The air brake system stands as one of the most critical safety innovations in modern transportation, particularly for heavy-duty vehicles where traditional hydraulic systems fall short. This comprehensive technical analysis explores the complete architecture, operational principles, and advanced technological advancements in air brake systems that make them indispensable for commercial trucks, buses, and trains. From fundamental components to cutting-edge electronic controls, we examine how these systems deliver reliable stopping power while meeting stringent safety standards.
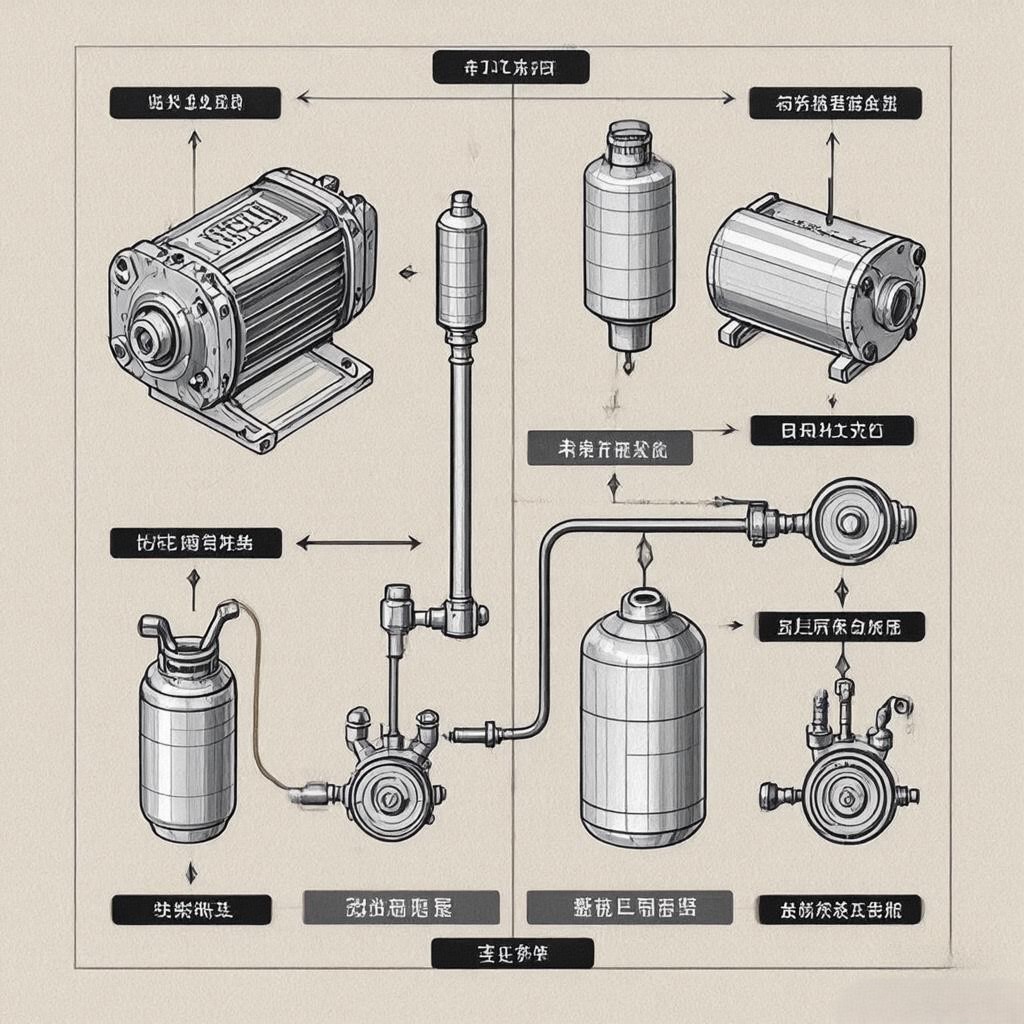
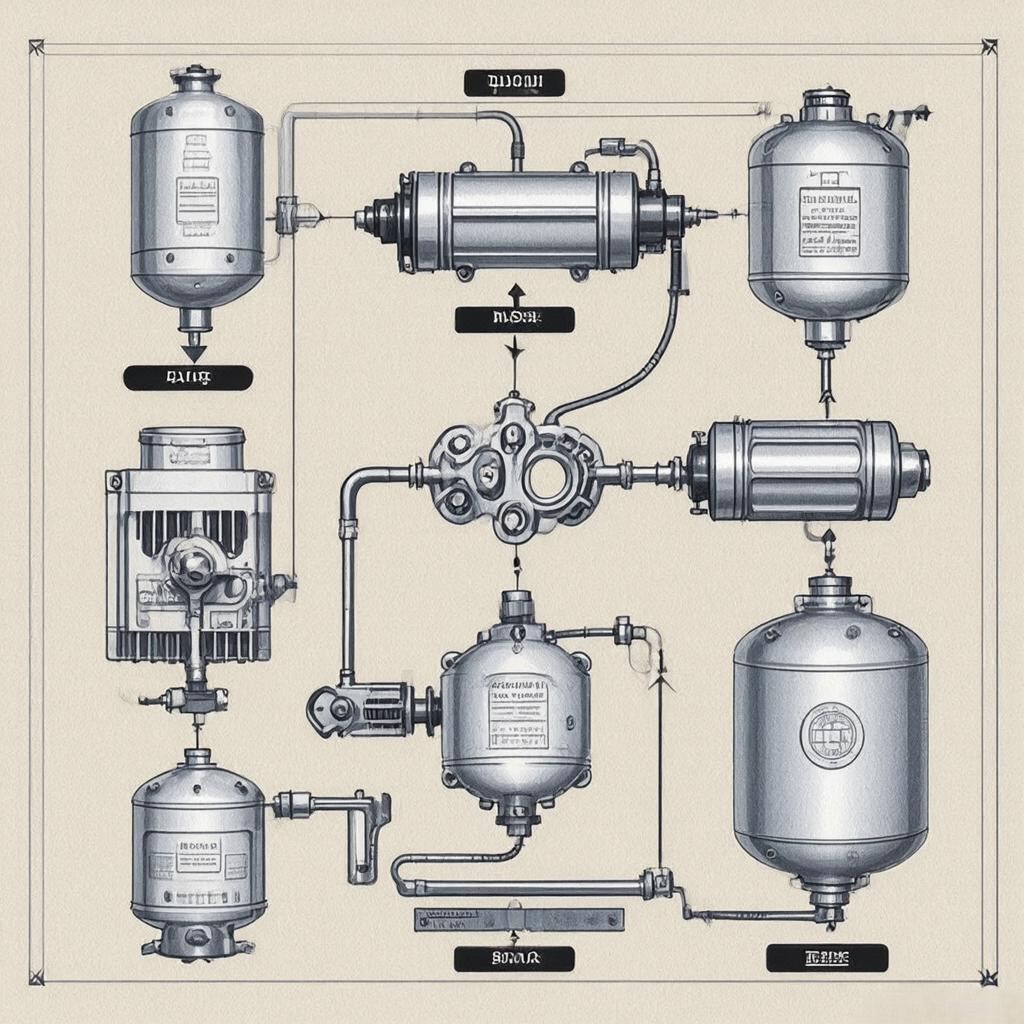
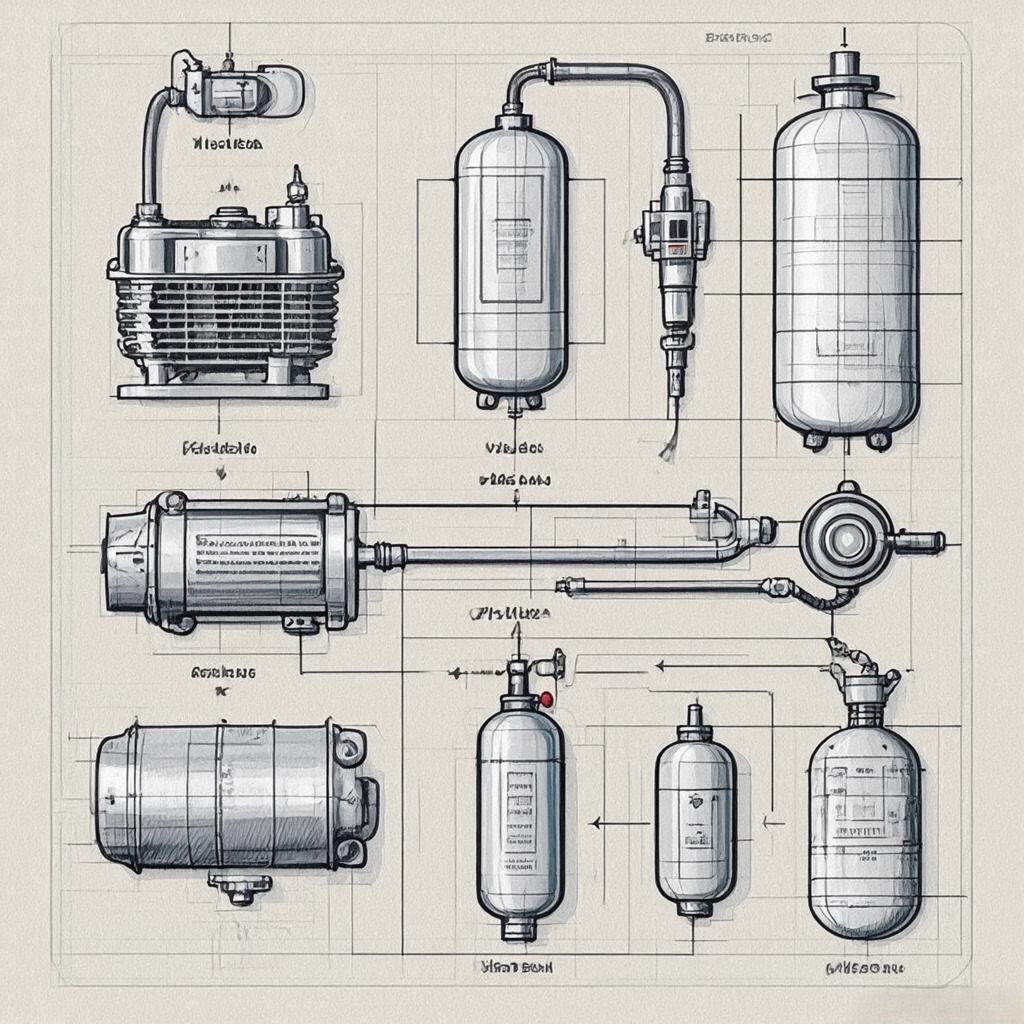
​​1. Fundamental Principles and System Overview​​
Air brake systems utilize compressed air as the power medium to transmit force from the driver’s pedal to the brake mechanisms, offering several key advantages over hydraulic systems:
- ​​Higher pressure capacity​​: Typically operates at 7-12 bar (100-175 psi)
- ​​Fail-safe design​​: Springs apply brakes automatically if air pressure fails
- ​​Scalability​​: Easily adapts to multiple axles and trailers
- ​​Heat dissipation​​: Superior performance under heavy braking conditions
​​Technical specifications​​:
- Maximum operating pressure: 1.2 MPa (174 psi)
- Air consumption: 0.5-2.0 mÂł/min per vehicle
- Response time: <0.5 seconds for full braking application
- Typical system weight: 50-150 kg depending on vehicle size
​​Industry significance​​: Over 90% of commercial trucks and buses worldwide use air brake systems, with the global market valued at 4.2billionin2023andprojectedtoreach6.5 billion by 2030.
​​2. Core Components and Functional Architecture​​
​​2.1 Air Supply System​​
​​Compressor assembly​​:
- ​​Types​​: Reciprocating (piston) or rotary screw compressors
- ​​Capacity​​: 300-1,200 liters/minute at 1.0 MPa
- ​​Materials​​: Aluminum alloy pistons with hardened steel cylinder liners
- ​​Cooling systems​​: Air-cooled or water-cooled configurations
​​Air dryer system​​:
- ​​Desiccant technology​​: Molecular sieve or activated alumina
- ​​Dew point control​​: -40°C to -70°C dew point range
- ​​Regeneration methods​​: Time-based or pressure differential
​​Air reservoirs​​:
- ​​Capacity​​: 100-500 liters per vehicle
- ​​Material​​: Carbon steel with epoxy coating or stainless steel
- ​​Safety features​​: Pressure relief valves (set at 1.25x working pressure)
​​2.2 Control and Distribution System​​
​​Foot brake valve​​:
- ​​Types​​: Graduated release or quick-release designs
- ​​Operation​​: Proportional control of air pressure (0-1.0 MPa)
- ​​Response time​​: <0.3 seconds for full application
​​Trailer control valve​​:
- ​​Types​​: Relay or supply/demand valves
- ​​Function​​: Independent control of up to 4 trailer axles
- ​​Communication​​: Electrical or pneumatic signals
​​Quick-release valves​​:
- ​​Purpose​​: Rapid exhaust of brake chamber air
- ​​Response time​​: <0.1 seconds for full release
- ​​Flow capacity​​: 100-300 liters/minute
​​2.3 Brake Actuation Components​​
​​Brake chambers​​:
- ​​Types​​: Spring brake (fail-safe) and service brake chambers
- ​​Sizes​​: Type 20 (small), Type 30 (medium), Type 30/30 (combination)
- ​​Force output​​: 2,000-10,000 N per chamber
​​Pushrod and slack adjuster​​:
- ​​Material​​: Heat-treated alloy steel
- ​​Adjustment mechanism​​: Manual or automatic (self-adjusting)
- ​​Travel limits​​: 1-3 inches maximum stroke
​​S-cam brakes​​:
- ​​Camshaft design​​: Hardened steel with precision machining
- ​​Brake shoe materials​​: Semi-metallic or low-metallic friction compounds
- ​​Torque output​​: 500-2,000 Nm per wheel
​​Disc brake systems​​:
- ​​Rotor materials​​: Gray cast iron or composite materials
- ​​Caliper types​​: Floating or fixed 4-piston designs
- ​​Pad materials​​: Ceramic or high-performance organic compounds
​​3. Advanced Control Systems and Electronic Integration​​
​​3.1 Electronic Brake Control Systems​​
​​Electronic Control Unit (ECU)​​:
- ​​Microprocessor​​: 32-bit ARM Cortex-M7 with 256KB Flash
- ​​Input sensors​​: Wheel speed, brake pressure, temperature
- ​​Output controls​​: Proportional valve modulation
​​Electronic Brakeforce Distribution (EBD)​​:
- ​​Algorithm​​: Torque-based distribution algorithm
- ​​Response time​​: <100ms for load changes
- ​​Accuracy​​: ±2% force distribution
​​Anti-lock Braking System (ABS)​​:
- ​​Modulation frequency​​: 10-20Hz pulse width modulation
- ​​Wheel speed sensors​​: Hall-effect or inductive types
- ​​Deceleration control​​: ±0.1g resolution
​​3.2 Advanced Driver Assistance Systems (ADAS) Integration​​
​​Automatic Emergency Braking (AEB)​​:
- ​​Detection range​​: 0.5-150 meters (radar/lidar)
- ​​Reaction time​​: <200ms from detection to braking
- ​​Deceleration capability​​: 0.5-1.0g emergency stop
​​Adaptive Cruise Control (ACC)​​:
- ​​Speed control range​​: 30-120 km/h
- ​​Following distance​​: 1-3 seconds adjustable
- ​​Gradient compensation​​: Automatic speed adjustment
​​Brake Assist System (BAS)​​:
- ​​Pedal recognition​​: Force/displacement sensors
- ​​Full braking activation​​: <150ms response time
- ​​Boost pressure​​: 0.5-1.0 MPa additional pressure
​​3.3 Predictive Maintenance Systems​​
​​Condition monitoring sensors​​:
- ​​Vibration sensors​​: Piezoelectric accelerometers
- ​​Temperature sensors​​: Thermocouples and RTDs
- ​​Pressure sensors​​: Piezoresistive MEMS devices
​​Data analytics algorithms​​:
- ​​Machine learning models​​: Predictive failure detection
- ​​Anomaly detection​​: Statistical process control
- ​​Remaining Useful Life (RUL) prediction​​: Based on usage patterns
​​Telematics integration​​:
- ​​Fleet management systems​​: Real-time monitoring
- ​​Wireless communication​​: 4G/LTE or 5G connectivity
- ​​Cloud-based analytics​​: Centralized data processing
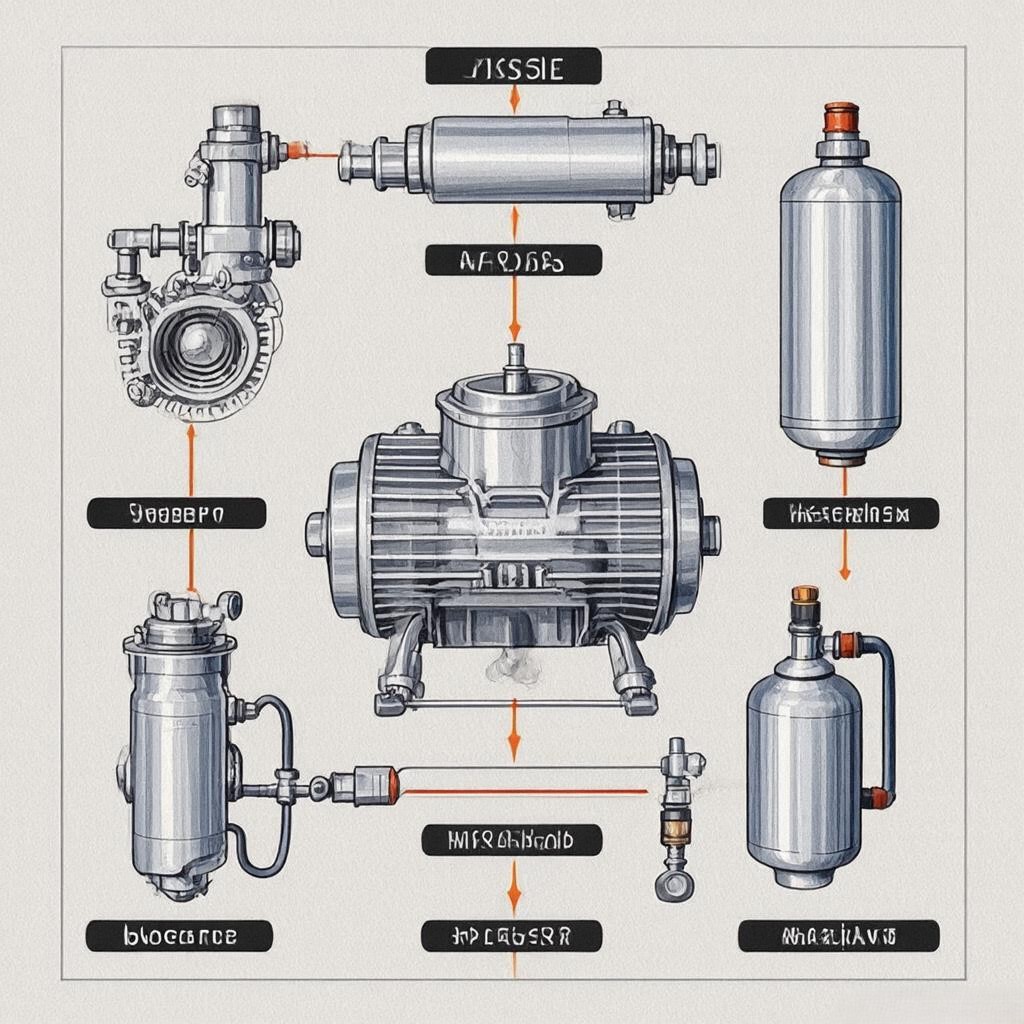
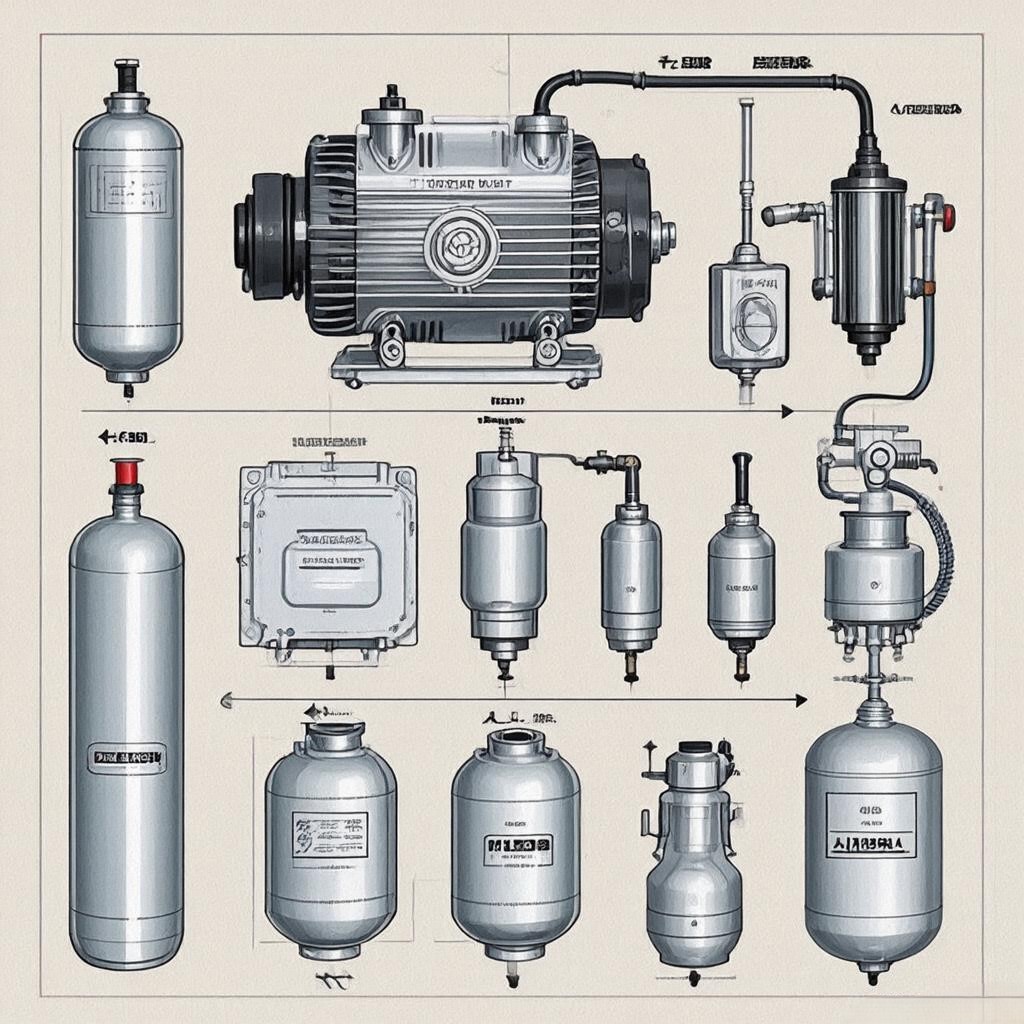
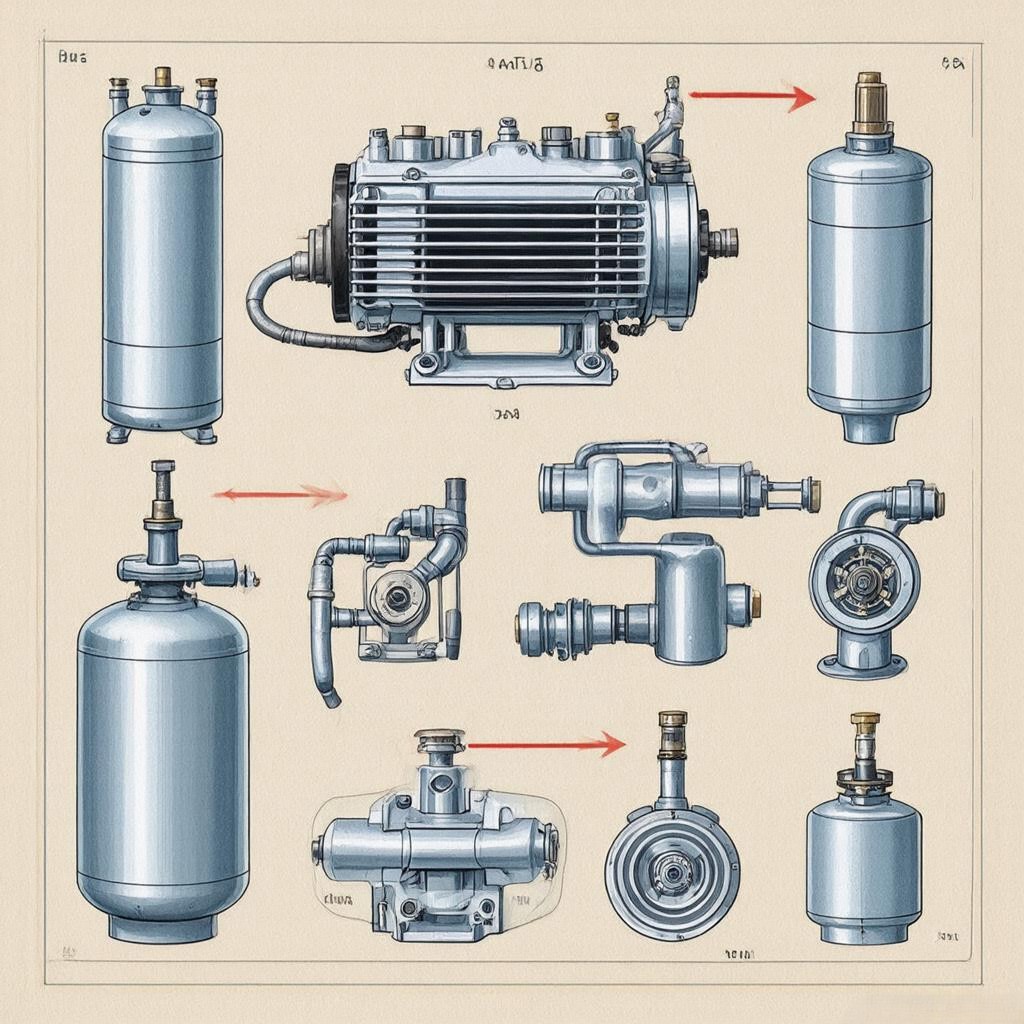
​​4. System Integration and Vehicle Applications​​
​​4.1 Commercial Trucks and Buses​​
​​Tractor-trailer configurations​​:
- ​​Multi-trailer setups​​: Up to 4 trailers with relay valves
- ​​Air suspension integration​​: Height control coordination
- ​​Tire pressure monitoring​​: Integrated with brake system
​​Performance metrics​​:
- Stopping distance: 40-60 meters from 80 km/h (loaded)
- Brake temperature management: <400°C under extreme conditions
- Maintenance interval: 12,000-20,000 km
​​Specialized applications​​:
- ​​Fire trucks​​: Rapid deployment braking systems
- ​​Concrete mixers​​: High-inertia braking requirements
- ​​Dump trucks​​: Load-sensing brake force adjustment
​​4.2 Passenger Coaches and Transit Buses​​
​​Urban transit systems​​:
- ​​Frequent stop capabilities​​: 0.2g deceleration rates
- ​​Low-floor accessibility​​: Compact brake components
- ​​Noise reduction​​: Muffled exhaust ports
​​Intercity coaches​​:
- ​​High-speed braking​​: 0.35g deceleration at 100 km/h
- ​​Tire wear optimization​​: Electronic brake proportioning
- ​​Passenger comfort​​: Smooth brake modulation
​​Safety features​​:
- ​​Hill start assist​​: Automatic brake hold
- ​​Emergency exit coordination​​: Door interlock with brakes
- ​​Fire suppression​​: Brake system temperature monitoring
​​4.3 Rail Applications​​
​​Locomotive braking systems​​:
- ​​Dynamic braking integration​​: Regenerative braking coordination
- ​​Distributed power control​​: Multiple locomotive synchronization
- ​​Grade braking algorithms​​: Automated speed control
​​Metro and light rail​​:
- ​​High-frequency operation​​: 30-second headways
- ​​Regenerative braking​​: Up to 30% energy recovery
- ​​Automatic train protection (ATP) integration​​
​​Freight railcars​​:
- ​​Distributed brake systems​​: Individual car control
- ​​Load sensing​​: Automatic brake force adjustment
- ​​Long-distance operation​​: Minimal maintenance requirements
​​5. Design Challenges and Engineering Solutions​​
​​5.1 Reliability and Safety Assurance​​
​​Redundancy design​​:
- ​​Dual air circuits​​: Independent supply paths
- ​​Fail-safe mechanisms​​: Spring-applied parking brakes
- ​​Emergency backup​​: Manual brake application
​​Testing protocols​​:
- ​​Burst pressure testing​​: 1.5x working pressure
- ​​Endurance testing​​: 1,000,000 brake applications
- ​​Environmental testing​​: -40°C to +85°C, 100% humidity
​​Certification standards​​:
- ​​SAE J1470​​: Air brake performance standards
- ​​ISO 26867​​: Railway applications
- ​​ECE R13​​: Commercial vehicle braking
​​5.2 Weight and Space Optimization​​
​​Material innovations​​:
- ​​Aluminum alloy components​​: Weight reduction of 30-50%
- ​​Composite materials​​: For non-structural parts
- ​​Miniaturized valves​​: High-flow in compact packages
​​Design strategies​​:
- ​​Modular assemblies​​: Standardized components
- ​​Integrated manifolds​​: Reduced plumbing requirements
- ​​Compact chambers​​: Optimized force-to-size ratio
​​Manufacturing techniques​​:
- ​​Additive manufacturing​​: Complex geometries
- ​​Precision casting​​: For critical components
- ​​Automated assembly​​: Consistent quality control
​​5.3 Environmental and Regulatory Compliance​​
​​Emissions control​​:
- ​​Oil carryover reduction​​: Advanced coalescing filters
- ​​Particulate filtration​​: Sub-micron air cleanliness
- ​​Refrigerant management​​: For air dryer systems
​​Noise reduction​​:
- ​​Acoustic insulation​​: Sound-absorbing materials
- ​​Vibration damping​​: Mounting system design
- ​​Exhaust silencing​​: Muffler designs
​​Recycling and end-of-life​​:
- ​​Material separation​​: Design for disassembly
- ​​Hazardous material management​​: Proper disposal protocols
- ​​Component reuse​​: Refurbishment programs
​​6. Testing and Validation Methodologies​​
​​6.1 Component-Level Testing​​
​​Air compressor testing​​:
- ​​Flow rate measurement​​: ±1% accuracy
- ​​Pressure stability​​: ±0.02 MPa over time
- ​​Temperature rise​​: <50°C temperature increase
​​Brake chamber testing​​:
- ​​Force output verification​​: ±2% tolerance
- ​​Stroke measurement​​: Precision dial indicators
- ​​Leak testing​​: Helium mass spectrometry
​​Valve testing​​:
- ​​Response time measurement​​: High-speed data acquisition
- ​​Flow coefficient determination​​: CV value calculation
- ​​Pressure drop analysis​​: Across full flow range
​​6.2 System-Level Validation​​
​​Vehicle testing protocols​​:
- ​​Braking distance tests​​: Wet/dry pavement conditions
- ​​Fade resistance tests​​: 10 consecutive 0.5g stops
- ​​Temperature rise tests​​: Continuous braking monitoring
​​Performance metrics​​:
- Stopping distance consistency: ±3% variation
- Brake balance: ±5% between axles
- System reliability: >99.9% uptime
​​Environmental testing​​:
- ​​Salt spray exposure​​: 1,000 hours minimum
- ​​Vibration testing​​: 15g RMS, 10-2,000Hz
- ​​Dust ingress testing​​: IP6x rated components
​​6.3 Virtual Validation​​
​​Simulation tools​​:
- ​​Computational fluid dynamics (CFD)​​: Airflow optimization
- ​​Finite element analysis (FEA)​​: Structural integrity
- ​​Multibody dynamics​​: Vehicle braking dynamics
​​Test scenarios​​:
- ​​10,000+ virtual test cases​​ covering all conditions
- ​​Edge case testing​​: Extreme loads and temperatures
- ​​Long-term durability simulation​​: 10-year equivalent cycles
​​7. Market Trends and Future Developments​​
​​7.1 Electrification and Hybrid Systems​​
​​Key innovations​​:
- ​​Electrically-assisted braking​​: Regenerative braking coordination
- ​​Air-over-hydraulic systems​​: Combined power media
- ​​Smart compressor control​​: Variable speed drives
​​Technical challenges​​:
- ​​System integration​​: Combining multiple power sources
- ​​Energy management​​: Optimizing braking energy recovery
- ​​Safety validation​​: New failure modes analysis
​​7.2 Advanced Materials and Manufacturing​​
​​Innovative approaches​​:
- ​​3D-printed components​​: Complex geometries
- ​​Carbon fiber reinforced polymers​​: Weight reduction
- ​​Additive manufacturing​​: Rapid prototyping
​​Sustainability focus​​:
- ​​Recyclable materials​​: End-of-life considerations
- ​​Energy-efficient manufacturing​​: Reduced carbon footprint
- ​​Smart materials​​: Self-diagnostic capabilities
​​7.3 Smart and Connected Systems​​
​​Emerging technologies​​:
- ​​Predictive maintenance​​: IoT sensor integration
- ​​Over-the-air updates​​: Software improvements
- ​​Fleet telematics​​: Real-time monitoring
​​User benefits​​:
- ​​Reduced downtime​​: Predictive maintenance
- ​​Improved safety​​: Early fault detection
- ​​Operational efficiency​​: Data-driven optimization
​​8. Case Studies: Real-World Implementations​​
​​Case Study 1: Long-Haul Truck Brake System Upgrade​​
A major logistics company implemented advanced air brake systems across their fleet, achieving:
- 15% reduction in braking distance
- 20% longer component lifespan
- 30% decrease in maintenance costs
​​Case Study 2: Transit Bus Brake System Modernization​​
A city transportation authority upgraded to electronic-controlled air brakes, resulting in:
- 40% improvement in stop consistency
- 50% reduction in passenger complaints
- 25% lower brake dust emissions
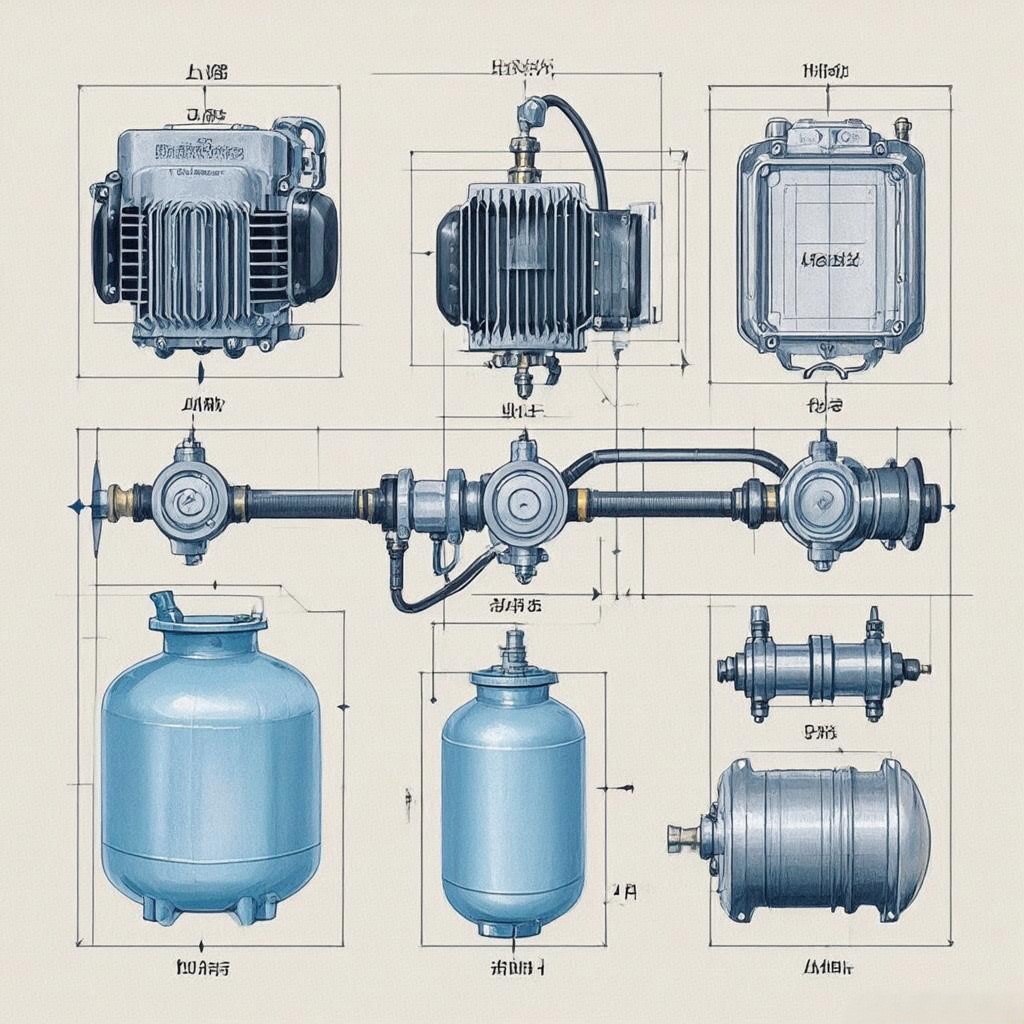

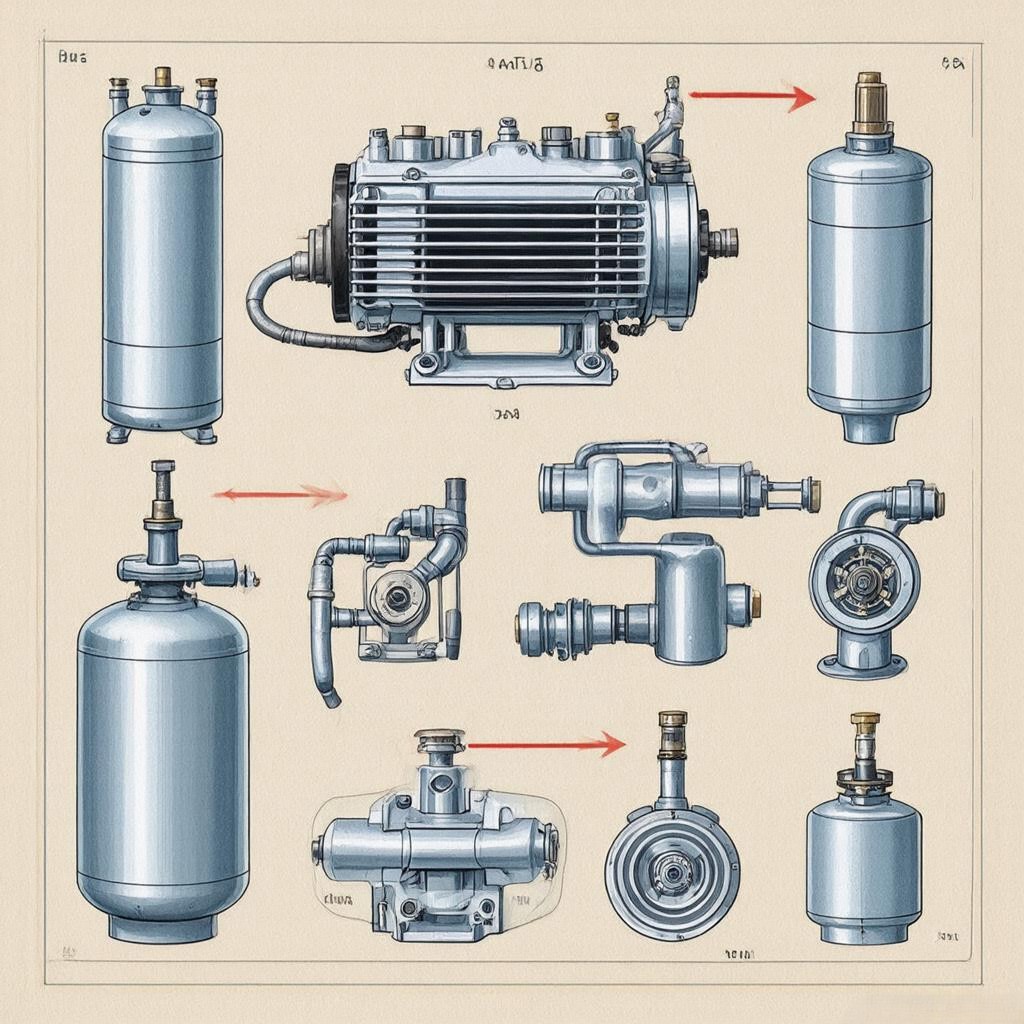
​​Conclusion: The Backbone of Heavy Vehicle Safety​​
Air brake systems represent the critical safety interface between heavy vehicles and the road, combining mechanical reliability with advanced electronic controls to deliver unmatched stopping power. As vehicles become more sophisticated with electrification and autonomous capabilities, these systems must continue evolving to meet new challenges while maintaining their core function of safe deceleration.
​​Key takeaways:​​
- Modern air brake systems integrate compressed air power with electronic controls for optimal performance
- Advanced materials and manufacturing are enabling lighter, more efficient designs
- System integration with electrification and autonomy requires new engineering solutions
- Sustainability and digitalization are shaping the next generation of braking technology
​​Final thought​​: In an era where vehicle safety standards are higher than ever, the air brake system remains the gold standard for heavy-duty applications. The next generation of these systems will need to balance unprecedented safety requirements with the demands of electrification, autonomy, and environmental sustainability, making them one of the most critical areas of automotive innovation today.
​​Call to Action​​
đź”§ Upgrading your vehicle’s braking system?
⚙️ Explore our advanced air brake solutions for improved safety and efficiency
📊 Request performance data comparing traditional vs. next-generation systems
#AirBrakeSystem #CommercialVehicles #HeavyDutyBraking #VehicleSafety #ADAS #Electrification #SmartMobility #FutureOfTransportation #FunctionalSafety #AutomotiveEngineering