Modern braking systems have evolved far beyond simple mechanical linkages, transforming into sophisticated electro-mechanical systems where electrical components play a pivotal role. From momentary switches to advanced control modules, these components form the intelligent nervous system that governs braking performance, safety features, and driver assistance functions. This comprehensive technical analysis explores the critical electrical components in braking systems, their functional interrelationships, and how they’re shaping the future of vehicle safety and performance.
​​1. The Evolution of Electrical Components in Braking Systems​​
The integration of electrical components into braking systems has revolutionized vehicle safety and performance. Key milestones include:
- ​​1980s​​: Introduction of electronic anti-lock braking systems (ABS)
- ​​1990s​​: Development of electronic brakeforce distribution (EBD)
- ​​2000s​​: Implementation of electronic stability control (ESC)
- ​​2010s​​: Emergence of regenerative braking in hybrid/electric vehicles
- ​​2020s​​: Integration with autonomous driving systems
​​Technical significance​​: Modern vehicles can have over 50 electrical components dedicated to braking functions, with control algorithms processing up to 1,000 sensor inputs per second.
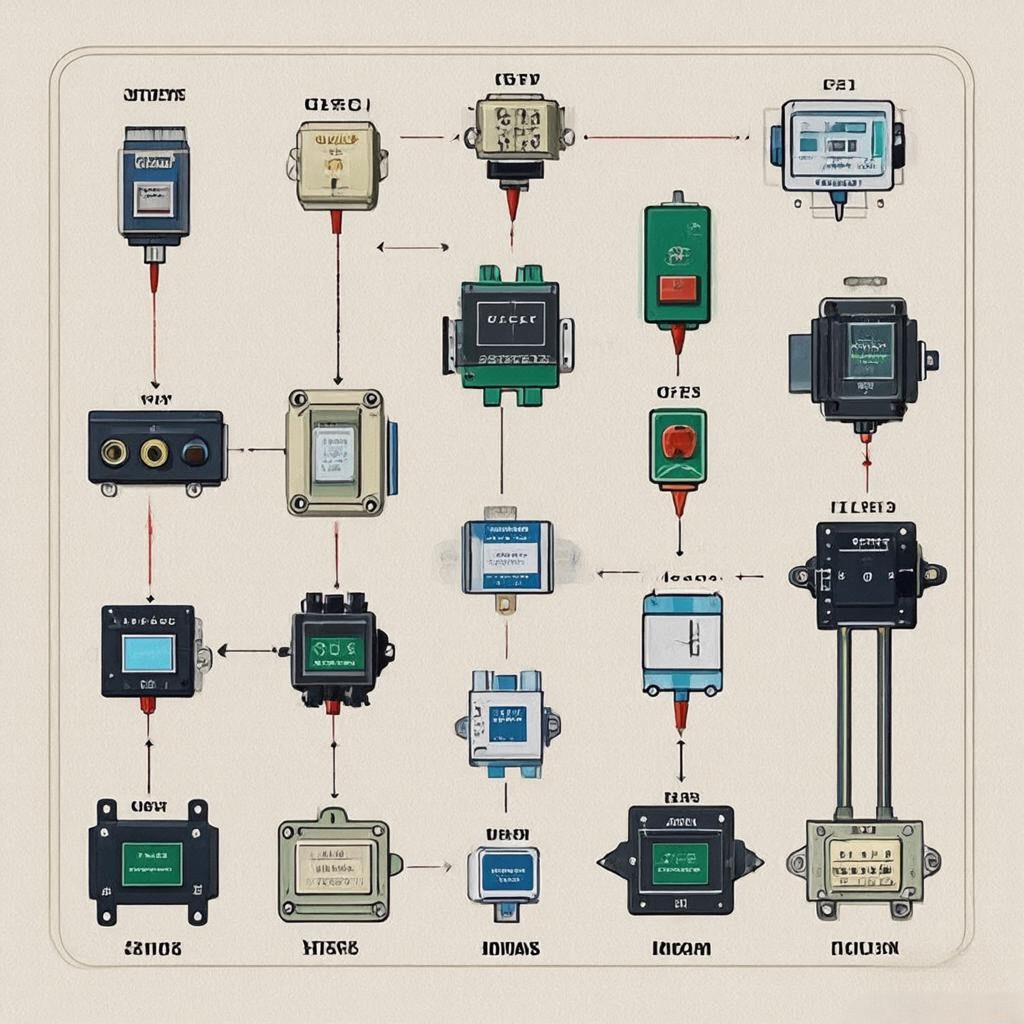
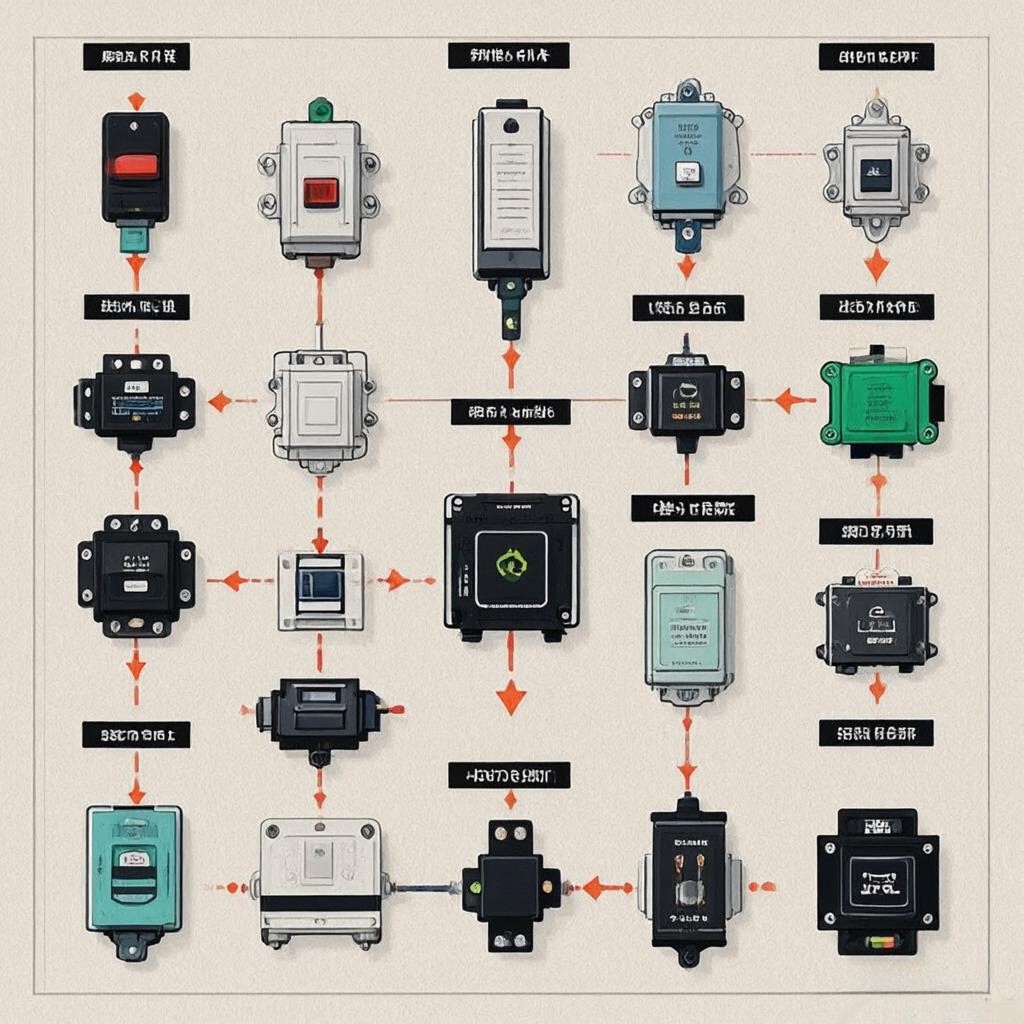
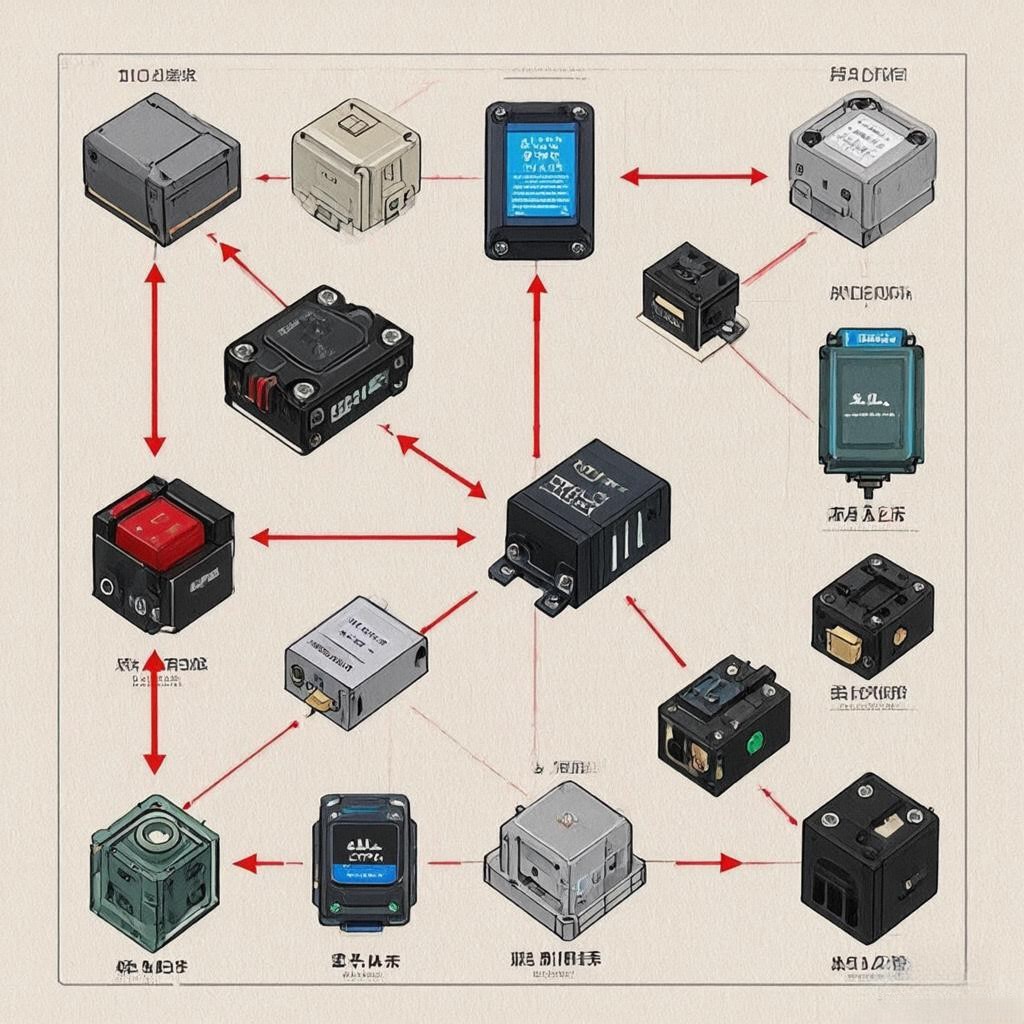
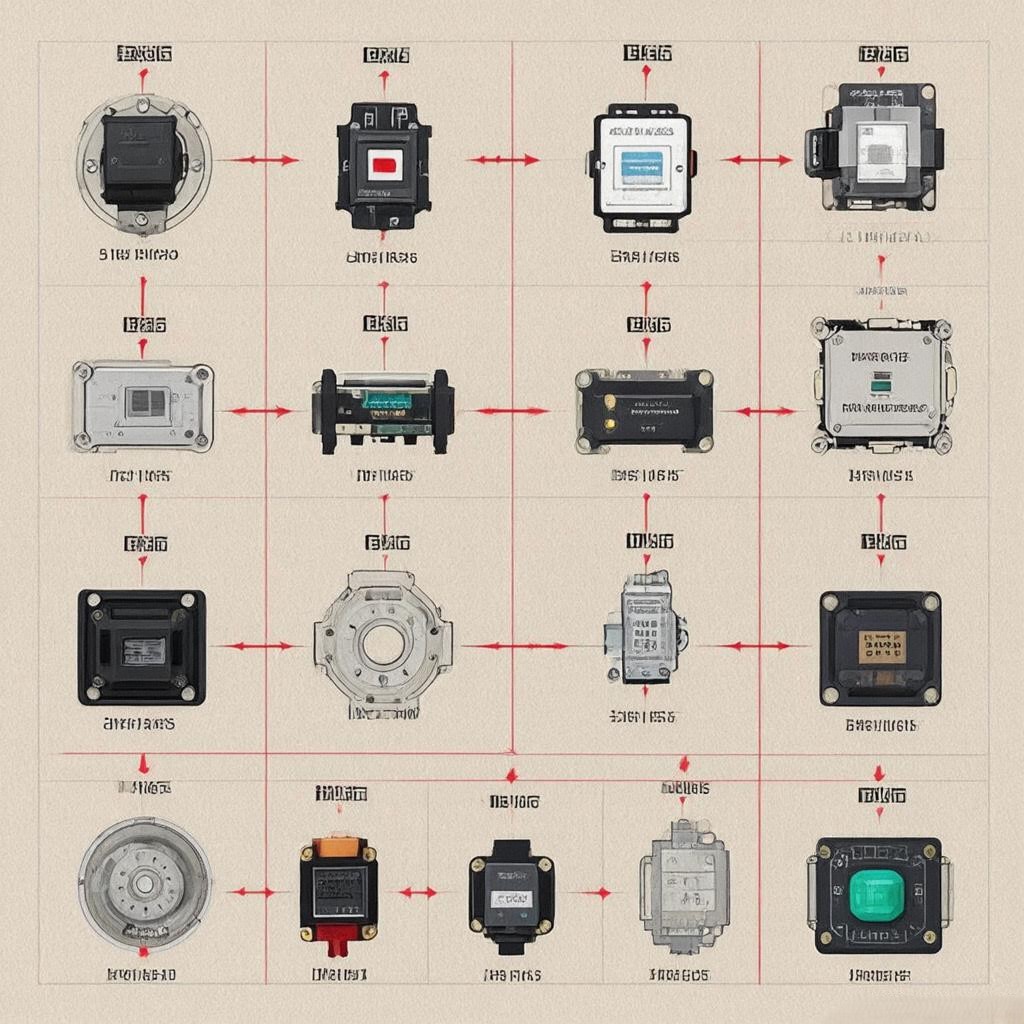
​​2. Core Electrical Components and Their Functions​​
​​2.1 Control Switches​​
​​Brake Light Switch​​
- ​​Function​​: Activates brake lights when pedal is depressed
- ​​Technical specs​​:
- Operating voltage: 12V/24V
- Current rating: 20-30A
- Switching speed: <50ms response time
- ​​Advanced features​​:
- Pressure-sensitive activation for electronic parking brakes
- Integration with cruise control disengagement
​​Parking Brake Switch​​
- ​​Function​​: Signals ECU when parking brake is engaged
- ​​Types​​:
- Mechanical switches for traditional systems
- Hall-effect sensors for electronic systems
- ​​Safety features​​:
- Redundant signaling paths
- Fail-safe default positions
​​2.2 Relay Systems​​
​​Brake Light Relays​​
- ​​Function​​: High-current switching for brake lights
- ​​Technical specifications​​:
- Contact rating: 30A/12V (continuous), 40A/12V (intermittent)
- Coil voltage: 12V±10%
- Response time: <15ms
- ​​Design considerations​​:
- Latching vs. non-latching configurations
- Protection against voltage spikes
​​ABS Relay Modules​​
- ​​Function​​: Power distribution for ABS components
- ​​Advanced features​​:
- Pre-charge circuits for smooth activation
- Redundant contacts for fail-safe operation
​​2.3 Control Modules​​
​​Brake Control Module (BCM)​​
- ​​Functions​​:
- Coordinates ABS, EBD, and ESC functions
- Processes sensor inputs (wheel speed, pedal position, etc.)
- Controls actuator outputs (solenoids, motors)
- ​​Technical specifications​​:
- Processing power: 32-bit microcontrollers @ 100MHz+
- Memory: 256KB+ Flash, 32KB+ RAM
- Communication: CAN, LIN, FlexRay protocols
​​Electronic Parking Brake (EPB) Control Unit​​
- ​​Functions​​:
- Motor control for caliper actuation
- Position sensing and feedback
- Automatic engagement when vehicle is stationary
- ​​Advanced features​​:
- Dynamic torque control
- Hill-start assist integration
​​3. Advanced Functional Features in Modern Electrical Components​​
​​3.1 Signal Processing and Diagnostics​​
​​Sensor Signal Conditioning​​
- ​​Noise filtering​​: Analog filters remove EMI from wheel speed sensors
- ​​Signal amplification​​: Precision op-amps boost weak sensor signals
- ​​Analog-to-digital conversion​​: 12-bit ADCs for high-resolution measurements
​​Built-in Diagnostics​​
- ​​Continuity monitoring​​: Detects open circuits in brake switches
- ​​Performance validation​​: Verifies sensor output ranges
- ​​Fault code generation​​: ISO 14229 (UDS) compliant error reporting
​​3.2 Communication Protocols​​
​​CAN Bus Integration​​
- ​​Data transmission rates​​: 500kbps standard, 1Mbps high-speed
- ​​Message prioritization​​: Critical braking messages get highest priority
- ​​Network management​​: Sleep/wake functions for power efficiency
​​LIN Network Applications​​
- ​​Cost-effective solutions​​: For simple switch inputs
- ​​Deterministic timing​​: Precise synchronization of brake pedal sensors
​​FlexRay Implementation​​
- ​​High-speed requirements​​: For future autonomous braking systems
- ​​Deterministic latency​​: <10μs timing guarantees
​​3.3 Power Management​​
​​Voltage Regulation​​
- ​​Switching regulators​​: High efficiency (85-95%) for ECU power supplies
- ​​LDO regulators​​: Clean voltage for sensitive analog circuits
​​Protection Circuits​​
- ​​Overvoltage clamping​​: TVS diodes protect against load dumps
- ​​Reverse polarity protection​​: MOSFET-based solutions
- ​​Current limiting​​: Prevents damage from short circuits
​​4. System Integration and Architectural Considerations​​
​​4.1 Functional Safety Architecture​​
​​ASIL Compliance​​
- ​​ASIL B requirements​​: For basic braking functions
- ​​ASIL D requirements​​: For autonomous emergency braking
​​Redundancy Design​​
- ​​Dual-channel architectures​​: For critical safety functions
- ​​Cross-checking mechanisms​​: Verify sensor inputs independently
​​4.2 Electromagnetic Compatibility (EMC)​​
​​Shielding Strategies​​
- ​​Conductive coatings​​: For plastic housings
- ​​Filtered connectors​​: Prevent EMI ingress
​​Filtering Components​​
- ​​Ferrite beads​​: Suppress high-frequency noise
- ​​RC filters​​: Clean power supply lines
​​4.3 Thermal Management​​
​​Heat Dissipation​​
- ​​Thermal vias​​: In PCB designs for heat spreading
- ​​Heat sinks​​: For high-power components
​​Temperature Monitoring​​
- ​​Thermistors​​: Embedded temperature sensing
- ​​Shutdown protection​​: Prevents overheating damage
​​5. Design Challenges and Engineering Solutions​​
​​5.1 Miniaturization vs. Power Handling​​
​​Solution Approaches​​:
- ​​High-density PCB layouts​​: 4-6 layer designs with blind vias
- ​​Advanced packaging​​: Ball grid arrays (BGAs) for ICs
- ​​Hybrid connectors​​: Combine power and signal contacts
​​5.2 Software Complexity​​
​​Development Methodologies​​:
- ​​Model-based design​​: Simulink/Stateflow for control algorithms
- ​​AUTOSAR compliance​​: Standardized software architecture
- ​​Over-the-air updates​​: For firmware improvements
​​5.3 Cost vs. Performance Tradeoffs​​
​​Optimization Strategies​​:
- ​​Platform-based design​​: Common components across vehicle lines
- ​​Selective redundancy​​: Critical functions only
- ​​Commodity vs. custom ICs​​: Balance cost and performance
​​6. Testing and Validation Protocols​​
​​6.1 Electrical Performance Testing​​
​​Component Level​​:
- ​​Contact resistance​​: <10mΩ for switches/relays
- ​​Insulation resistance​​: >100MΩ between circuits
​​System Level​​:
- ​​Signal integrity​​: Eye diagram analysis for high-speed signals
- ​​Power quality​​: Harmonic distortion measurements
​​6.2 Environmental Testing​​
​​Temperature Cycling​​: -40°C to +125°C, 1,000 cycles
​​Vibration Testing​​: 5-2000Hz, 15g RMS acceleration
​​Moisture Resistance​​: 10 days in 95% RH at 40°C
​​6.3 Functional Safety Validation​​
​​Fault Injection Testing​​:
- ​​Simulated failures​​: Open circuits, short circuits, stuck signals
- ​​Graceful degradation​​: System response to partial failures
​​Statistical Testing​​:
- ​​Million-mile equivalence​​: Accelerated testing methodologies
- ​​Failure mode analysis​​: FMEA with risk prioritization
​​7. Market Trends and Future Developments​​
​​7.1 Electrification and Autonomous Driving​​
​​Key Trends​​:
- ​​48V architectures​​: For higher power braking systems
- ​​Redundant power supplies​​: For fail-operational autonomous systems
- ​​AI-based control algorithms​​: Machine learning for brake modulation
​​7.2 Sustainable Design Initiatives​​
​​Innovations​​:
- ​​Energy harvesting​​: Regenerative braking for accessory power
- ​​Biodegradable materials​​: Eco-friendly component housings
- ​​Modular designs​​: Easy disassembly for recycling
​​7.3 Advanced Manufacturing Techniques​​
​​Production Technologies​​:
- ​​Automated optical inspection​​: For PCB assembly quality
- ​​3D-printed prototypes​​: Rapid development cycles
- ​​Digital twin simulations​​: Virtual validation before physical testing
​​8. Case Studies: Real-World Implementations​​
​​Case Study 1: Premium EV Braking System​​
​​Implementation​​:
- ​​48V electrical architecture​​
- ​​Redundant control modules​​
- ​​AI-based brake blending algorithms​​
​​Results​​:
- 20% improvement in brake response time
- 99.99% system availability
- 30% reduction in component count
​​Case Study 2: Commercial Vehicle ABS Upgrade​​
​​Implementation​​:
- ​​High-current relays with pre-charge circuits​​
- ​​Enhanced sensor signal processing​​
- ​​Integrated diagnostic capabilities​​
​​Results​​:
- 40% reduction in false activation events
- 50,000+ hour MTBF (Mean Time Between Failures)
- Simplified technician diagnostics
​​Conclusion: The Intelligent Heart of Modern Braking Systems​​
Electrical components have transformed braking systems from purely mechanical systems into sophisticated electro-mechanical networks. As vehicles continue to evolve toward higher levels of automation and electrification, these components will become even more critical:
​​Key takeaways:​​
- Modern braking systems rely on a complex ecosystem of electrical components
- Advanced signal processing and diagnostics are essential for safety
- Electromagnetic compatibility and thermal management are critical design considerations
- Future developments will focus on higher integration and intelligence
​​Final thought​​: In the era of autonomous vehicles, electrical components in braking systems are not just about stopping distance—they’re about enabling vehicles to make split-second decisions that protect lives. The next generation of braking systems will depend on these components to bridge the gap between mechanical action and digital intelligence.
​​Call to Action​​
đź”§ Upgrading your vehicle’s braking system?
⚙️ Consider advanced electrical components for improved safety and performance
📊 Request a technical comparison of traditional vs. next-generation solutions
#AutomotiveEngineering #BrakeTechnology #ElectricalSystems #VehicleSafety #ADAS #FunctionalSafety #SmartMobility #FutureOfTransportation