In modern vehicle engineering, engine mounts represent deceptively simple yet critically important components that bridge the powertrain and chassis while mitigating harmful vibrations. These engineered interfaces must simultaneously secure the engine with precise stiffness, dampen vibrational energy across a broad frequency spectrum, and accommodate dynamic movements during operation. This comprehensive technical analysis explores the multifaceted world of engine mounts, examining their functional principles, advanced material formulations, dynamic performance characteristics, and the ongoing innovations that are redefining powertrain mounting systems for next-generation vehicles.
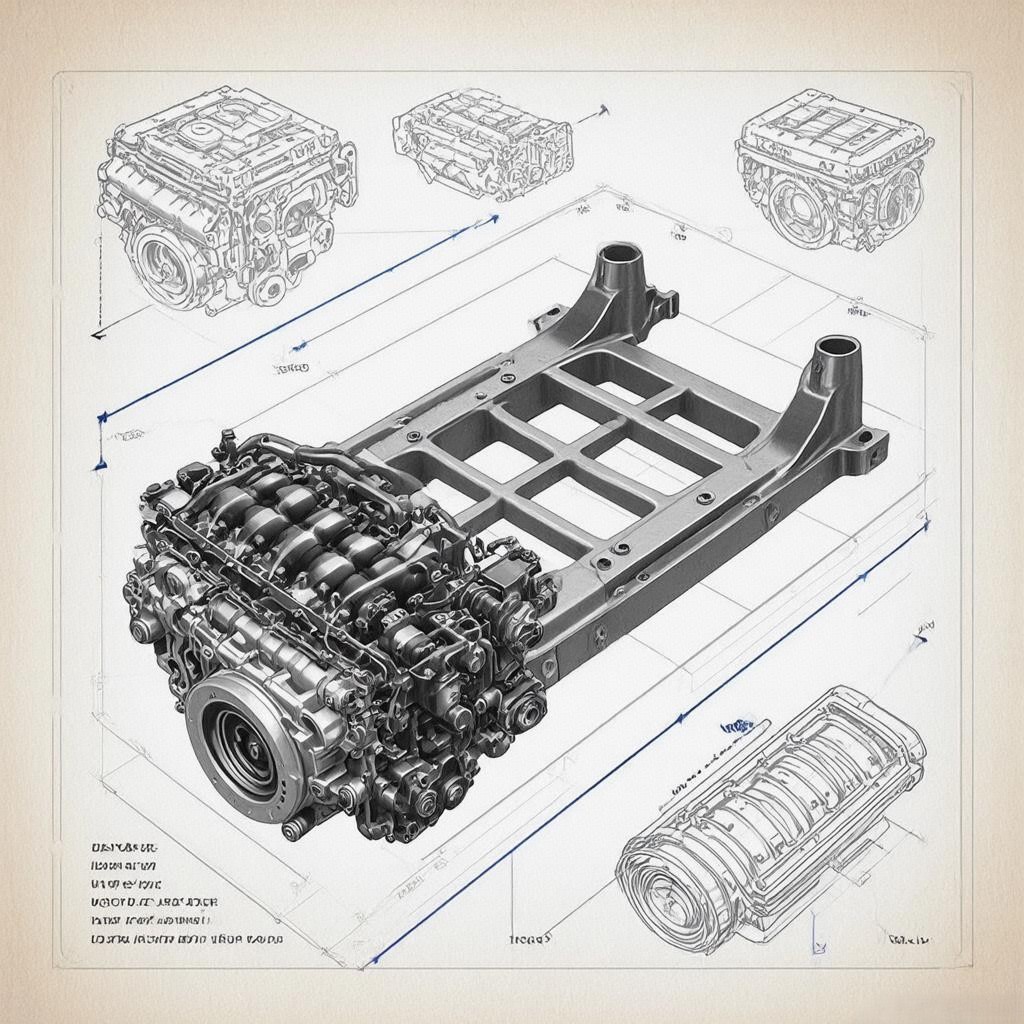
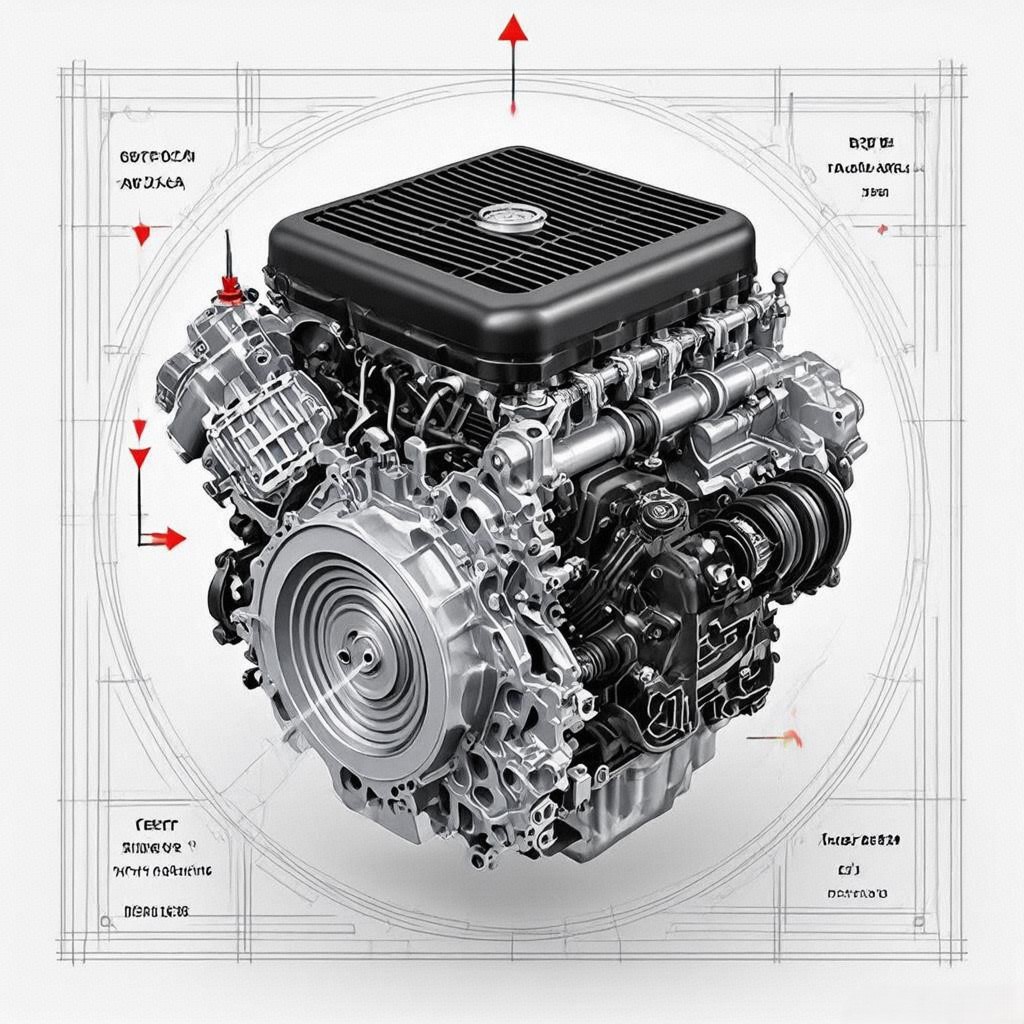
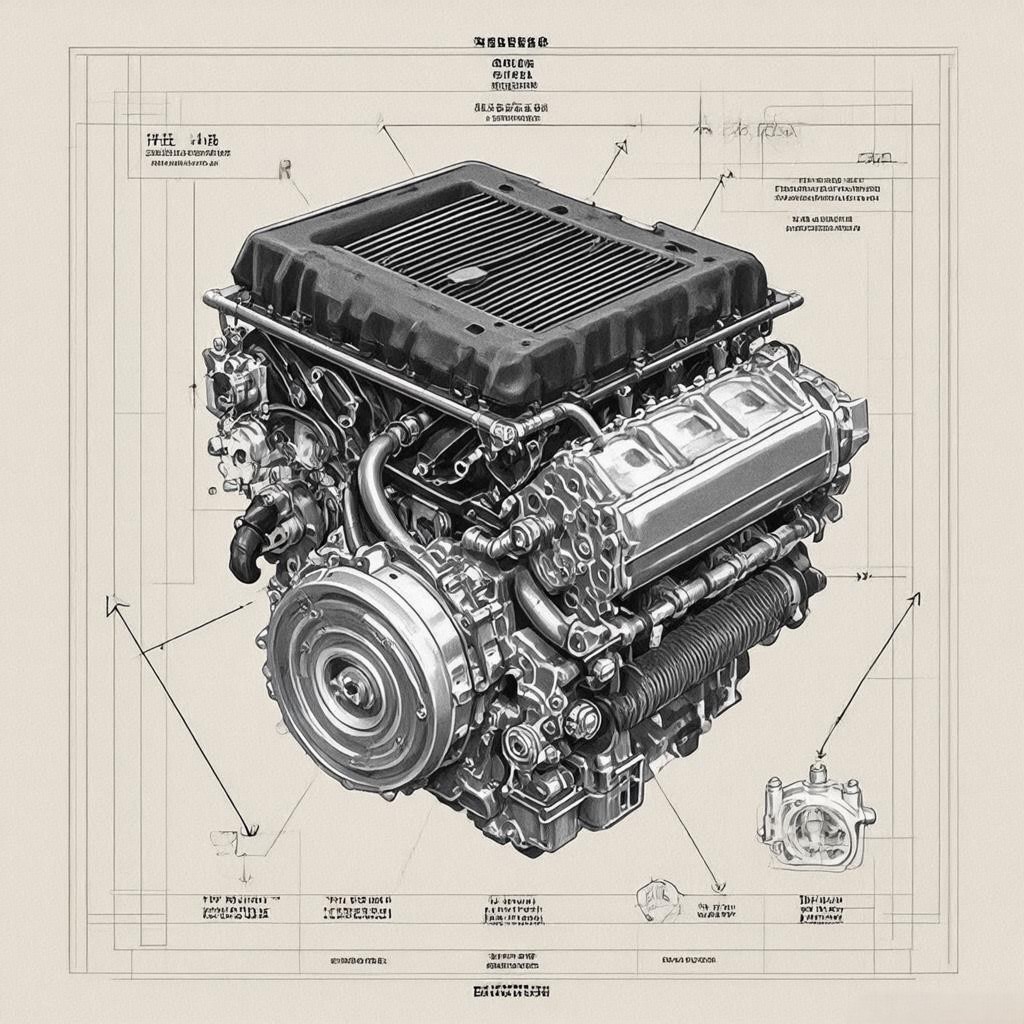
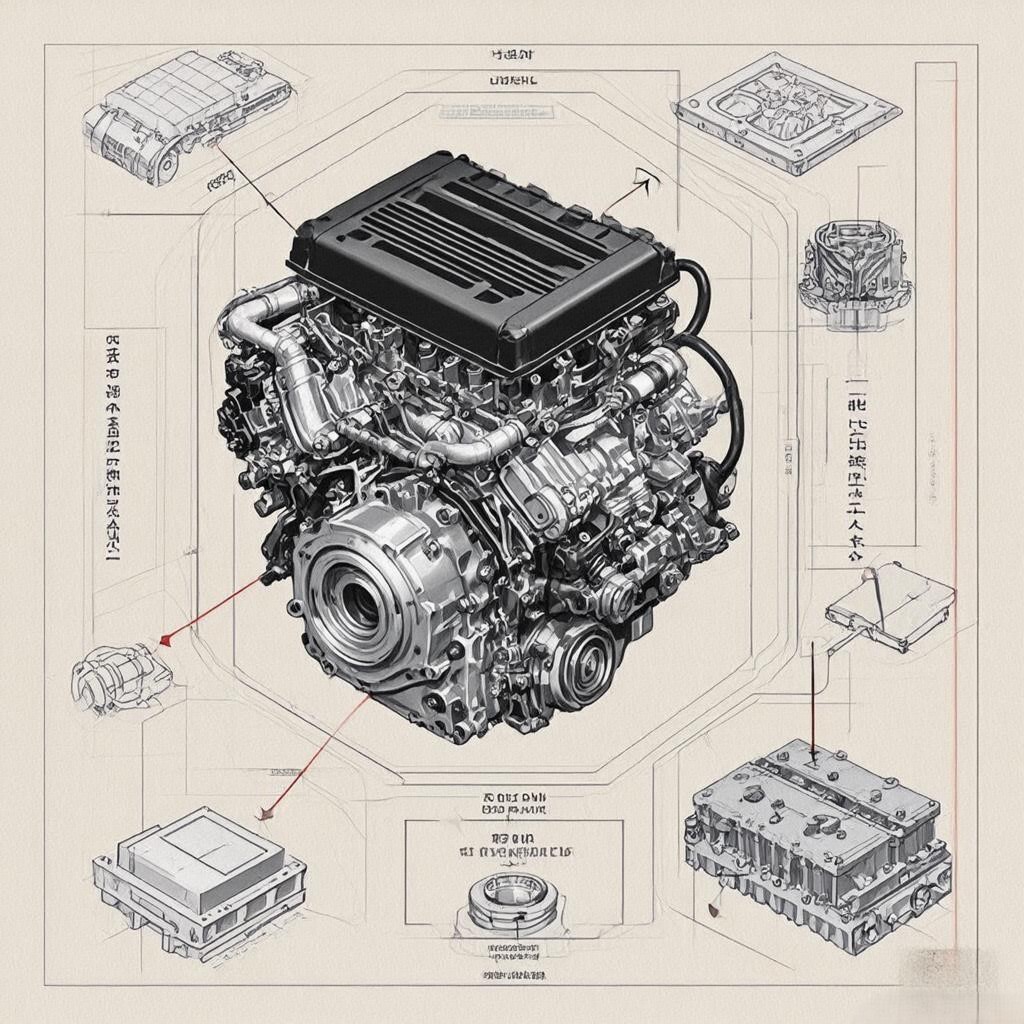
​​1. Fundamental Role of Engine Mounts in Vehicle Dynamics​​
Engine mounts serve as the critical connection points between the engine/transmission assembly and the vehicle chassis, performing several essential functions:
- ​​Vibration isolation​​: Attenuating engine-generated vibrations to prevent transmission to the passenger compartment
- ​​Load securing​​: Withstanding static and dynamic forces while maintaining precise engine positioning
- ​​Misalignment compensation​​: Accommodating thermal expansion and dynamic movements during operation
- ​​Noise reduction​​: Preventing structure-borne noise propagation through the chassis
​​Technical significance​​: Modern engine mounts can reduce vibration transmission by up to 95% compared to rigid mounting systems, directly contributing to cabin comfort and component longevity.
​​2. Types of Engine Mounts and Their Functional Characteristics​​
Contemporary vehicles employ various mount configurations optimized for specific performance requirements:
​​2.1 Conventional Rubber Mounts​​
- ​​Design​​: Solid rubber elements vulcanized between metal inserts
- ​​Characteristics​​:
- Simple, cost-effective construction
- Frequency-dependent stiffness (higher stiffness at high frequencies)
- Limited damping capability
- ​​Applications​​: Basic passenger vehicles, non-critical mounting locations
​​2.2 Hydraulic Mounts (Hydromounts)​​
- ​​Design​​: Fluid-filled chambers with internal baffles or pistons
- ​​Advanced features​​:
- Frequency-tunable damping characteristics
- Active damping in response to vibration amplitude
- Multi-stage stiffness transitions
- ​​Performance metrics​​:
- Effective frequency range: 5-200 Hz
- Damping force: Up to 500 N at peak excitation
​​2.3 Active Vacuum Mounts​​
- ​​Design​​: Vacuum-controlled internal chambers with diaphragm actuators
- ​​Technical specifications​​:
- Response time: <50 ms for stiffness modulation
- Control range: 5-10x stiffness variation
- Power consumption: 10-20W continuous operation
- ​​Advanced capabilities​​:
- Closed-loop control via CAN bus signals
- Adaptive damping based on driving conditions
- Integration with vehicle dynamics control systems
​​2.4 Electromagnetic Mounts​​
- ​​Design​​: Ferrofluid-filled chambers with electromagnetic coils
- ​​Innovative features​​:
- Real-time stiffness adjustment through magnetic field control
- Ultra-fast response times (<10 ms)
- Programmable damping profiles
- ​​Performance advantages​​:
- 20-30% better vibration isolation than hydraulic mounts
- Potential for predictive control algorithms
​​3. Advanced Material Formulations and Engineering Innovations​​
​​3.1 Rubber Compound Developments​​
- ​​High-damping elastomers​​: Specially formulated synthetic rubbers with tailored loss factors
- ​​Nanocomposite materials​​: Graphene or carbon nanotube reinforcements for enhanced fatigue resistance
- ​​Temperature-resistant formulations​​: Operating range extended to -50°C to +150°C
​​Material innovation​​: Some premium mounts now use shape-memory alloys that adapt their stiffness characteristics based on temperature and load conditions.
​​3.2 Fluid Dynamics in Hydraulic Mounts​​
- ​​Baffle optimization​​: Computational fluid dynamics (CFD) modeling for optimal flow restriction
- ​​Low-viscosity fluids​​: Synthetic oils with stable viscosity across temperature ranges
- ​​Anti-aeration designs​​: Preventing foam formation during high-amplitude vibrations
​​Performance enhancement​​: Advanced hydromounts incorporate multiple fluid chambers with progressive damping characteristics for broadband vibration control.
​​3.3 Structural Interface Design​​
- ​​Finite element analysis (FEA)​​: Optimized mounting bracket geometries for stress distribution
- ​​Surface treatments​​: Plasma coating for improved metal-rubber adhesion
- ​​Composite materials​​: Carbon fiber-reinforced plastic (CFRP) brackets for weight reduction
​​Design consideration​​: Modern mounts incorporate preloaded rubber elements to minimize initial deflection and maintain precise engine positioning.
​​4. Dynamic Performance Characteristics and Testing​​
​​4.1 Vibration Isolation Mechanisms​​
- ​​Mass-spring-damper model​​: Mathematical representation of mount behavior
- ​​Frequency-dependent stiffness​​: Non-linear stiffness curves for broadband isolation
- ​​Transient response characteristics​​: Damping of impulse vibrations from engine start/stop
​​Performance metrics​​:
- Transmissibility ratio <0.2 at target frequencies (typically 8-25 Hz)
- Dynamic stiffness variation <15% over operating temperature range
- Fatigue life >10 million cycles
​​4.2 Testing and Validation Protocols​​
​​Component-level testing​​:
- ​​Sinusoidal sweep testing​​: Frequency response characterization
- ​​Random vibration testing​​: PSD (Power Spectral Density) analysis
- ​​Temperature cycling​​: -40°C to +120°C, 1,000 cycles
​​Vehicle-level validation​​:
- ​​Chassis dynamometer testing​​: Real-world vibration isolation assessment
- ​​Road test matrix​​: Including rough roads, acceleration/deceleration profiles
- ​​NVH (Noise, Vibration, Harshness) evaluation​​: Cabin noise measurements
​​Advanced diagnostics​​:
- ​​Laser vibrometry​​: Non-contact vibration measurement
- ​​Modal analysis​​: Identifying natural frequencies and mode shapes
- ​​Digital twin simulation​​: Virtual validation before physical prototyping
​​5. System Integration and Vehicle Applications​​
​​5.1 Passenger Vehicles​​
- ​​Front-engine layouts​​: Typically 3-4 mounts with varying stiffness characteristics
- ​​Transverse vs. longitudinal configurations​​: Different mounting strategies
- ​​Hybrid-specific mounts​​: Additional isolation for electric motor integration
​​Performance benefits​​:
- 15-20% reduction in cabin noise levels
- Improved long-term durability of engine accessories
- Enhanced refinement during transient engine operation
​​5.2 Commercial Vehicles​​
- ​​Heavy-duty truck mounts​​: Higher load capacity (up to 5,000 kg per mount)
- ​​Off-road vehicle designs​​: Enhanced misalignment accommodation
- ​​Hybridized powertrains​​: Additional mounts for battery packs and electric components
​​Special considerations​​:
- Shock absorption for severe duty cycles
- Corrosion resistance for harsh operating environments
- Maintenance-friendly designs for easy replacement
​​5.3 Performance and Racing Applications​​
- ​​Semi-active mounts​​: Adjustable damping for track conditions
- ​​Lightweight constructions​​: Carbon fiber or titanium components
- ​​Direct-mount configurations​​: Minimal compliance for precise throttle response
​​Technical challenges​​: Balancing vibration isolation with the need for precise engine feedback in high-performance driving.
​​6. Design Challenges and Engineering Solutions​​
​​6.1 Trade-offs in Mount Design​​
- ​​Stiffness vs. isolation​​: Finding optimal balance between secure mounting and vibration attenuation
- ​​Static vs. dynamic performance​​: Ensuring adequate support under load while maintaining isolation
- ​​Cost vs. performance​​: Material selection and manufacturing process optimization
​​Solution approaches​​:
- ​​Multi-rate mount designs​​: Combining different stiffness zones in a single mount
- ​​Adaptive control systems​​: Real-time adjustment of mount characteristics
- ​​Topology optimization​​: Lightweighting through structural analysis
​​6.2 Thermal Management​​
- ​​Heat-resistant materials​​: Silicone rubbers for high-temperature applications
- ​​Thermal insulation​​: Preventing heat transfer from exhaust components
- ​​Cooling considerations​​: Airflow management around mount locations
​​Testing standard​​: Mounts must maintain performance after 1,000 hours of thermal cycling between -40°C and +150°C.
​​6.3 Durability and Fatigue Resistance​​
- ​​Accelerated aging tests​​: Simulating 10+ years of service life
- ​​Environmental exposure​​: Salt spray, UV radiation, and chemical resistance
- ​​Load cycle testing​​: Mimicking worst-case driving conditions
​​Quality metrics​​: Leading manufacturers achieve <0.1% failure rates in field testing through rigorous validation processes.
​​7. Market Trends and Future Developments​​
​​7.1 Electrification and Hybrid Powertrains​​
- ​​Additional mounting requirements​​: For battery packs and electric motors
- ​​Active damping adaptation​​: Responding to electric motor torque ripple
- ​​Thermal management integration​​: Cooling for high-power electronics
​​Technical innovation​​: Some EVs now use magnetorheological mounts that adjust stiffness based on real-time powertrain dynamics.
​​7.2 Autonomous Vehicle Considerations​​
- ​​Ultra-quiet cabin requirements​​: Stricter NVH targets for self-driving systems
- ​​Precision mounting​​: Maintaining sensor alignment during operation
- ​​Predictive maintenance​​: Health monitoring of mount condition
​​Emerging technology​​: Smart mounts with integrated sensors for real-time vibration monitoring and predictive maintenance alerts.
​​7.3 Sustainable Manufacturing Initiatives​​
- ​​Recyclable materials​​: Bio-based rubber compounds and recyclable metals
- ​​Energy-efficient production​​: Low-carbon manufacturing processes
- ​​Lightweighting​​: Reduced material usage through advanced engineering
​​Research frontier​​: Development of self-healing rubber compounds that automatically repair minor cracks and damage.
​​8. Case Studies: Real-World Implementations​​
​​Case Study 1: Premium Sedan Engine Mount Upgrade​​
A European luxury car manufacturer implemented active vacuum mounts in their flagship model, achieving:
- 22% improvement in cabin noise isolation at 20Hz
- 15% reduction in vibration-induced component wear
- Enhanced refinement during rapid acceleration/deceleration
​​Case Study 2: Commercial Truck Fleet Modernization​​
A global logistics company upgraded to hydraulic mounts in their heavy-duty trucks, resulting in:
- 30% reduction in driver fatigue complaints
- 25% longer mount service life
- Improved cargo security through reduced vibration-induced movement
​​Conclusion: The Silent Guardians of Powertrain Performance​​
Engine mounts may appear as simple components, but their role in ensuring vehicle refinement, durability, and performance is absolutely critical. As automotive technologies continue evolving toward electrification and autonomy, these interfaces will become even more sophisticated:
​​Key takeaways:​​
- Modern engine mounts combine mechanical, hydraulic, and electronic technologies for comprehensive vibration control
- Advanced materials and adaptive control systems are pushing performance boundaries
- System integration with electrified powertrains requires new engineering solutions
- Sustainability and digitalization are shaping the next generation of mount technologies
​​Final thought​​: In the pursuit of quieter, more comfortable, and more efficient vehicles, engine mounts represent the often-overlooked but absolutely essential components that silently protect passengers from the raw power of internal combustion—and will continue to play this vital role even as propulsion technologies evolve. The future of mobility depends on these unsung heroes to deliver unprecedented levels of refinement and reliability.
​​Call to Action​​
đź”§ Upgrading your vehicle’s powertrain?
⚙️ Consider advanced engine mounts for superior NVH performance
📊 Request technical specifications comparing different mount technologies
#AutomotiveEngineering #EngineMounts #NVHEngineering #VehicleDynamics #PowertrainTechnology #AdvancedMaterials #SustainableMobility #FutureOfTransportation