- ​​High-speed balancing​​: ±0.1gmm imbalance correction
- ​​Resonance avoidance​​: Critical speed analysis
- ​​Vibration damping​​: Constrained-layer damping materials
​​Performance metrics​​:
- Noise reduction: 5-8dB(A) improvement
- Vibration isolation: 30% reduction in vibration transmission
- Service life: 20% longer component durability
​​6. Testing and Validation Methodologies​​
​​6.1 Component-Level Testing​​
​​Chain/belt testing​​:
- ​​Endurance testing​​: 10,000km equivalent cycles
- ​​Load testing​​: 150% working load capacity
- ​​Aging tests​​: Temperature/humidity cycling
​​Phaser testing​​:
- ​​Life cycle testing​​: 100 million actuation cycles
- ​​Pressure testing​​: 150% working pressure
- ​​Temperature testing​​: -40°C to +150°C operation
​​Sensor validation​​:
- ​​Accuracy verification​​: Reference standard comparison
- ​​Response time testing​​: Step input response
- ​​Environmental testing​​: Vibration and temperature exposure
​​6.2 System-Level Validation​​
​​Engine dynamometer testing​​:
- ​​Timing accuracy verification​​: Optical encoder measurement
- ​​Performance mapping​​: BSFC and power output
- ​​Emission testing​​: CVS bag sampling
​​Vehicle testing protocols​​:
- ​​Real-world driving cycles​​: WLTP and FTP-75
- ​​Cold start performance​​: -30°C ambient conditions
- ​​High-altitude testing​​: Up to 3,000m elevation
​​Endurance testing​​:
- ​​1,000-hour durability​​: Continuous operation
- ​​100,000km road testing​​: Real-world conditions
- ​​Thermal cycling​​: -40°C to +125°C, 1,000 cycles
​​6.3 Virtual Validation​​
​​Simulation tools​​:
- ​​Multi-body dynamics​​: Valve train motion analysis
- ​​Finite element analysis (FEA)​​: Stress and fatigue prediction
- ​​Computational fluid dynamics (CFD)​​: Lubrication flow analysis
​​Test scenarios​​:
- ​​10,000+ virtual test cases​​ covering all operating conditions
- ​​Edge case testing​​: Extreme loads and temperatures
- ​​Long-term durability simulation​​: 10-year equivalent cycles
​​7. Market Trends and Future Developments​​
​​7.1 Electrification and 48V Systems​​
​​Key innovations​​:
- ​​Electric cam phasers​​: 48V motor-driven timing adjustment
- ​​Hybrid system synchronization​​: Coordinated ICE and electric motor timing
- ​​Predictive timing control​​: AI-based optimization algorithms
​​Technical challenges​​:
- ​​System integration​​: Combining electrical and mechanical components
- ​​Energy management​​: Optimizing battery usage for timing actuation
- ​​Control complexity​​: Managing multiple timing variables
​​7.2 Advanced Materials and Manufacturing​​
​​Innovative approaches​​:
- ​​3D-printed components​​: Complex geometries for lightweighting
- ​​Carbon fiber timing gears​​: Ultra-lightweight alternatives
- ​​Additive manufacturing​​: Rapid prototyping of new designs
​​Sustainability focus​​:
- ​​Recyclable materials​​: End-of-life considerations
- ​​Energy-efficient manufacturing​​: Reduced carbon footprint
- ​​Smart materials​​: Self-diagnostic capabilities
​​7.3 Smart and Connected Timing Systems​​
​​Emerging technologies​​:
- ​​Over-the-air updates​​: Software calibration adjustments
- ​​Digital twin technology​​: Predictive maintenance and performance monitoring
- ​​AI-based learning algorithms​​: Personalized timing profiles
​​User benefits​​:
- ​​Reduced maintenance​​: Predictive service alerts
- ​​Improved performance​​: Continuous optimization
- ​​Enhanced diagnostics​​: Remote troubleshooting
​​8. Case Studies: Real-World Implementations​​
​​Case Study 1: High-Performance Sports Car Timing System​​
A leading supercar manufacturer implemented a variable timing system with the following results:
- 8,000rpm redline capability
- 30% increase in horsepower at high RPM
- 10% improvement in throttle response
​​Case Study 2: Commercial Diesel Engine Timing Upgrade​​
A global truck manufacturer upgraded their timing system, achieving:
- 5% better fuel economy
- 40% reduction in NOx emissions
- Extended service intervals to 1 million km
​​Conclusion: The Precision Foundation of Modern Engines​​
Timing kits represent the critical synchronization mechanism that enables modern engines to achieve unprecedented levels of performance, efficiency, and emissions control. As engines continue to evolve with electrification and alternative fuels, these systems will play an increasingly important role in managing complex combustion processes while meeting stringent regulatory requirements.
​​Key takeaways:​​
- Modern timing kits combine chains/belts, phasers, and sensors into integrated systems
- Advanced materials and manufacturing enable higher precision and durability
- Electrification and connectivity are driving the next generation of timing innovations
- Sustainability and digitalization are transforming timing system design
​​Final thought​​: In an era where engine displacements are shrinking but performance demands are increasing, timing kits have become the unsung heroes of modern powertrains. The next generation of these systems will need to balance unprecedented precision requirements with the demands of hybridization, alternative fuels, and environmental sustainability, making them one of the most critical areas of automotive engineering innovation today.
​​Call to Action​​
đź”§ Upgrading your engine’s timing system?
⚙️ Explore our advanced timing kits for improved performance and durability
📊 Request performance data comparing traditional vs. next-generation systems
#TimingKits #EngineTechnology #AutomotiveEngineering #VariableValveTiming #ADAS #Electrification #SmartMobility #FutureOfTransportation #FunctionalSafety #AdvancedManufacturing