In the world of heavy-duty transportation, the ability to safely and efficiently decelerate massive vehicles represents a critical engineering challenge. Retarders (often designated as REV – Retarder, Engine Valve) have emerged as indispensable components in modern heavy vehicles, providing auxiliary braking power that reduces reliance on traditional friction brakes while enhancing safety, extending brake life, and improving overall vehicle control. This comprehensive technical analysis explores the complete ecosystem of retarder systems, their functional principles, advanced technological implementations, and the transformative impact these systems have on heavy vehicle operations worldwide.
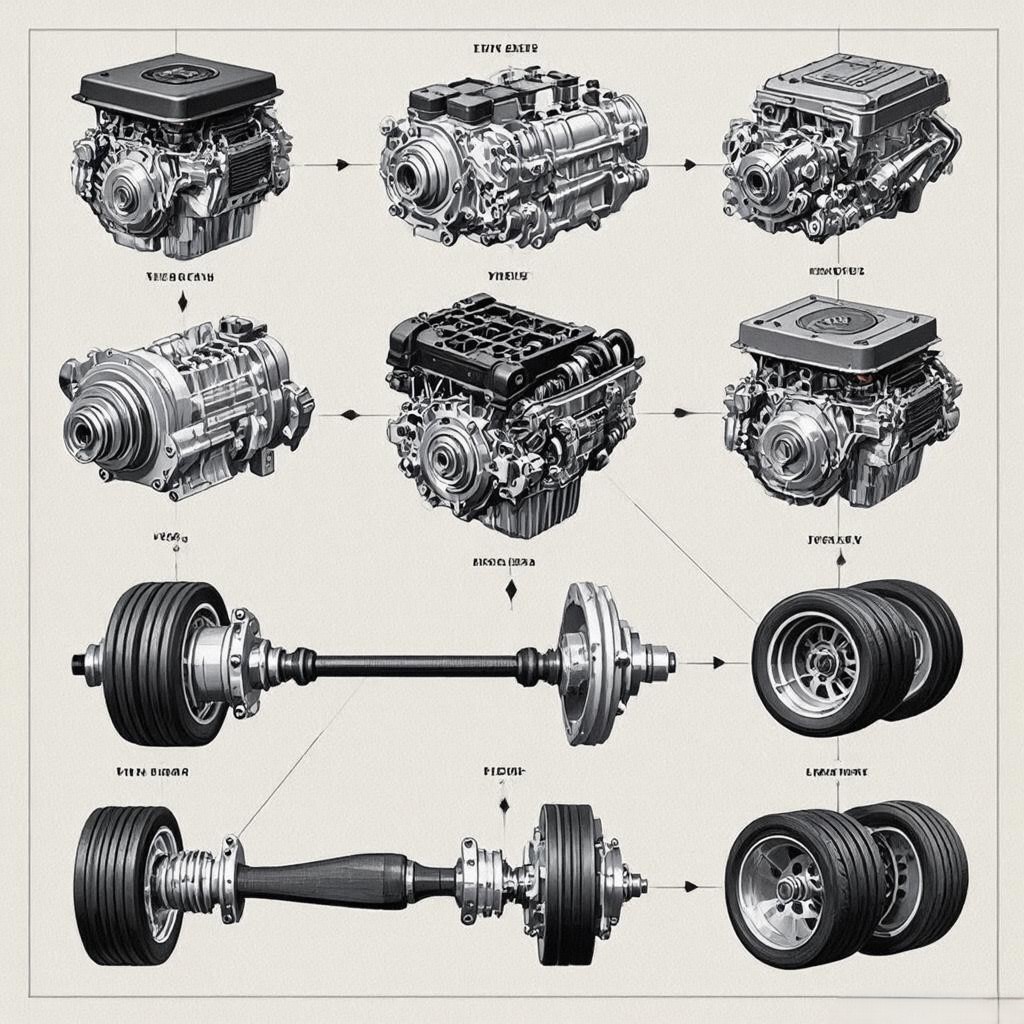
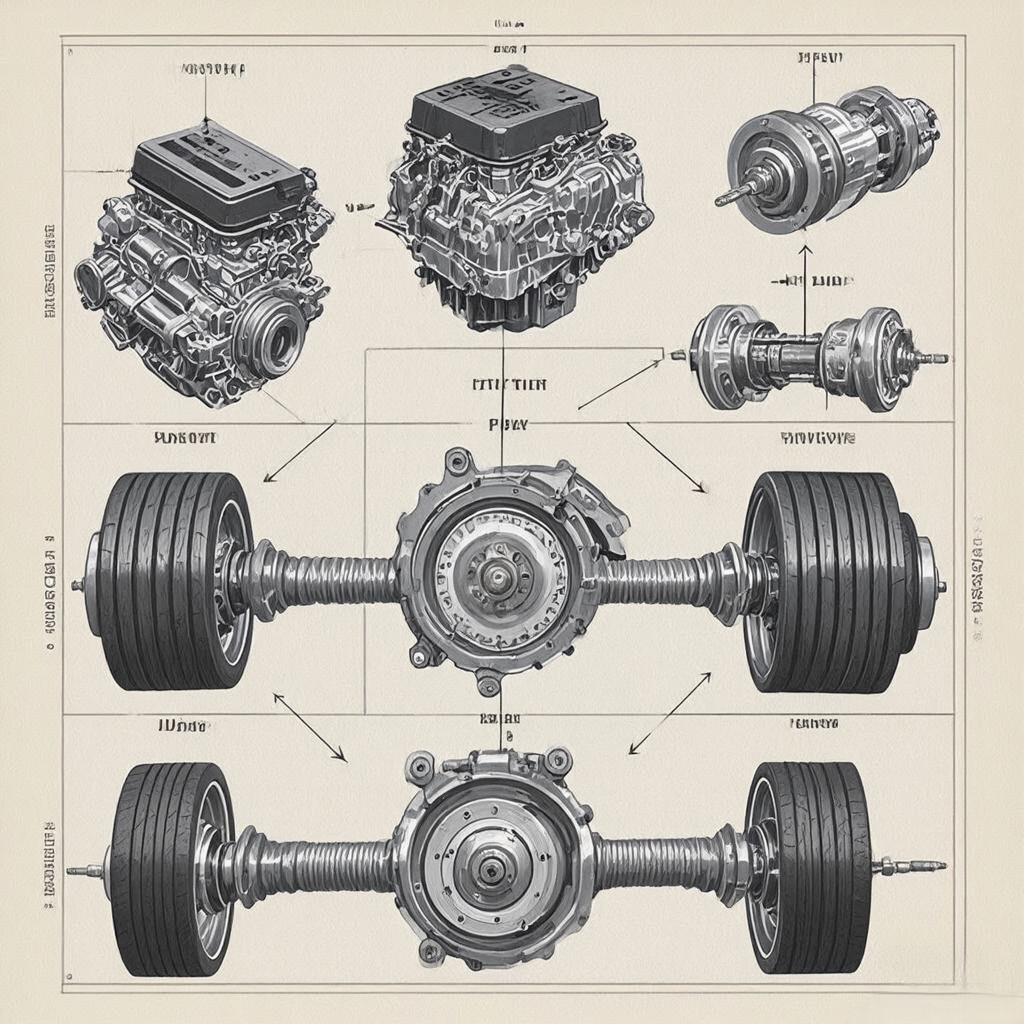
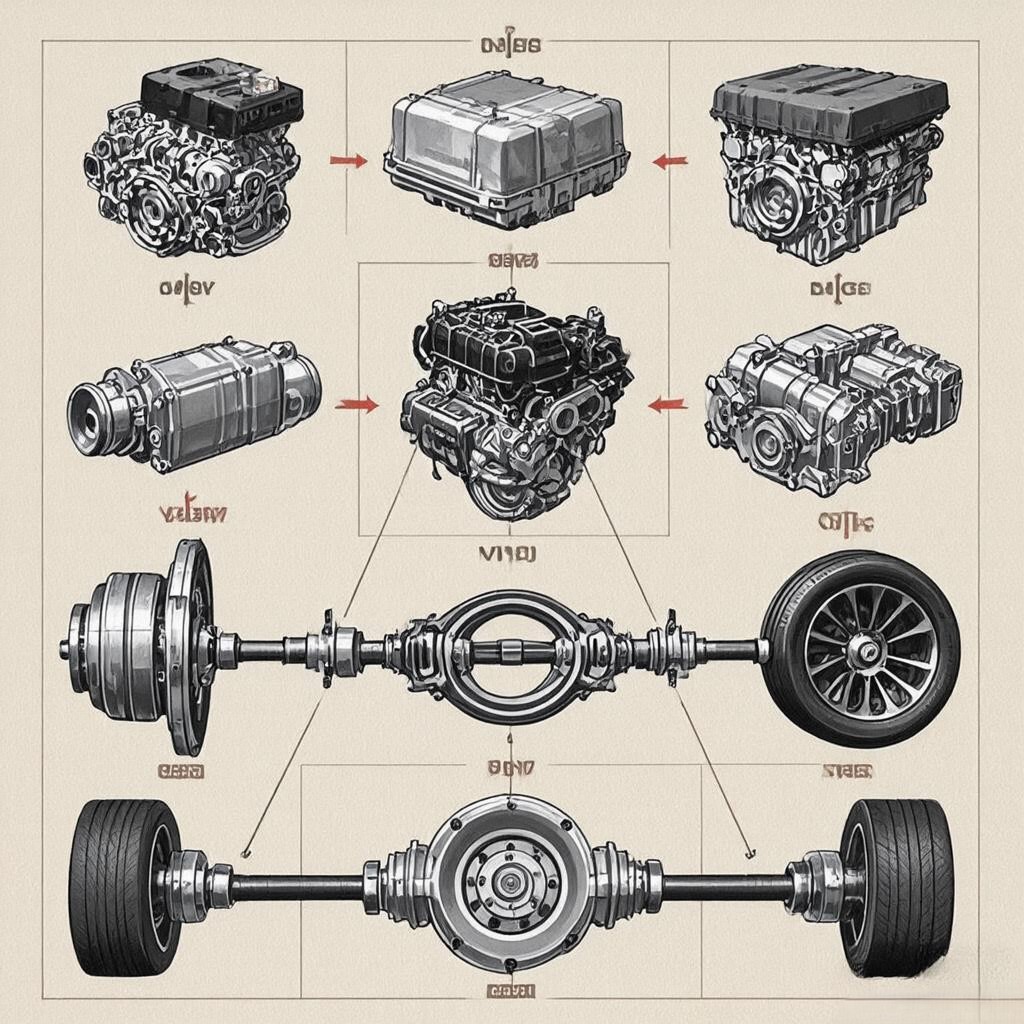
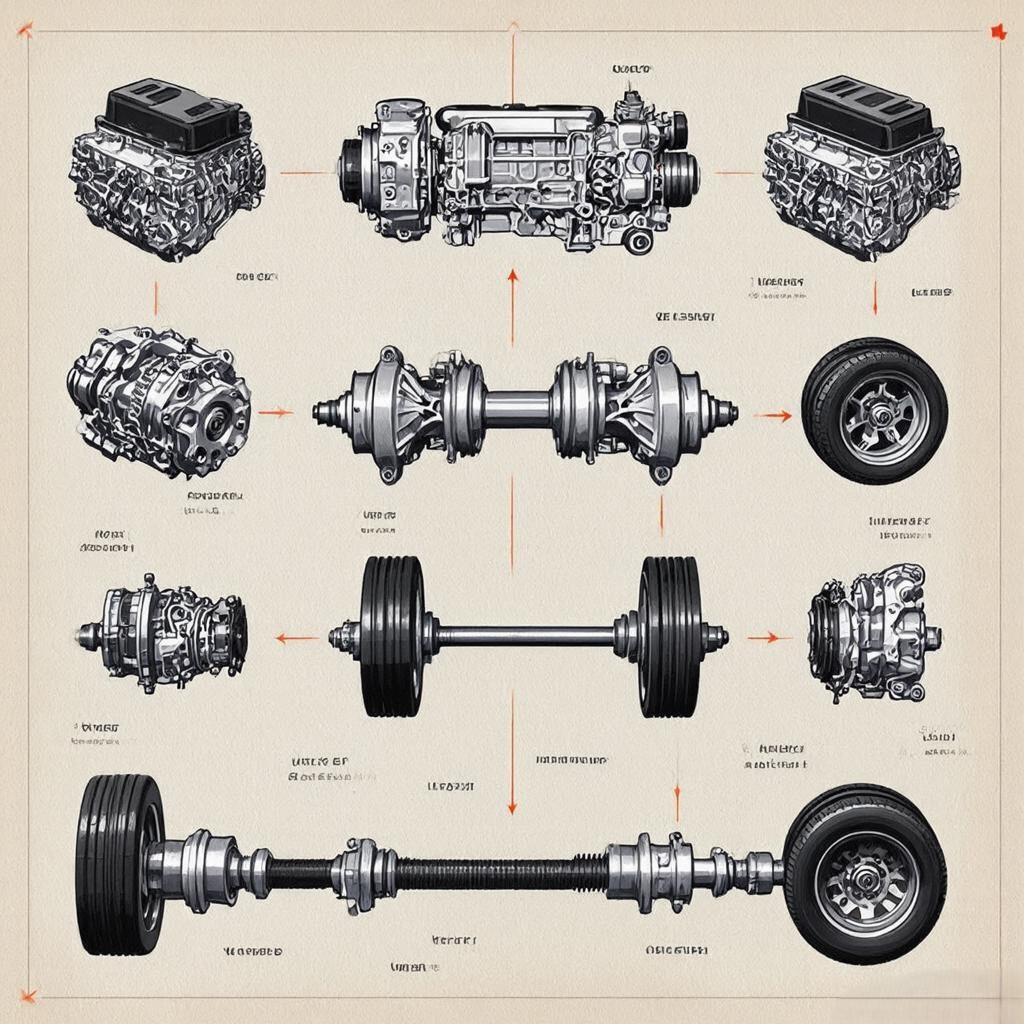
​​1. Fundamental Principles of Retarder Systems​​
Retarders serve as supplementary braking systems that harness the engine’s inherent resistance to rotation to slow the vehicle, operating through several fundamental mechanisms:
- ​​Engine compression braking​​: Utilizing engine cylinders to create resistance against piston movement
- ​​Exhaust throttling​​: Restricting exhaust flow to increase backpressure
- ​​Hydraulic retardation​​: Converting kinetic energy into heat through fluid friction
- ​​Electric regeneration​​: Capturing energy for potential reuse (in hybrid systems)
​​Technical specifications​​:
- Typical braking force: 20-40% of vehicle gross weight
- Operating temperature range: -40°C to +85°C
- Response time: <0.5 seconds for full activation
- Maximum power dissipation: Up to 400 kW in heavy-duty applications
​​Industry significance​​: Vehicles equipped with modern retarders experience 30-50% longer brake component lifespan and 25% reduction in brake-related maintenance costs, while significantly improving safety on long descents.
​​2. Types of Retarder Systems and Operational Characteristics​​
Contemporary heavy vehicles employ various retarder configurations optimized for specific operational requirements:
​​2.1 Exhaust Brakes​​
​​Design and functionality​​:
- ​​Valve mechanism​​: Butterfly or gate valve in the exhaust stream
- ​​Backpressure generation​​: Restricts exhaust flow during activation
- ​​Typical braking force​​: 10-20% of engine torque output
​​Performance metrics​​:
- Response time: 0.3-0.8 seconds
- Maximum backpressure: 3-5 bar (43-72 psi)
- Fuel efficiency impact: Minimal (passive operation)
​​Applications​​: Light to medium-duty trucks, buses
​​2.2 Engine Compression Brakes (Jake Brakes)​​
​​Mechanical operation​​:
- ​​Valve timing modification​​: Opens exhaust valves during compression stroke
- ​​Energy dissipation​​: Converts piston compression work into heat
- ​​Braking stages​​: Typically 2-8 stages for graduated control
​​Technical specifications​​:
- Braking torque: 25-40% of engine rating
- Noise level: 85-95 dB(A) (unmuffled)
- Durability: 1,000,000+ activation cycles
​​Advanced features​​:
- ​​Variable stage control​​: Electronic modulation of braking intensity
- ​​Muffler integration​​: Noise reduction systems
- ​​Engine protection algorithms​​: Preventing overheating
​​2.3 Hydraulic Retarders​​
​​Hydraulic circuit design​​:
- ​​Torque converter principle​​: Fluid coupling with stator braking
- ​​Heat dissipation​​: Through vehicle cooling system
- ​​Control methods​​: Proportional valve or on/off operation
​​Performance characteristics​​:
- Braking power: 50-400 kW continuous rating
- Response time: <0.2 seconds
- Cooling requirements: 10-30 kW heat rejection
​​Integration aspects​​:
- ​​Transmission-mounted​​: Direct integration with gearbox
- ​​Independent systems​​: Standalone units for specific applications
​​2.4 Electromagnetic Retarders​​
​​Electrodynamic braking​​:
- ​​Rotor-stator interaction​​: Copper windings and magnetic fields
- ​​Energy conversion​​: Kinetic to electrical energy
- ​​Power management​​: Battery charging or resistive dissipation
​​Technical highlights​​:
- Regenerative capability: Up to 30% energy recovery
- Braking torque: 100-300 Nm per unit
- Noise level: <75 dB(A)
​​Advanced developments​​:
- ​​Hybrid system integration​​: Combined with electric drivetrains
- ​​Smart control algorithms​​: Predictive braking based on route data
​​3. Advanced Control Systems and Electronic Integration​​
​​3.1 Electronic Control Units (ECUs)​​
​​Hardware specifications​​:
- ​​32-bit microcontrollers​​: 150MHz+ processing power
- ​​Sensor interfaces​​: 16+ analog/digital inputs
- ​​Communication protocols​​: CAN FD (5Mbps), LIN (20kbps)
​​Software features​​:
- ​​Adaptive braking algorithms​​: Load-sensing and grade detection
- ​​Fail-safe modes​​: Multiple redundancy levels
- ​​Diagnostic capabilities​​: ISO 14229 (UDS) compliance
​​Control strategies​​:
- ​​Proportional-integral-derivative (PID) control​​: Precise torque modulation
- ​​Predictive algorithms​​: Using GPS and terrain mapping
- ​​Driver preference learning​​: Customizable response profiles
​​3.2 Sensor Suite and Feedback Systems​​
​​Critical sensors and functions​​:
- ​​Vehicle speed sensors​​: Wheel-based (±1% accuracy)
- ​​Throttle position sensors​​: 0.5% resolution
- ​​Engine load sensors​​: MAP/MAF-based measurement
- ​​Temperature sensors​​: Exhaust, coolant, oil (±2°C accuracy)
​​Data fusion techniques​​:
- ​​Kalman filtering​​: Noise reduction in sensor readings
- ​​Sensor validation​​: Cross-checking multiple inputs
- ​​Failure detection​​: Real-time anomaly monitoring
​​3.3 Human-Machine Interface (HMI)​​
​​Driver controls​​:
- ​​Dashboard switches​​: Multifunctional stalks or buttons
- ​​Pedal modulation​​: Optional foot-controlled operation
- ​​Display feedback​​: LCD/LED indicators with 5+ status levels
​​Customization options​​:
- ​​Braking intensity profiles​​: 3-5 preset modes
- ​​Automatic activation thresholds​​: Configurable slope angles
- ​​Integration with cruise control​​: Coordinated speed management
​​4. System Integration and Vehicle Applications​​
​​4.1 Heavy-Duty Trucks and Buses​​
​​Typical configurations​​:
- ​​Compression brakes​​: 6-8 stage Jake brakes for maximum retardation
- ​​Hydraulic retarders​​: Transmission-mounted for seamless integration
- ​​Combined systems​​: Multiple technologies for graduated response
​​Performance metrics​​:
- Deceleration rate: 0.3-0.5g on 6% grades
- Brake temperature reduction: 30-50% compared to friction brakes alone
- Maintenance interval extension: 2-3x longer service life
​​Specialized applications​​:
- ​​Mountainous routes​​: Continuous braking for extended descents
- ​​Urban transit buses​​: Frequent stop-and-go operation
- ​​Emergency vehicles​​: Controlled approach speeds
​​4.2 Off-Highway and Construction Equipment​​
​​Heavy machinery implementations​​:
- ​​Hydraulic retarders​​: Integrated with hydrostatic transmissions
- ​​Electromagnetic systems​​: For precise load control
- ​​Engine compression brakes​​: Modified for non-road engines
​​Performance requirements​​:
- ​​Dust and water resistance​​: IP67/IP69K ratings
- ​​High ambient temperatures​​: Up to 120°C operation
- ​​Vibration resistance​​: 15g RMS acceleration
​​Unique features​​:
- ​​Load-sensing valves​​: Automatic adjustment based on implement weight
- ​​Creep control​​: Low-speed braking assistance
- ​​Regenerative systems​​: Battery charging during deceleration
​​4.3 Passenger Coaches and Tour Buses​​
​​Touring vehicle applications​​:
- ​​Quiet operation​​: Muffled exhaust brakes and electromagnetic systems
- ​​Smooth modulation​​: Precise control for passenger comfort
- ​​Automatic grade braking​​: Pre-programmed descent profiles
​​Safety enhancements​​:
- ​​ABS coordination​​: Preventing wheel lockup during retardation
- ​​ESP integration​​: Stability control during braking
- ​​Hill start assist​​: Preventing rollback on inclines
​​5. Design Challenges and Engineering Solutions​​
​​5.1 Thermal Management​​
​​Heat dissipation strategies​​:
- ​​Cooling system integration​​: Dedicated oil/water circuits
- ​​Heat exchanger designs​​: High-efficiency finned cores
- ​​Thermal sensors​​: Real-time temperature monitoring
​​Material innovations​​:
- ​​High-temperature alloys​​: For exhaust components
- ​​Ceramic coatings​​: Reduced thermal conductivity
- ​​Phase-change materials​​: Thermal energy storage
​​5.2 Noise and Vibration Control​​
​​Acoustic mitigation techniques​​:
- ​​Exhaust mufflers​​: Reactive and absorptive elements
- ​​Mounting systems​​: Vibration isolation mounts
- ​​Sound-dampening materials​​: Composite panels
​​Vibration reduction strategies​​:
- ​​Balanced rotor designs​​: For electromagnetic systems
- ​​Hydraulic damping​​: Fluid inertia accumulators
- ​​Structural reinforcement​​: Stiffening of mounting points
​​5.3 Reliability and Durability​​
​​Component life extension​​:
- ​​Surface treatments​​: Chrome plating, nitriding
- ​​Advanced lubrication​​: Synthetic oils with additives
- ​​Predictive maintenance​​: Condition monitoring systems
​​Testing protocols​​:
- ​​Endurance testing​​: 1,000,000+ activation cycles
- ​​Environmental simulation​​: -40°C to +120°C, 100% humidity
- ​​Salt spray exposure​​: 2,000+ hours for corrosion resistance
​​6. Testing and Validation Methodologies​​
​​6.1 Component-Level Testing​​
​​Retarder unit testing​​:
- ​​Torque measurement​​: ±1% accuracy dynamometers
- ​​Temperature cycling​​: -40°C to +85°C, 1,000 cycles
- ​​Vibration testing​​: 15g RMS, 10-2,000Hz
​​Control system validation​​:
- ​​HIL testing​​: 100% coverage of software states
- ​​Fault injection​​: Simulating sensor failures
- ​​EMC testing​​: Immunity to 100V/m fields
​​6.2 System-Level Validation​​
​​Vehicle testing protocols​​:
- ​​Grade braking tests​​: 6-12% slopes at full payload
- ​​Endurance runs​​: 10,000km with continuous monitoring
- ​​Emergency stop simulations​​: 0.3-0.5g deceleration
​​Performance metrics​​:
- Braking force consistency: ±5% variation
- Temperature stability: <10°C rise during operation
- Response time: <0.5 seconds for 95% of activations
​​6.3 Virtual Validation​​
​​Simulation tools​​:
- ​​Model-in-the-loop (MIL)​​: MATLAB/Simulink models
- ​​Software-in-the-loop (SIL)​​: Real-time processor-in-the-loop
- ​​Hardware-in-the-loop (HIL)​​: dSPACE/ETAS systems
​​Test scenarios​​:
- ​​10,000+ virtual test cases​​ covering all operating conditions
- ​​Edge case testing​​: Extreme loads and temperatures
- ​​Long-term durability simulation​​: 10-year equivalent cycles
​​7. Market Trends and Future Developments​​
​​7.1 Electrification and Hybridization​​
​​Key innovations​​:
- ​​Regenerative retarders​​: Energy recovery systems
- ​​48V mild hybrid integration​​: Reduced electrical loads
- ​​Predictive control algorithms​​: Using route data and traffic patterns
​​Technical challenges​​:
- ​​Energy storage capacity​​: Battery sizing for regenerative systems
- ​​Thermal management​​: Heat dissipation in electric components
- ​​System integration​​: Coordinating with existing drivetrain
​​7.2 Advanced Materials and Manufacturing​​
​​Innovative approaches​​:
- ​​3D-printed components​​: Complex geometries for improved cooling
- ​​Carbon fiber reinforced polymers​​: Lightweight housings
- ​​Additive manufacturing​​: Rapid prototyping of new designs
​​Sustainability focus​​:
- ​​Recyclable materials​​: End-of-life considerations
- ​​Energy-efficient manufacturing​​: Reduced carbon footprint
- ​​Smart materials​​: Self-healing coatings and structures
​​7.3 Smart and Connected Systems​​
​​Emerging technologies​​:
- ​​Over-the-air (OTA) updates​​: Software improvements without service visits
- ​​Digital twin technology​​: Predictive maintenance and performance monitoring
- ​​AI-based learning algorithms​​: Personalized braking profiles
​​User benefits​​:
- ​​Remote diagnostics​​: Fleet management integration
- ​​Customizable settings​​: Driver preference storage
- ​​Proactive alerts​​: Maintenance notifications based on usage
​​8. Case Studies: Real-World Implementations​​
​​Case Study 1: Mountain Route Trucking Fleet​​
A European logistics company implemented advanced retarder systems in their mountain route fleet, achieving:
- 40% reduction in brake component replacements
- 25% improvement in fuel efficiency on descents
- Enhanced safety with fewer brake-related incidents
​​Case Study 2: Urban Transit Bus Modernization​​
A city transportation authority upgraded their bus fleet with quiet electromagnetic retarders, resulting in:
- 50% noise reduction in residential areas
- 30% longer brake life
- Improved passenger comfort during frequent stops
​​Conclusion: The Intelligent Braking Solution for Heavy Vehicles​​
Retarder systems have evolved from simple engine braking mechanisms to sophisticated electronic control systems that manage complex deceleration tasks while optimizing vehicle performance and safety. As transportation requirements continue to demand heavier payloads and more efficient operations, these systems will play an increasingly critical role in shaping the future of heavy vehicle engineering.
​​Key takeaways:​​
- Modern retarders combine multiple braking technologies with advanced electronic controls
- System integration with vehicle dynamics requires sophisticated sensor fusion and control algorithms
- Electrification and connectivity are driving the next generation of retarder innovations
- Sustainability and digitalization are transforming traditional braking system architectures
​​Final thought​​: The retarder represents the perfect synergy between mechanical engineering and digital intelligence, constantly adapting to deliver optimal deceleration performance while protecting vehicle components and ensuring passenger safety. As vehicles become more connected and autonomous, these systems will continue to evolve, incorporating artificial intelligence and predictive analytics to redefine the standards of heavy vehicle braking performance.
​​Call to Action​​
đź”§ Upgrading your fleet’s braking system?
⚙️ Explore our advanced retarder solutions for improved safety and efficiency
📊 Request technical specifications and performance data for your specific application
#HeavyVehicleTechnology #RetarderSystems #EngineBraking #CommercialTransportation #AdvancedDriverAssistanceSystems #Electrification #SmartMobility #FutureOfTransportation #VehicleDynamics #SustainableEngineering