Internal combustion engines (ICEs) stand as remarkable feats of engineering, transforming fuel into mechanical energy with precision and power. At the heart of every engine lies a complex assembly of core components, each playing a critical role in the combustion process and power generation. This comprehensive technical analysis delves into the essential engine parts, their functions, advanced materials, and the ongoing innovations that are shaping the future of powertrain technology.
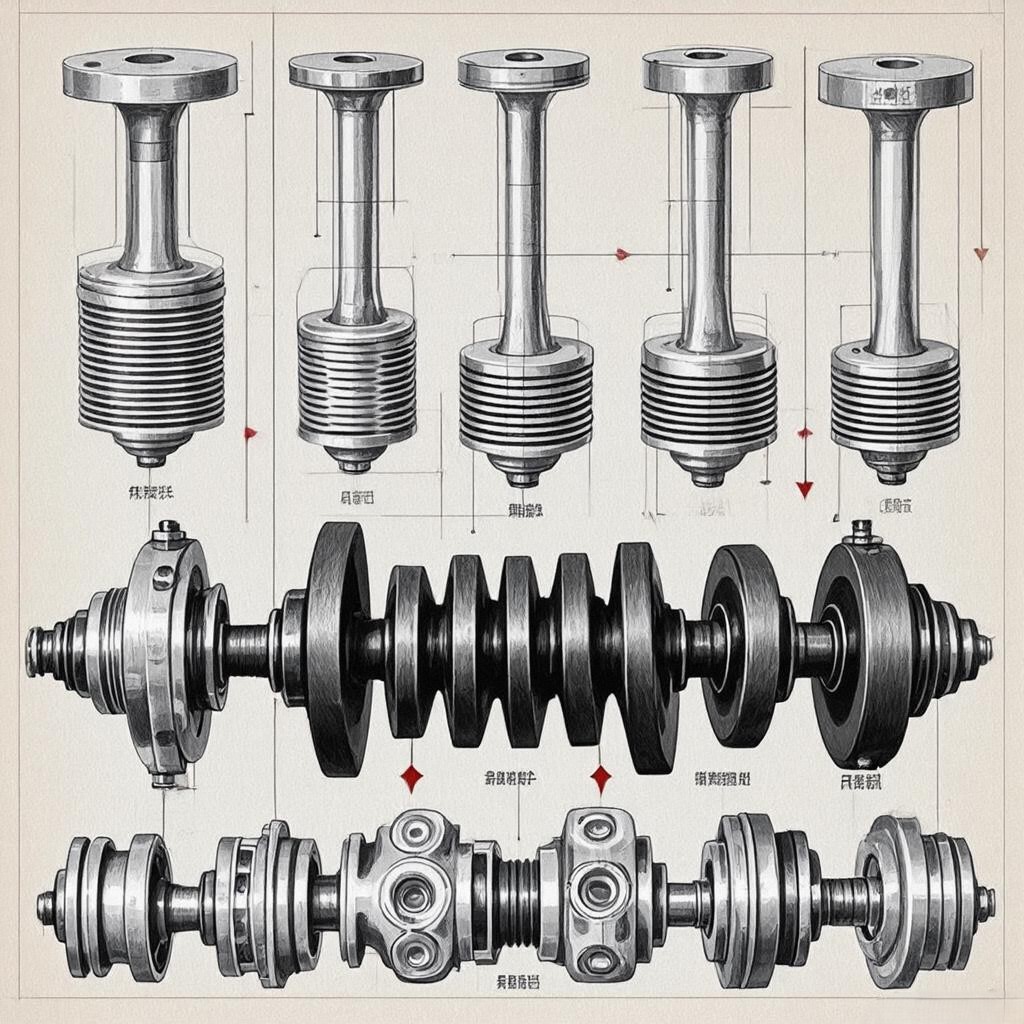
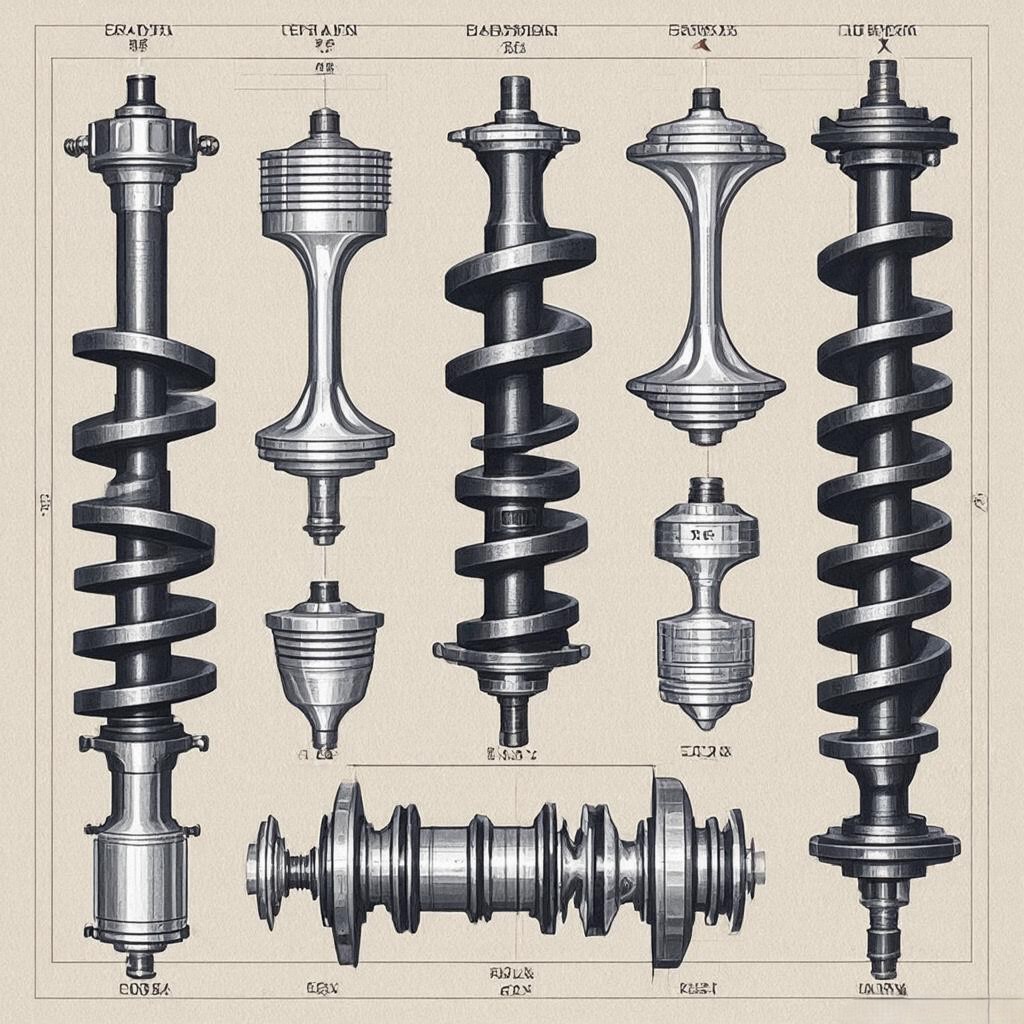
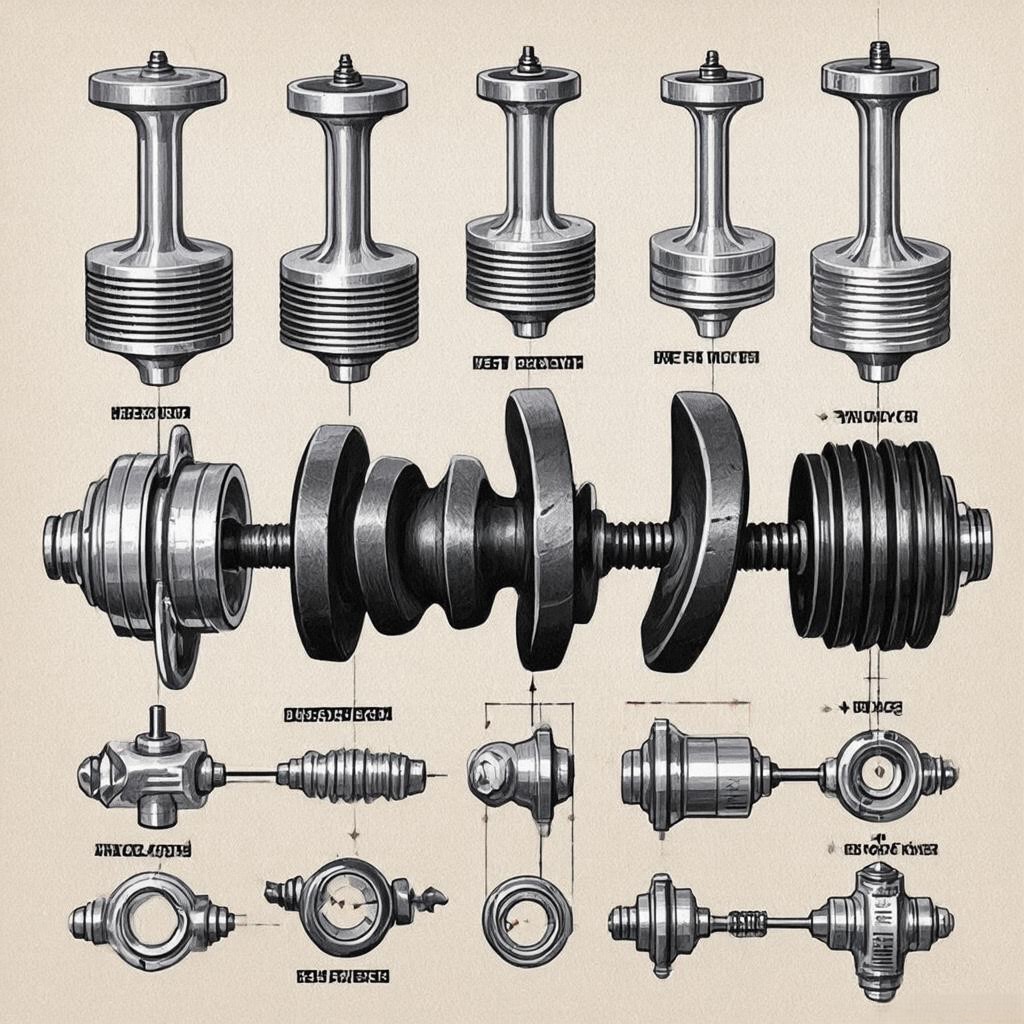
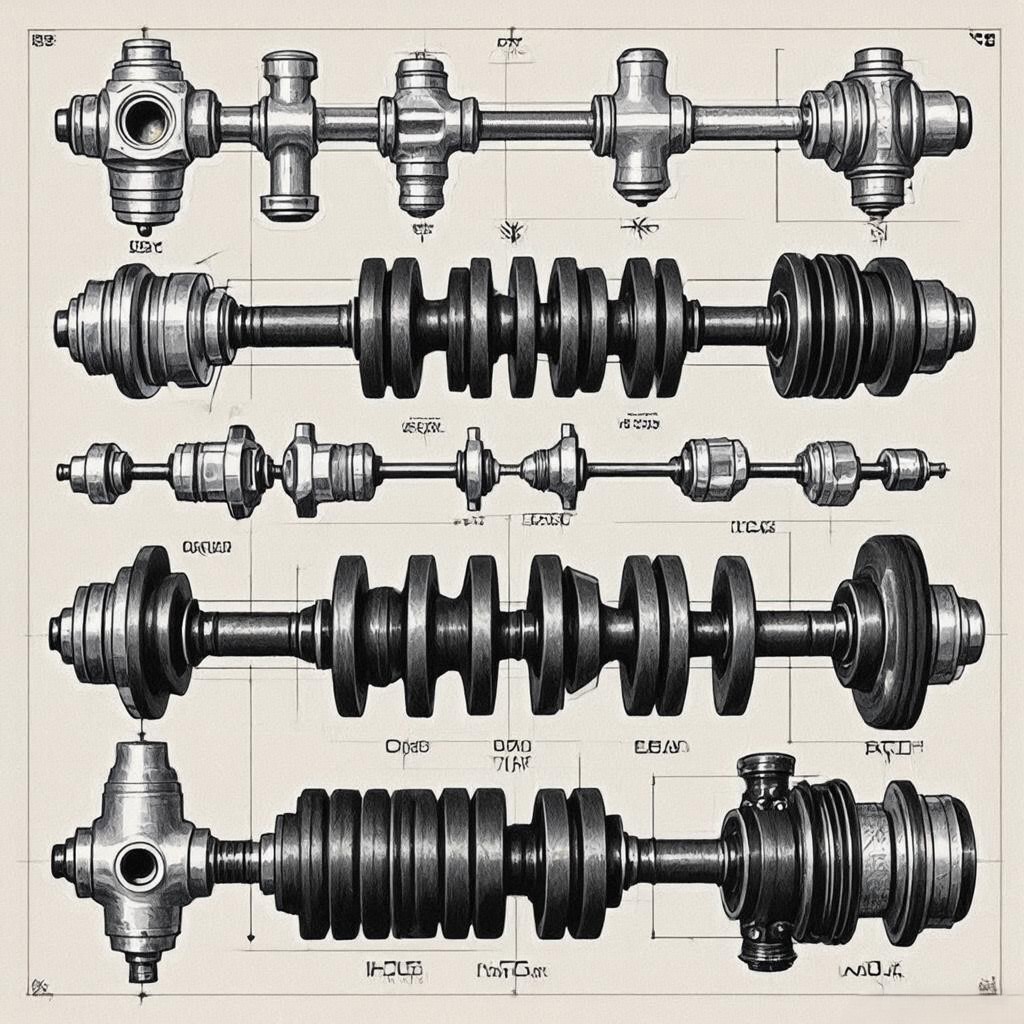
​​1. The Fundamental Role of Engine Components​​
Engine components work in perfect synchronization to convert chemical energy from fuel into mechanical power. These parts can be categorized into several functional groups:
- ​​Power generation components​​ (pistons, crankshaft, connecting rods)
- ​​Air/fuel delivery systems​​ (intake valves, fuel injectors, throttle body)
- ​​Exhaust and emission control​​ (exhaust valves, catalytic converters, EGR systems)
- ​​Lubrication and cooling​​ (oil pump, water pump, radiator)
- ​​Timing and control systems​​ (camshafts, timing belts/chains, sensors)
​​Technical significance​​: Modern engines achieve thermal efficiencies of 25-40%, with advanced designs pushing toward 50% efficiency through innovative component designs.
​​2. Core Engine Components and Their Functions​​
​​2.1 Pistons and Piston Rings​​
​​Piston Design and Materials​​:
- ​​Aluminum alloys​​: Lightweight (2.5-3.0 kg per piston) with high thermal conductivity
- ​​Forged vs. cast construction​​: Forged pistons offer superior strength for high-performance applications
- ​​Coatings​​: Thermal barrier coatings (ceramic) and oil-shedding polymers
​​Piston Ring Functions​​:
- ​​Compression rings​​: Seal combustion chamber (typically 2-3 rings per piston)
- ​​Oil control rings​​: Regulate oil film thickness on cylinder walls
- ​​Materials​​: High-carbon steel with molybdenum or chrome plating
​​Performance metrics​​:
- Piston speed: Up to 25 m/s in high-revving engines
- Temperature resistance: Up to 350°C surface temperature
​​2.2 Crankshaft and Connecting Rods​​
​​Crankshaft Construction​​:
- ​​Forged steel​​: High-strength alloy steels (e.g., SAE 4340)
- ​​Counterweights​​: Precision-balanced to reduce vibrations
- ​​Main bearings​​: Journal diameters typically 50-100 mm
​​Connecting Rod Features​​:
- ​​I-beam cross-section​​: Optimized strength-to-weight ratio
- ​​Powder metallurgy​​: Used for high-performance small-end bearings
- ​​Material​​: Forged steel or aluminum alloys for lightweight applications
​​Load specifications​​:
- Maximum combustion pressure: 15-20 MPa in turbocharged engines
- Bending stress: Up to 1,000 MPa during peak operation
​​2.3 Cylinder Block and Head​​
​​Block Materials and Design​​:
- ​​Cast iron​​: Traditional material with excellent wear resistance
- ​​Aluminum alloys​​: Lightweight (30-40% weight reduction vs. iron)
- ​​Closed-deck design​​: Enhanced cylinder rigidity for high boost applications
​​Cylinder Head Features​​:
- ​​Multi-valve configurations​​: 4-5 valves per cylinder for improved breathing
- ​​Variable valve timing (VVT)​​: Camshaft phasing mechanisms
- ​​Material​​: Aluminum alloys with sodium-filled exhaust valves
​​Thermal management​​:
- ​​Cooling jacket design​​: Optimized flow paths for coolant circulation
- ​​Thermal barrier coatings​​: Reduce cylinder head surface temperatures by 50-100°C
​​3. Air/Fuel Delivery and Combustion Systems​​
​​3.1 Intake and Exhaust Valves​​
​​Valve Materials and Coatings​​:
- ​​Intake valves​​: Silchrome-plated steel for corrosion resistance
- ​​Exhaust valves​​: Inconel alloys or Stellite-facing for high-temperature endurance
- ​​Sodium-filled exhaust valves​​: Improved heat dissipation
​​Valve Train Components​​:
- ​​Rocker arms​​: Roller-tip designs reduce friction
- ​​Valve springs​​: Dual-spring configurations prevent surge at high RPM
- ​​Variable valve lift (VVL)​​: Cam profile switching mechanisms
​​Performance specifications​​:
- Valve lift: 8-12 mm in modern engines
- Operating temperature: Up to 800°C for exhaust valves
​​3.2 Fuel Injection Systems​​
​​Injection Technologies​​:
- ​​Direct injection (DI)​​: 2,000-3,000 bar fuel pressure
- ​​Port fuel injection (PFI)​​: Lower pressure (3-5 bar)
- ​​Gasoline direct injection (GDI)​​: Piezo-electric injectors with 5-7 hole nozzles
​​Fuel Pump Systems​​:
- ​​High-pressure pumps​​: Plunger-type with camshaft drive
- ​​Common rail systems​​: Accumulator design for precise pressure control
- ​​Electric fuel pumps​​: 2-5 bar for PFI systems
​​Emission control integration​​:
- ​​Lean-burn combustion​​: Requires precise air/fuel ratio control
- ​​Exhaust gas recirculation (EGR)​​: Cooled EGR systems for NOx reduction
​​3.3 Turbocharging and Supercharging​​
​​Turbocharger Components​​:
- ​​Turbine wheel​​: Inconel alloys for high-temperature operation
- ​​Compressor wheel​​: Aluminum alloys with optimized blade geometry
- ​​Bearing systems​​: Floating journal bearings or ball bearings
​​Supercharger Types​​:
- ​​Roots type​​: Positive displacement, high boost at low RPM
- ​​Twin-screw​​: Continuous compression with higher efficiency
- ​​Centrifugal​​: Similar to turbochargers but belt-driven
​​Performance metrics​​:
- Boost pressure: Up to 3.5 bar in performance applications
- Efficiency gains: 20-30% power increase with forced induction
​​4. Lubrication and Cooling Systems​​
​​4.1 Lubrication System Components​​
​​Oil Pump Designs​​:
- ​​Gear pumps​​: Simple, reliable design for most applications
- ​​Variable displacement pumps​​: Adjust flow based on engine load
- ​​Electric oil pumps​​: For start-stop systems and hybrid applications
​​Oil Filter Technologies​​:
- ​​Full-flow filters​​: Remove 98% of contaminants >25μm
- ​​Bypass filters​​: Capture particles down to 1-2μm
- ​​Magnetic filters​​: Capture ferrous particles
​​Lubricant specifications​​:
- ​​Viscosity grades​​: 0W-20 to 10W-60 depending on climate and load
- ​​Additives​​: Detergents, anti-wear agents, viscosity modifiers
​​4.2 Cooling System Components​​
​​Water Pump Designs​​:
- ​​Mechanical pumps​​: Belt-driven with impeller designs
- ​​Electric pumps​​: Precise flow control for start-stop systems
- ​​Variable speed pumps​​: Adjust flow based on coolant temperature
​​Radiator and Heat Exchangers​​:
- ​​Aluminum radiators​​: Lightweight with high heat dissipation
- ​​Oil coolers​​: Integrated or standalone designs
- ​​Intercoolers​​: Air-to-air or air-to-water for charge air cooling
​​Coolant specifications​​:
- ​​Ethylene glycol-based​​: Typical 50/50 mix with water
- ​​Organic acid technology (OAT)​​: Extended-life coolants
- ​​Nanofluids​​: Advanced coolants with enhanced thermal properties
​​5. Timing and Valve Control Systems​​
​​5.1 Camshaft and Timing Components​​
​​Camshaft Materials and Design​​:
- ​​Forged steel​​: High-strength for performance applications
- ​​Cast iron​​: Cost-effective for standard engines
- ​​Variable valve timing (VVT)​​: Phasing mechanisms with hydraulic or electric actuators
​​Timing Belt/Chain Systems​​:
- ​​Timing belts​​: Fiber-reinforced rubber with tensioner systems
- ​​Timing chains​​: Roller chains with hydraulic tensioners
- ​​Chain guides​​: Polymer or metal designs to reduce noise
​​Performance specifications​​:
- Cam lift: 8-15 mm depending on engine design
- Valve timing variation: ±1° crank angle precision
​​5.2 Variable Valve Timing and Lift Systems​​
​​VVT Technologies​​:
- ​​Hydraulic VVT​​: Oil-pressure actuated phasers
- ​​Electric VVT​​: Precise motor-driven control
- ​​Camless systems​​: Fully electronic valve actuation
​​VVL (Variable Valve Lift) Systems​​:
- ​​BMW Valvetronic​​: Continuously variable lift control
- ​​Honda VTEC​​: Switching between high/low lift profiles
- ​​Ferrari Variable Lift​​: Advanced electro-hydraulic systems
​​Benefits​​:
- Improved fuel efficiency (10-20% gains)
- Enhanced low-end torque and high-RPM power
- Reduced emissions through optimized combustion
​​6. Advanced Materials and Manufacturing Innovations​​
​​6.1 Lightweight Materials​​
​​Aluminum Alloys​​:
- ​​319 alloy​​: Common for engine blocks (good castability)
- ​​356 alloy​​: Improved mechanical properties
- ​​A356-T6​​: Heat-treated for higher strength
​​Magnesium Alloys​​:
- ​​AZ91D​​: Used for valve covers and other non-critical parts
- ​​WE43​​: High-temperature magnesium alloys for exhaust components
​​Titanium Alloys​​:
- ​​Ti-6Al-4V​​: Used in high-performance valves and connecting rods
- ​​Beta-C​​: Advanced titanium alloys for extreme applications
​​6.2 Additive Manufacturing​​
​​3D-Printed Components​​:
- ​​Complex manifold designs​​: Optimized flow paths
- ​​Lightweight brackets​​: Topology-optimized structures
- ​​Prototyping​​: Rapid development of new designs
​​Direct Metal Laser Sintering (DMLS)​​:
- ​​Stainless steel and Inconel parts​​: For high-temperature applications
- ​​Titanium components​​: Reduced weight with maintained strength
​​6.3 Precision Manufacturing Techniques​​
​​CNC Machining​​:
- ​​5-axis machining​​: Complex part geometries
- ​​High-speed machining​​: Improved surface finish
- ​​Micro-machining​​: For small precision components
​​Casting Technologies​​:
- ​​Die casting​​: High-volume production of aluminum parts
- ​​Sand casting​​: For large, complex components
- ​​Investment casting​​: Precision parts with excellent surface finish
​​7. Testing and Validation of Engine Components​​
​​7.1 Component-Level Testing​​
​​Piston and Ring Testing​​:
- ​​Firing tests​​: Simulated combustion conditions
- ​​Friction testing​​: Ring/bore interaction analysis
- ​​Thermal cycling​​: Thermal shock resistance
​​Crankshaft Testing​​:
- ​​Bending fatigue tests​​: 10^8 cycles minimum
- ​​Surface durability tests​​: Scuffing resistance evaluation
- ​​Balancing verification​​: ±1gmm imbalance tolerance
​​7.2 System-Level Validation​​
​​Engine Dynamometer Testing​​:
- ​​Power and torque measurement​​: ±1% accuracy
- ​​Emission testing​​: CO, HC, NOx, PM measurements
- ​​Fuel consumption analysis​​: BSFC (Brake Specific Fuel Consumption)
​​Endurance Testing​​:
- ​​1,000-hour durability tests​​: Simulated real-world conditions
- ​​Cold start testing​​: -30°C ambient conditions
- ​​High-altitude testing​​: Up to 5,000m equivalent
​​7.3 Virtual Validation Methods​​
​​Finite Element Analysis (FEA)​​:
- ​​Stress analysis​​: Predict component failure points
- ​​Thermal analysis​​: Heat dissipation modeling
- ​​Vibration analysis​​: NVH (Noise, Vibration, Harshness) prediction
​​Computational Fluid Dynamics (CFD)​​:
- ​​Airflow optimization​​: Intake and exhaust port design
- ​​Combustion simulation​​: Flame propagation modeling
- ​​Cooling system analysis​​: Coolant flow distribution
​​8. Future Trends in Engine Component Development​​
​​8.1 Electrification and Hybridization​​
​​48V Mild Hybrid Systems​​:
- ​​Belt-integrated starter generators (BISG)​​
- ​​P0/P2 hybrid configurations​​
- ​​Regenerative braking integration​​
​​High-Voltage Components​​:
- ​​Electric water pumps​​: Reduced parasitic losses
- ​​Electric oil pumps​​: Precise lubrication control
- ​​Integrated starter generators (ISG)​​
​​8.2 Alternative Fuels and Combustion Concepts​​
​​Gasoline Compression Ignition (GCI)​​:
- ​​Lean-burn combustion​​: Improved efficiency
- ​​Advanced injection timing​​: Controlled auto-ignition
- ​​EGR optimization​​: Reduced NOx emissions
​​Hydrogen Internal Combustion Engines (H2-ICE)​​:
- ​​Modified fuel systems​​: High-pressure hydrogen delivery
- ​​Combustion chamber redesign​​: Flame speed optimization
- ​​Materials compatibility​​: Hydrogen embrittlement resistance
​​8.3 Advanced Manufacturing and Materials​​
​​Additive Manufacturing​​:
- ​​Complex cooling channel designs​​
- ​​Topology-optimized components​​
- ​​Rapid prototyping of new designs​​
​​Nanomaterials and Coatings​​:
- ​​Diamond-like carbon (DLC) coatings​​: Reduced friction
- ​​Thermal barrier coatings​​: Improved heat management
- ​​Self-healing materials​​: Crack repair capabilities
​​Conclusion: The Heart of Modern Transportation​​
Engine components represent the pinnacle of mechanical engineering, combining precision design, advanced materials, and innovative manufacturing to deliver reliable power generation. As the automotive industry evolves toward electrification and alternative fuels, these components continue to adapt, incorporating new technologies to meet ever-stricter efficiency and emission standards.
​​Key takeaways:​​
- Modern engines integrate dozens of precisely engineered components working in harmony
- Advanced materials and manufacturing are pushing performance boundaries
- Electrification is transforming traditional engine architectures
- Sustainability drives innovation in component design and materials
​​Final thought​​: While electric vehicles capture headlines, the internal combustion engine remains a remarkable engineering achievement. The ongoing evolution of engine components ensures this technology will continue playing a vital role in global transportation for decades to come, even as it evolves to meet new challenges and opportunities.
​​Call to Action​​
đź”§ Interested in engine component technologies?
⚙️ Explore our advanced engineering solutions for next-generation powertrains
📊 Request detailed specifications on our latest high-performance components
#EngineTechnology #AutomotiveEngineering #PowertrainInnovation #InternalCombustion #AdvancedMaterials #ManufacturingExcellence #SustainableMobility #FutureOfTransportation
Quisque tempor urna sed metus lobortis, vitae posuere lacus varius. Curabitur justo velit, laoreet vel tristique quis, aliquam nec nisl. Vestibulum vel arcu nunc.