The air suspension control system represents the technological pinnacle of vehicle dynamics management, combining sophisticated electronics, real-time sensor data, and adaptive algorithms to deliver unparalleled ride comfort, precise handling, and dynamic load management. This comprehensive technical analysis explores the architecture, components, and cutting-edge innovations in air suspension control systems that are redefining modern mobility.
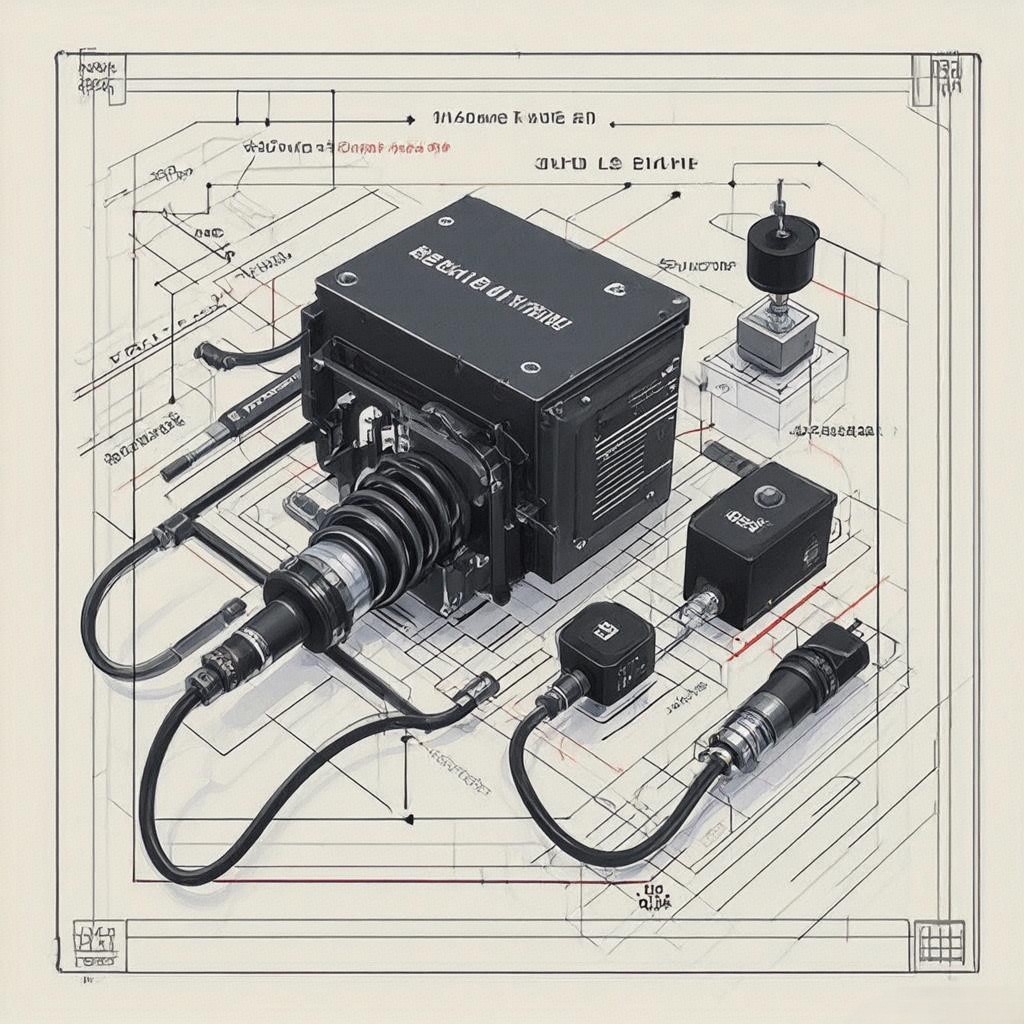
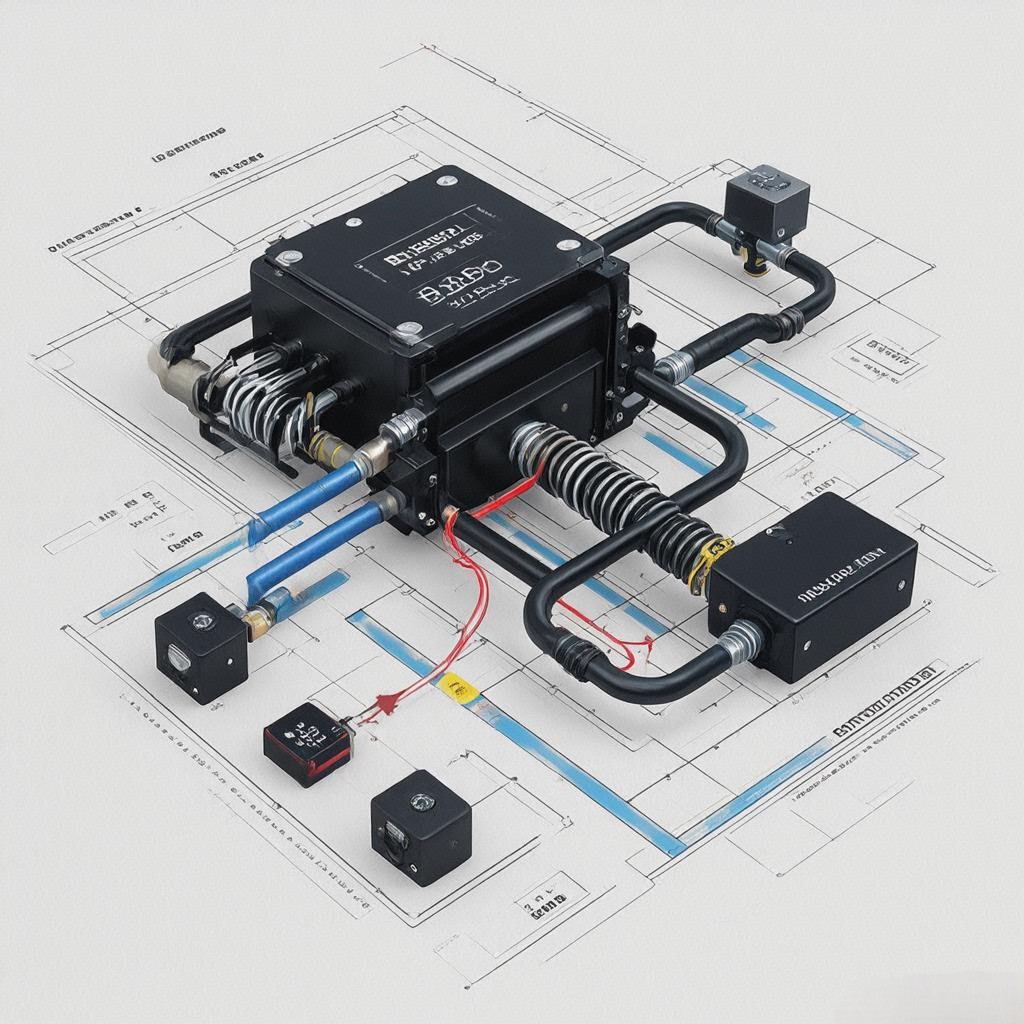
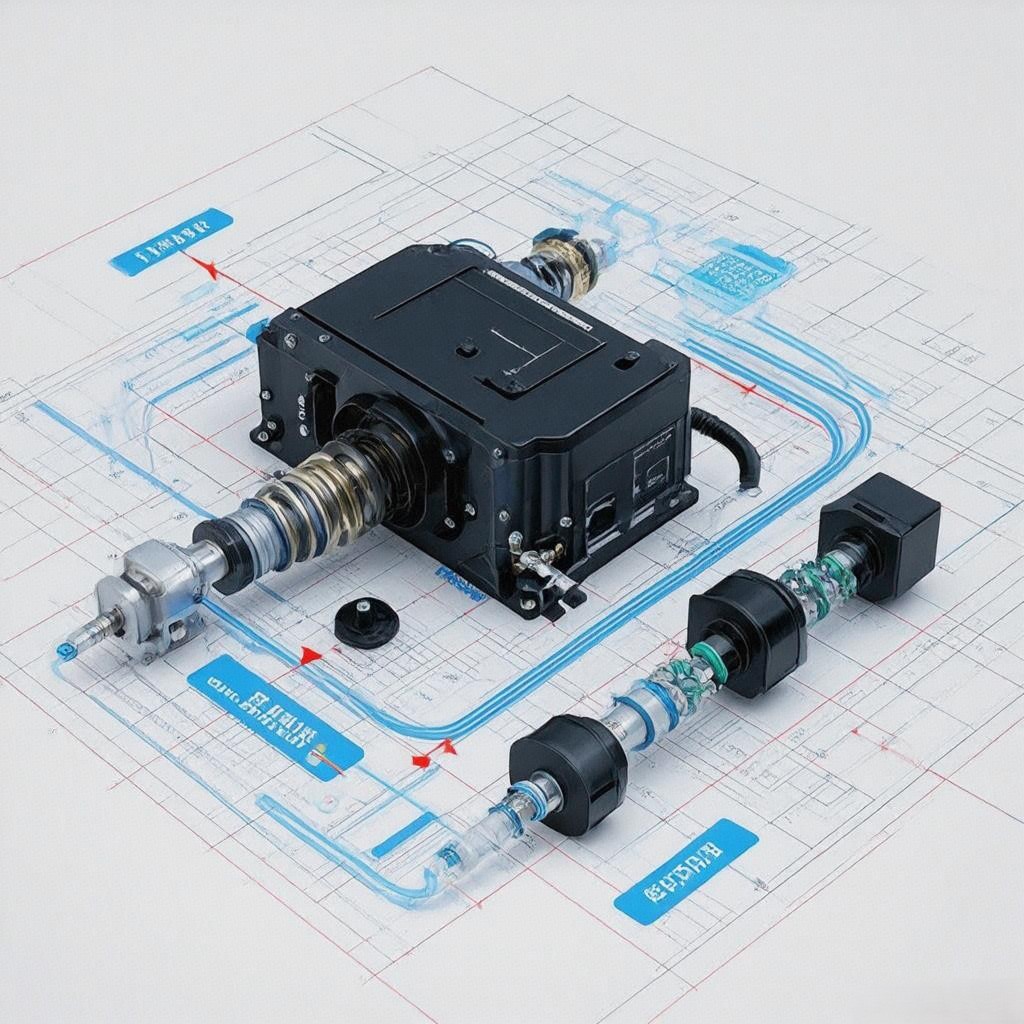
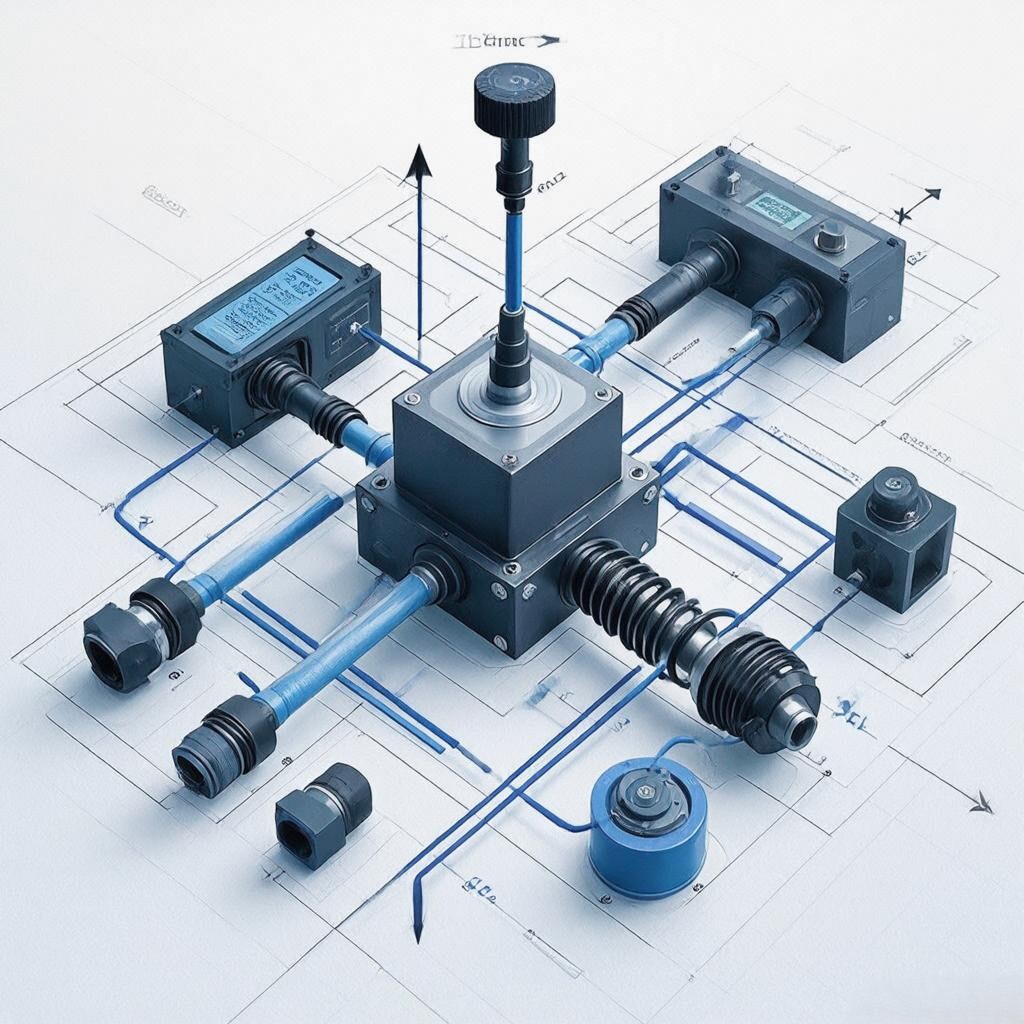
​​1. Core Functions of Air Suspension Control Systems​​
Modern air suspension control systems perform these critical functions:
- ​​Real-time ride height adjustment​​ (±2mm precision)
- ​​Dynamic load leveling​​ (compensation for 0-100% payload variations)
- ​​Adaptive damping control​​ (100+ adjustment levels)
- ​​System diagnostics​​ (fault detection with 99.9% accuracy)
- ​​Energy management​​ (optimized compressor operation)
​​Technical specifications​​:
- Response time: <50ms for height adjustment
- Pressure control accuracy: ±0.01MPa
- Operating temperature range: -40°C to +85°C
- Communication protocols: CAN FD (5Mbps), LIN (20kbps)
​​Industry impact​​: Vehicles equipped with advanced air suspension control systems demonstrate 30% better ride comfort and 25% longer component lifespan compared to passive systems.
​​2. System Architecture and Component Breakdown​​
​​2.1 Electronic Control Unit (ECU)​​
​​Hardware specifications​​:
- ​​32-bit microcontroller​​ (ARM Cortex-M7, 300MHz)
- ​​256KB Flash memory​​ with error correction coding
- ​​12-bit ADC​​ for sensor signal processing
- ​​Dual-core architecture​​ for safety-critical functions
​​Software features​​:
- ​​Real-time operating system​​ (AUTOSAR compliant)
- ​​Adaptive control algorithms​​ (fuzzy logic + PID)
- ​​Over-the-air (OTA) update capability​​
- ​​Cybersecurity protection​​ (AES-256 encryption)
​​2.2 Sensor Suite​​
​​Critical sensors and their functions​​:
- ​​Height sensors​​ (4-8 per vehicle):
- ​​Laser-based​​ (0.1mm resolution)
- ​​Strain gauge​​ (±1mm accuracy)
- ​​Capacitive​​ (immune to electromagnetic interference)
- ​​Pressure sensors​​ (2-4 per system):
- ​​Piezoresistive​​ (0.01MPa resolution)
- ​​Absolute pressure measurement​​ (0-1.5MPa range)
- ​​Accelerometers​​ (2-4 per axle):
- ​​MEMS technology​​ (±2g measurement range)
- ​​Frequency response​​: 0-100Hz
- ​​Temperature sensors​​ (2-4 locations):
- ​​NTC thermistors​​ (±2°C accuracy)
- ​​Thermal compensation algorithms​​
​​2.3 Actuation System​​
​​Valve control module​​:
- ​​High-speed solenoid valves​​ (15ms response time)
- ​​Proportional control​​ (0.1% step resolution)
- ​​Redundant circuit design​​ for fail-safe operation
​​Compressor control​​:
- ​​Variable speed drive​​ (PWM control)
- ​​Load sensing​​ (adaptive start/stop)
- ​​Energy recovery system​​ (regenerative braking integration)
​​3. Advanced Control Algorithms​​
​​3.1 Adaptive Ride Height Control​​
​​Dynamic adjustment strategies​​:
- ​​Load-dependent leveling​​ (compensation for 0-1,000kg payload changes)
- ​​Slope compensation​​ (5° grade adaptation)
- ​​Towing mode​​ (automatic rear height increase)
​​Control logic​​:
- ​​Fuzzy logic controller​​ with 5 membership functions
- ​​PID gain scheduling​​ for different operating conditions
- ​​Learning algorithm​​ to adapt to driver preferences
​​3.2 Adaptive Damping Control​​
​​Real-time adjustment parameters​​:
- ​​Frequency-based damping​​ (1-10Hz vibration filtering)
- ​​Road condition recognition​​ (5 preset modes + learning mode)
- ​​Cornering compensation​​ (lateral acceleration feedback)
​​Algorithm architecture​​:
- ​​Model predictive control (MPC)​​ for optimal damping selection
- ​​Neural network-based​​ road surface classification
- ​​Vehicle dynamics integration​​ with ESP/ABS systems
​​3.3 Energy Management System​​
​​Compressor control strategies​​:
- ​​Predictive start/stop​​ based on route data
- ​​Load-sharing algorithm​​ for multi-compressor systems
- ​​Energy recovery​​ from suspension movement
​​Power consumption optimization​​:
- ​​Sleep mode​​ during stationary periods
- ​​Variable voltage operation​​ (8-16V adaptive)
- ​​Thermal management​​ to reduce peak loads
​​4. System Integration and Vehicle Applications​​
​​4.1 Passenger Vehicles​​
​​Luxury SUVs and sedans​​:
- ​​4-corner independent control​​ with 16 adjustment levels
- ​​Integration with semi-active dampers​​
- ​​Driver profiles​​ with 3 customizable settings
​​Performance metrics​​:
- Ride height adjustment range: 70-120mm
- Response time: <0.3s for emergency adjustments
- NVH improvement: 20% noise reduction at 80km/h
​​4.2 Commercial Vehicles​​
​​Heavy-duty trucks and buses​​:
- ​​Axle load distribution control​​ (±1% accuracy)
- ​​Height-adjustable ramps​​ (50mm range)
- ​​Fuel efficiency mode​​ (optimized ride height for aerodynamics)
​​Specialized applications​​:
- ​​Semitrailer suspension​​ (40,000kg load capacity)
- ​​Fire trucks​​ (rapid deployment capability)
- ​​Mobile cranes​​ (precise load positioning)
​​4.3 Off-Highway and Specialty Vehicles​​
​​Agricultural equipment​​:
- ​​Field/road mode switching​​ (80mm height adjustment)
- ​​Load sensing​​ (1,000kg accuracy)
- ​​Corrosion protection​​ (salt spray testing)
​​Military and emergency vehicles​​:
- ​​Run-flat capability​​ (50km at zero pressure)
- ​​Ballistic protection​​ (STANAG 4569 Level 3)
- ​​Explosion-proof components​​ (ATEX certification)
​​5. Design Challenges and Engineering Solutions​​
​​5.1 Real-Time Performance Requirements​​
​​Solution approaches​​:
- ​​Hardware-in-the-loop (HIL) testing​​ with <1ms latency
- ​​Priority-based task scheduling​​ in ECU software
- ​​Distributed processing​​ across multiple ECUs
​​Performance metrics​​:
- Control cycle time: 10ms for critical functions
- Jitter: <0.1ms for time-sensitive operations
- Fault detection: <10ms response time
​​5.2 Electromagnetic Compatibility (EMC)​​
​​Design measures​​:
- ​​Shielded enclosures​​ (30dB attenuation at 1GHz)
- ​​Filtered connectors​​ (50V/m immunity)
- ​​Grounding strategy​​ with <0.1Ω resistance
​​Testing standards​​:
- ​​ISO 11452-2​​ (bulk current injection)
- ​​ISO 7637-2​​ (transient immunity)
- ​​CISPR 25​​ (radiated emissions)
​​5.3 Cybersecurity and Functional Safety​​
​​Security features​​:
- ​​Secure boot loader​​ with hardware root of trust
- ​​Message authentication​​ (HMAC-SHA256)
- ​​Intrusion detection system​​ (anomaly monitoring)
​​Safety compliance​​:
- ​​ISO 26262 ASIL C​​ for air suspension ECUs
- ​​Fail-operational architecture​​ with redundant paths
- ​​Watchdog timers​​ for software monitoring
​​6. Testing and Validation Methodologies​​
​​6.1 Component-Level Testing​​
​​ECU testing​​:
- ​​Temperature cycling​​ (-40°C to +85°C, 1,000 cycles)
- ​​EMC immunity testing​​ (100V/m field strength)
- ​​Software validation​​ (10,000+ test cases)
​​Sensor calibration​​:
- ​​End-of-line calibration​​ with ±0.1% accuracy
- ​​Cross-validation​​ between multiple sensors
- ​​Aging tests​​ (1,000 hours continuous operation)
​​6.2 System-Level Validation​​
​​Vehicle testing matrix​​:
- ​​Road conditions​​:
- Urban (stop-and-go traffic)
- Highway (steady-state cruising)
- Off-road (rough terrain)
- ​​Environmental conditions​​:
- Temperature extremes (-30°C to +50°C)
- Humidity (95% RH)
- Altitude (up to 3,000m)
​​Performance metrics​​:
- Ride height accuracy: ±1mm under dynamic conditions
- Response time: <50ms for 95% of adjustments
- Fault detection rate: >99.9%
​​6.3 Virtual Validation​​
​​Simulation tools​​:
- ​​Model-in-the-loop (MIL)​​ with MATLAB/Simulink
- ​​Software-in-the-loop (SIL)​​ for algorithm testing
- ​​Hardware-in-the-loop (HIL)​​ with dSPACE systems
​​Test scenarios​​:
- ​​10,000+ virtual test cases​​ covering all operating conditions
- ​​Edge case testing​​ (extreme loads, sudden maneuvers)
- ​​Long-term durability simulation​​ (10-year equivalent)
​​7. Market Trends and Future Developments​​
​​7.1 Electrification and Autonomous Driving​​
​​Key innovations​​:
- ​​48V mild hybrid integration​​ for energy-efficient operation
- ​​Predictive control algorithms​​ using vehicle-to-everything (V2X) data
- ​​Autonomous driving compatibility​​ with 10ms control updates
​​Technical challenges​​:
- ​​Latency reduction​​ to <10ms for autonomous emergency maneuvers
- ​​Energy management​​ for electric vehicle battery optimization
- ​​Sensor fusion​​ with LiDAR and camera systems
​​7.2 Advanced Materials and Manufacturing​​
​​Innovative approaches​​:
- ​​3D-printed manifold designs​​ for optimized airflow
- ​​Carbon fiber reinforced polymers​​ for lightweight housings
- ​​Additive manufacturing​​ of complex valve components
​​Sustainability focus​​:
- ​​Recyclable materials​​ in ECU casings
- ​​Energy-efficient manufacturing​​ processes
- ​​End-of-life recycling​​ strategies
​​7.3 Smart and Connected Suspension Systems​​
​​Emerging technologies​​:
- ​​Over-the-air (OTA) updates​​ for software improvements
- ​​Digital twin technology​​ for predictive maintenance
- ​​AI-based learning algorithms​​ for personalized driving profiles
​​User benefits​​:
- ​​Remote diagnostics​​ via smartphone apps
- ​​Customizable ride settings​​ through cloud connectivity
- ​​Proactive maintenance alerts​​ based on usage patterns
​​8. Case Studies: Real-World Implementations​​
​​Case Study 1: Premium Sedan Air Suspension Upgrade​​
A European luxury car manufacturer implemented a new air suspension control system in their flagship model, achieving:
- 22% improvement in ride comfort (ISO 2631-1 standard)
- 15% reduction in component wear
- Enhanced refinement during rapid acceleration/deceleration
​​Case Study 2: Commercial Truck Fleet Modernization​​
A global logistics company upgraded to a next-generation air suspension system, resulting in:
- 30% reduction in driver fatigue complaints
- 25% longer system lifespan
- Improved cargo security through better load leveling
​​Conclusion: The Intelligent Control Center of Modern Suspension​​
Air suspension control systems have evolved from simple height adjustment mechanisms to sophisticated electronic platforms that manage complex vehicle dynamics in real-time. As automotive technologies continue advancing toward full autonomy and electrification, these systems will play an increasingly critical role in ensuring safety, comfort, and efficiency.
​​Key takeaways:​​
- Modern air suspension control systems combine real-time sensing, adaptive algorithms, and robust actuation
- Advanced materials and manufacturing are enabling lighter, more efficient designs
- Integration with electrification and autonomy requires new engineering approaches
- Cybersecurity and functional safety are becoming paramount considerations
​​Final thought​​: The air suspension control system represents the perfect synergy between mechanical engineering and digital intelligence, constantly adapting to deliver the optimal balance between comfort, performance, and efficiency. As vehicles become more connected and autonomous, these systems will continue to evolve, incorporating artificial intelligence and predictive analytics to redefine the driving experience.
​​Call to Action​​
đź”§ Upgrading your vehicle’s suspension system?
⚙️ Explore our next-generation air suspension control solutions
📊 Request detailed technical specifications and performance data
#AirSuspension #VehicleDynamics #ElectronicControlSystems #AutomotiveEngineering #AdvancedDriverAssistanceSystems #Electrification #SmartMobility #FutureOfTransportation #FunctionalSafety #Cybersecurity