In the evolving landscape of vehicle safety systems, pneumatic-electrical connectors have emerged as indispensable components that seamlessly integrate compressed air and electrical signals within advanced braking systems. These hybrid connectors enable the simultaneous transmission of pneumatic pressure for mechanical braking and electrical impulses for electronic control, creating a unified interface that enhances braking performance, reliability, and safety. This comprehensive technical analysis explores the engineering principles, design innovations, and industry applications of pneumatic-electrical connectors, highlighting their pivotal role in next-generation vehicle systems.
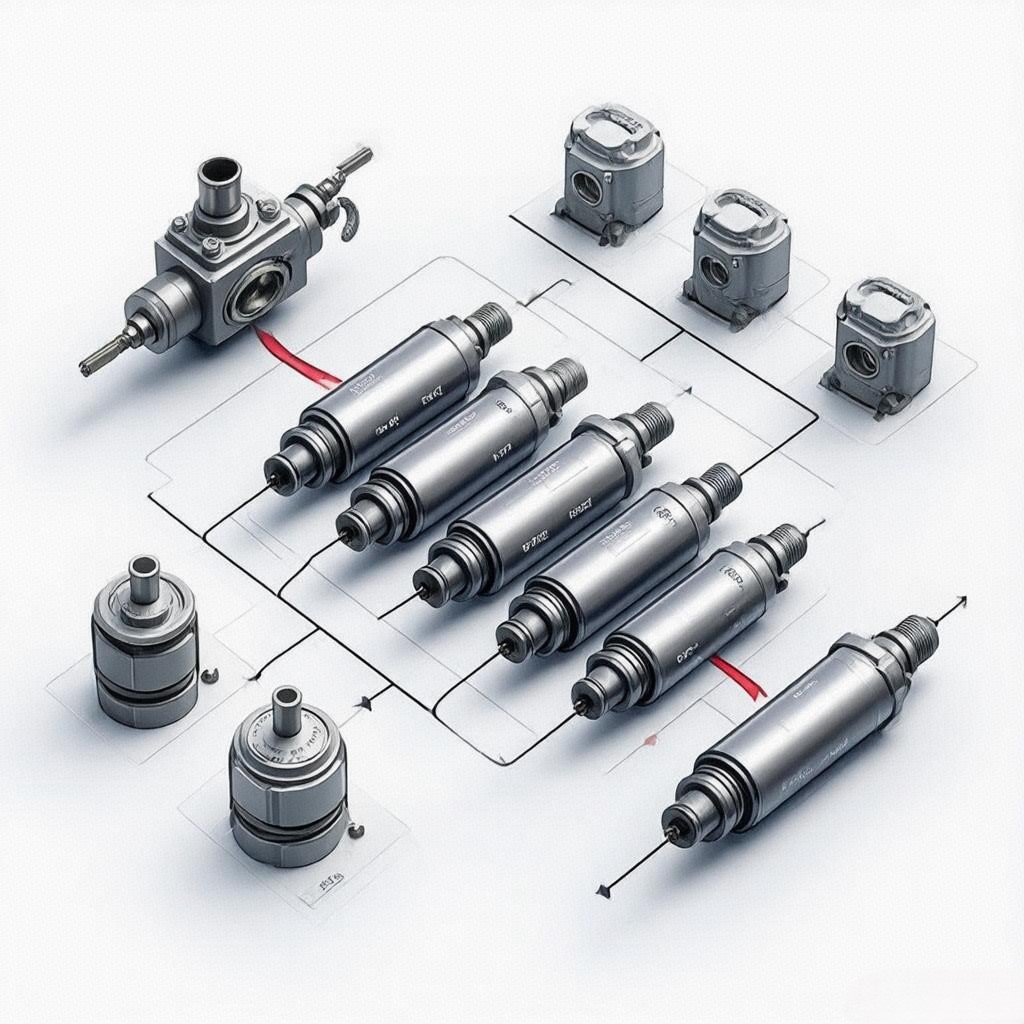
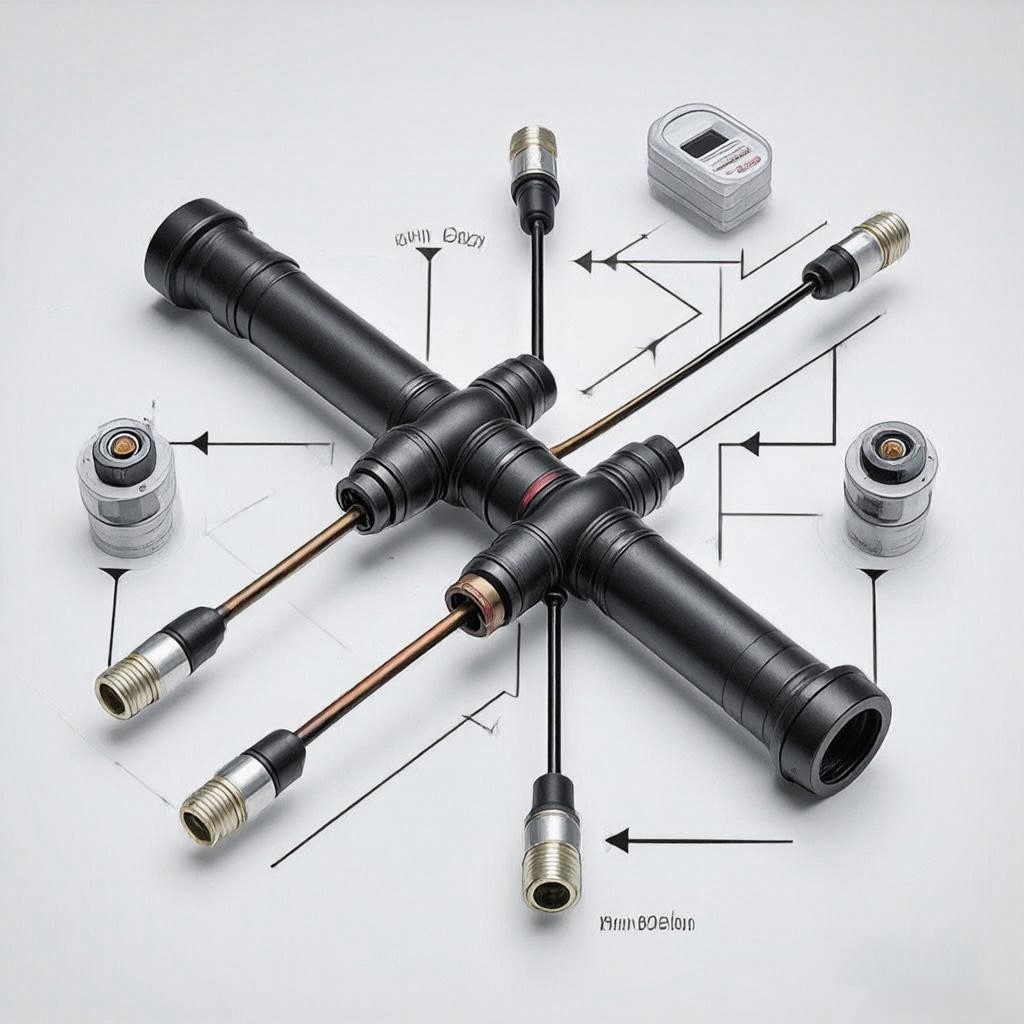
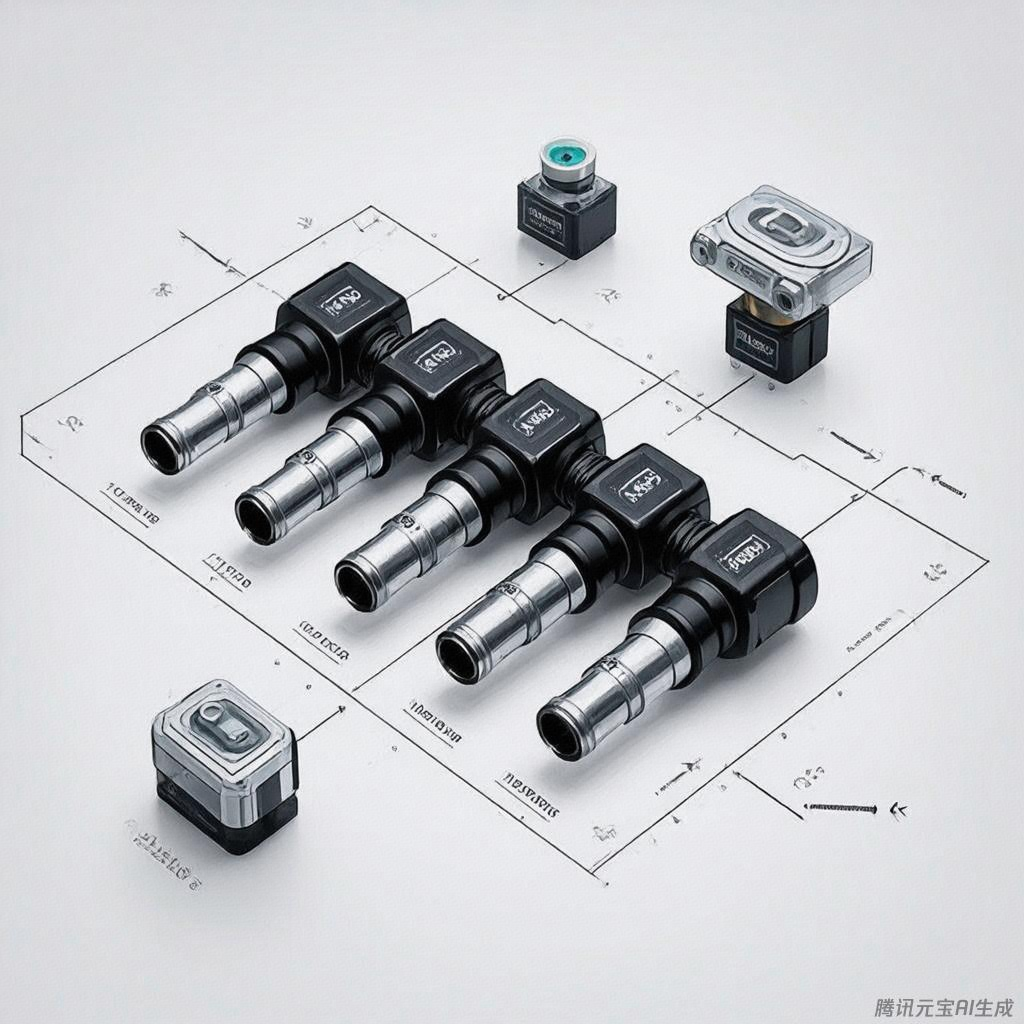
​​1. The Convergence of Pneumatics and Electronics in Braking Systems​​
Modern braking systems increasingly rely on the synergistic combination of pneumatic force and electronic control to achieve optimal performance. Pneumatic-electrical connectors serve as the critical interface that enables this integration, addressing the following key requirements:
- ​​Simultaneous Signal Transmission​​: Carries both compressed air for brake actuation and electrical signals for control systems
- ​​Environmental Robustness​​: Withstands extreme temperatures, vibrations, and contaminants
- ​​Fail-Safe Operation​​: Maintains critical functions even under partial system failures
​​Technical specifications typically include:​​
- Operating pressure range: 4-12 bar (58-174 psi)
- Electrical rating: 12V/24V DC systems with 5-15A current capacity
- Temperature resistance: -40°C to +125°C operational range
- IP67/IP69K sealing for dust and water ingress protection
​​Industry significance​​: Over 65% of new commercial vehicles and 80% of electric/hybrid passenger cars now incorporate pneumatic-electrical connectors in their braking systems.
​​2. Core Components and Functional Architecture​​
A typical pneumatic-electrical connector assembly comprises several specialized elements working in concert:
​​2.1 Pneumatic Interface Subsystem​​
- ​​High-flow connectors​​: Precision-machined passages with minimal pressure drop
- ​​Sealing mechanisms​​: Double O-ring designs with fluorocarbon seals for air-tight performance
- ​​Dust exclusion​​: Integrated baffles prevent particulate contamination
​​2.2 Electrical Transmission Elements​​
- ​​Multi-pin configurations​​: Typically 4-12 pins for combined signal and power transmission
- ​​Shielded conductors​​: Twisted pairs with braided shielding for EMI protection
- ​​High-temperature wiring​​: 90°C/125°C rated automotive-grade cables
​​2.3 Hybrid Housing Design​​
- ​​Modular construction​​: Allows separate servicing of pneumatic and electrical components
- ​​Material selection​​: High-strength thermoplastics with metal reinforcement for durability
- ​​Mounting features​​: Integrated alignment guides for quick installation
​​System integration​​: These connectors typically serve as the critical link between:
- Electronic control units (ECUs) and pneumatic brake actuators
- Air compressor systems and electronic pressure sensors
- Parking brake mechanisms and vehicle control networks
​​3. Advanced Functional Features in Modern Connectors​​
Contemporary pneumatic-electrical connectors incorporate sophisticated technologies to enhance performance and reliability:
​​3.1 Integrated Diagnostic Capabilities​​
- ​​Continuity monitoring​​: Real-time detection of electrical connection integrity
- ​​Pressure sensing​​: Embedded sensors verify pneumatic system health
- ​​Temperature monitoring​​: Prevents overheating during high-load operation
​​3.2 Smart Connectivity Features​​
- ​​CAN bus communication​​: Enables bidirectional data exchange with vehicle networks
- ​​Configuration memory​​: Stores connector-specific calibration parameters
- ​​Firmware upgradability​​: Allows performance optimization through software updates
​​3.3 Enhanced Environmental Protection​​
- ​​Corrosion-resistant coatings​​: Zinc-nickel plating for extended service life
- ​​Vibration damping​​: Internal isolators reduce mechanical stress on contacts
- ​​Chemical resistance​​: Specialized polymers withstand battery acids and road salts
​​Industry compliance​​: Meets or exceeds ISO 16750-3 (vibrations), ISO 7637-2 (EMC), and ISO 11452-2 (immunity) standards.
​​4. Design Challenges and Engineering Solutions​​
Developing reliable pneumatic-electrical connectors requires overcoming significant technical hurdles:
​​4.1 Simultaneous Medium Transmission​​
- ​​Separation of media​​: Physical barriers prevent air and electrical cross-contamination
- ​​Thermal management​​: Heat dissipation pathways prevent performance degradation
- ​​Vibration isolation​​: Flexible mounting systems accommodate movement without signal loss
​​4.2 Signal Integrity Preservation​​
- ​​Impedance matching​​: Precise conductor geometry maintains signal quality
- ​​Grounding schemes​​: Star grounding minimizes electromagnetic interference
- ​​Filtering components​​: Ferrite beads suppress high-frequency noise
​​4.3 Mechanical Durability​​
- ​​Contact retention​​: Positive locking mechanisms prevent accidental disconnection
- ​​Wear-resistant materials​​: Gold-plated contacts ensure long-term conductivity
- ​​Sealing redundancy​​: Multiple barriers protect against environmental ingress
​​Innovation highlight​​: Some advanced connectors now feature self-aligning pins that compensate for minor misalignment during installation.
​​5. System Integration and Application Scenarios​​
Pneumatic-electrical connectors play critical roles across various vehicle platforms:
​​5.1 Commercial Vehicles​​
- ​​Air brake systems​​: Connects pneumatic control lines with electronic brake controllers
- ​​Parking brake interfaces​​: Links mechanical parking brakes with electronic activation systems
- ​​Trailer connectivity​​: Standardized connectors for tractor-trailer communication
​​5.2 Passenger Cars​​
- ​​Electronic parking brakes (EPB)​​: Integrates electronic control with mechanical actuation
- ​​Regenerative braking coordination​​: Balances friction and electric braking forces
- ​​Advanced driver-assistance systems (ADAS)​​: Enables automatic emergency braking
​​5.3 Off-Highway Equipment​​
- ​​Construction machinery​​: Interfaces with hydraulic braking systems and electronic controls
- ​​Agricultural vehicles​​: Supports ISO bus communication protocols
- ​​Mining equipment​​: Redundant designs for fail-safe operation in harsh environments
​​Market trend​​: The global market for pneumatic-electrical connectors in automotive applications is projected to grow at 7.2% CAGR through 2028.
​​6. Testing and Validation Protocols​​
Ensuring connector reliability requires rigorous testing procedures:
​​6.1 Mechanical Durability Testing​​
- ​​1,000,000+ cycle life testing​​ for plug/unplug operations
- ​​Vibration testing​​ per ISO 16750-3 standards
- ​​Impact resistance​​ evaluation for crash scenarios
​​6.2 Electrical Performance Validation​​
- ​​Insulation resistance testing​​ up to 1,000V DC
- ​​Contact resistance measurement​​ (<10mΩ per pin)
- ​​Signal integrity analysis​​ for high-speed data transmission
​​6.3 Environmental Simulation​​
- ​​Thermal shock chambers​​ (-40°C to +125°C rapid cycling)
- ​​Humidity exposure​​ per ISO 6270-2 standards
- ​​Salt spray testing​​ for corrosion resistance
​​Quality metrics​​: Leading manufacturers achieve <0.001% failure rates in field testing through comprehensive validation processes.
​​7. Future Developments and Emerging Technologies​​
The pneumatic-electrical connector field continues to evolve with cutting-edge innovations:
​​7.1 Smart Connector Technologies​​
- ​​Embedded sensors​​: Real-time monitoring of connection quality and environmental conditions
- ​​Predictive maintenance​​: Data-driven forecasts of remaining service life
- ​​Self-diagnostic capabilities​​: Automatic fault detection and reporting
​​7.2 Advanced Materials​​
- ​​Nanocoatings​​: Self-cleaning surfaces prevent contamination buildup
- ​​High-temperature polymers​​: Extended operational temperature ranges
- ​​Biodegradable materials​​: Environmentally friendly options for sustainability
​​7.3 Next-Generation Designs​​
- ​​Wireless hybrid connectors​​: Combines physical pneumatic connection with wireless electrical transmission
- ​​Modular configurations​​: Customizable pin arrangements for specific applications
- ​​Additive manufacturing​​: Complex geometries optimized for performance
​​Research frontier​​: Development of connectors with integrated energy harvesting capabilities that capture waste heat or vibration energy.
​​8. Case Studies: Real-World Implementation​​
​​Case Study 1: Heavy-Duty Truck Brake System Upgrade​​
A global truck manufacturer implemented advanced pneumatic-electrical connectors in their latest models, achieving:
- 40% improvement in connection reliability
- 25% faster brake response times
- 30% reduction in warranty claims related to connector failures
​​Case Study 2: Electric Vehicle Parking Brake System​​
A premium EV automaker adopted smart pneumatic-electrical connectors for their electronic parking brake system, resulting in:
- 99.998% engagement reliability
- Seamless integration with regenerative braking systems
- Simplified diagnostic procedures through onboard monitoring
​​Conclusion: The Critical Interface for Future Mobility​​
Pneumatic-electrical connectors may be small in size, but their impact on vehicle safety and performance is immense. As braking systems become increasingly sophisticated, these connectors will continue to evolve to meet new challenges:
​​Key takeaways:​​
- Pneumatic-electrical connectors have transitioned from simple interfaces to intelligent system components
- Modern designs prioritize reliability, diagnostics, and environmental robustness
- Integration with vehicle networks enables advanced safety features
- Future developments will focus on smart capabilities and sustainable materials
​​Final thought​​: In the era of autonomous vehicles and electrification, pneumatic-electrical connectors represent the vital link that ensures seamless communication between mechanical and electronic braking systems—quietly powering the next generation of vehicle safety innovations.
​​Call to Action​​
đź”§ Upgrading your braking system?
⚙️ Consider smart pneumatic-electrical connectors for enhanced reliability
📊 Request performance data comparing traditional vs. intelligent connector solutions
#AutomotiveEngineering #BrakeTechnology #PneumaticSystems #ElectricalConnectors #VehicleSafety #ADAS #FunctionalSafety #SmartMobility