In the intricate ecosystem of modern vehicle safety systems, sensor cable assemblies serve as the critical neural pathways that transmit vital braking system data between sensors, control units, and actuators. These specialized wiring harnesses have evolved from simple electrical conduits into sophisticated systems that enable real-time monitoring, precise control, and advanced safety features. This comprehensive technical analysis explores the engineering behind sensor cable assemblies, their critical role in braking systems, and how they’re shaping the future of vehicle safety.
​​1. The Critical Role of Sensor Cable Assemblies in Braking Systems​​
Sensor cable assemblies form the information superhighway that allows modern braking systems to function with unprecedented precision. Their primary functions include:
- ​​Data transmission​​: Carrying signals from wheel speed sensors, brake pressure sensors, and temperature sensors to electronic control units (ECUs)
- ​​Power delivery​​: Supplying low-voltage power to sensor electronics
- ​​Signal integrity​​: Maintaining clean, uninterrupted communication between system components
​​Technical specifications typically include:​​
- Wire gauge: AWG 22-26 for signal wires, AWG 18-20 for power lines
- Signal types: Analog (0-5V), digital (CAN/LIN protocols), and PWM signals
- Environmental ratings: IP67/IP69K for dust/water resistance, -40°C to +125°C operational range
​​Industry significance​​: With the rise of advanced driver-assistance systems (ADAS) and autonomous driving technologies, sensor cable assemblies have become as critical to braking performance as the mechanical components themselves.
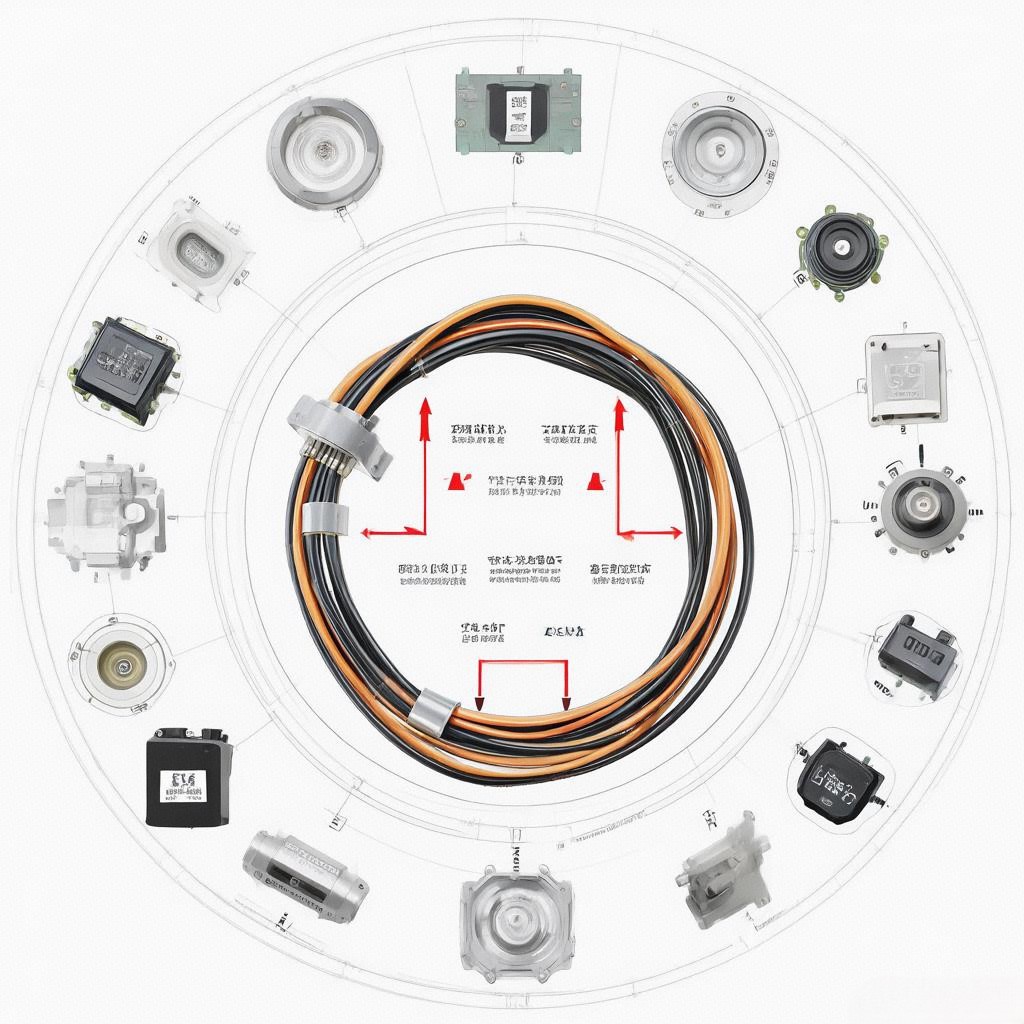
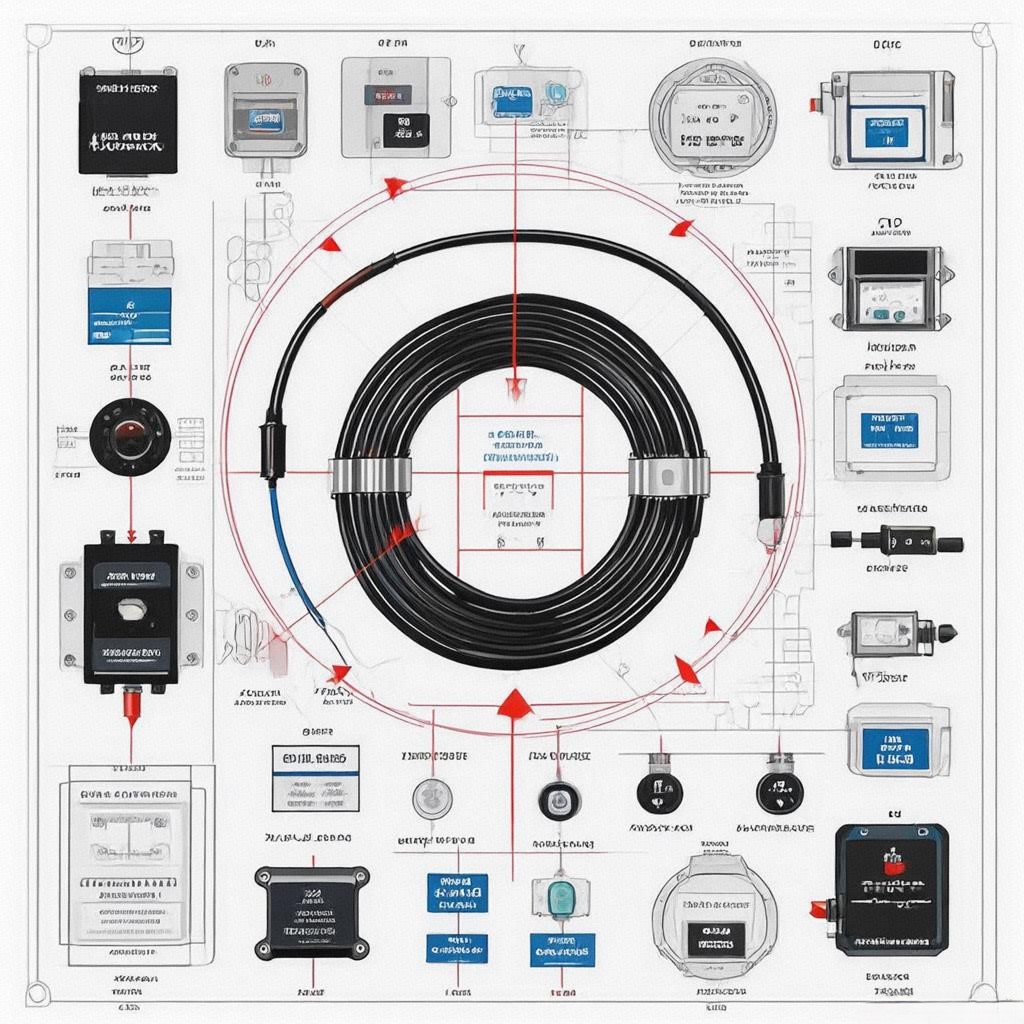
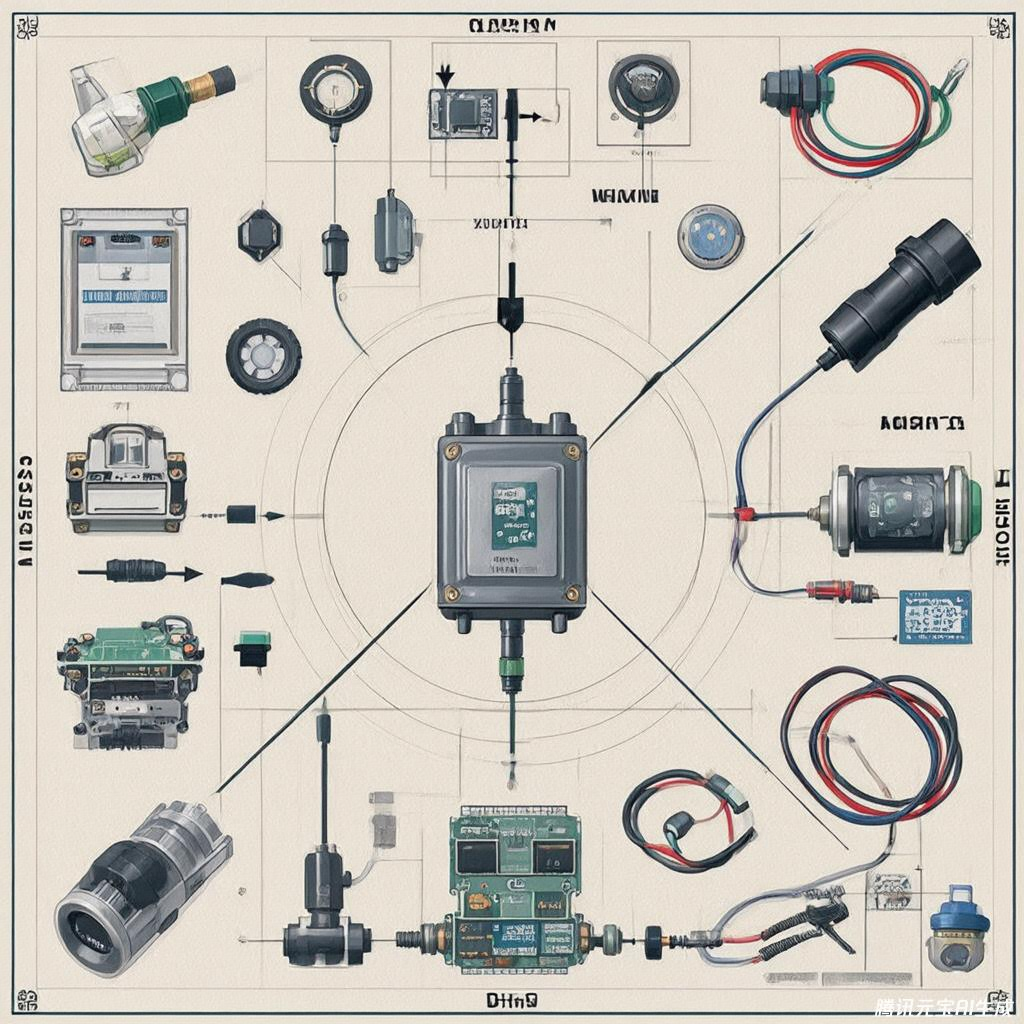
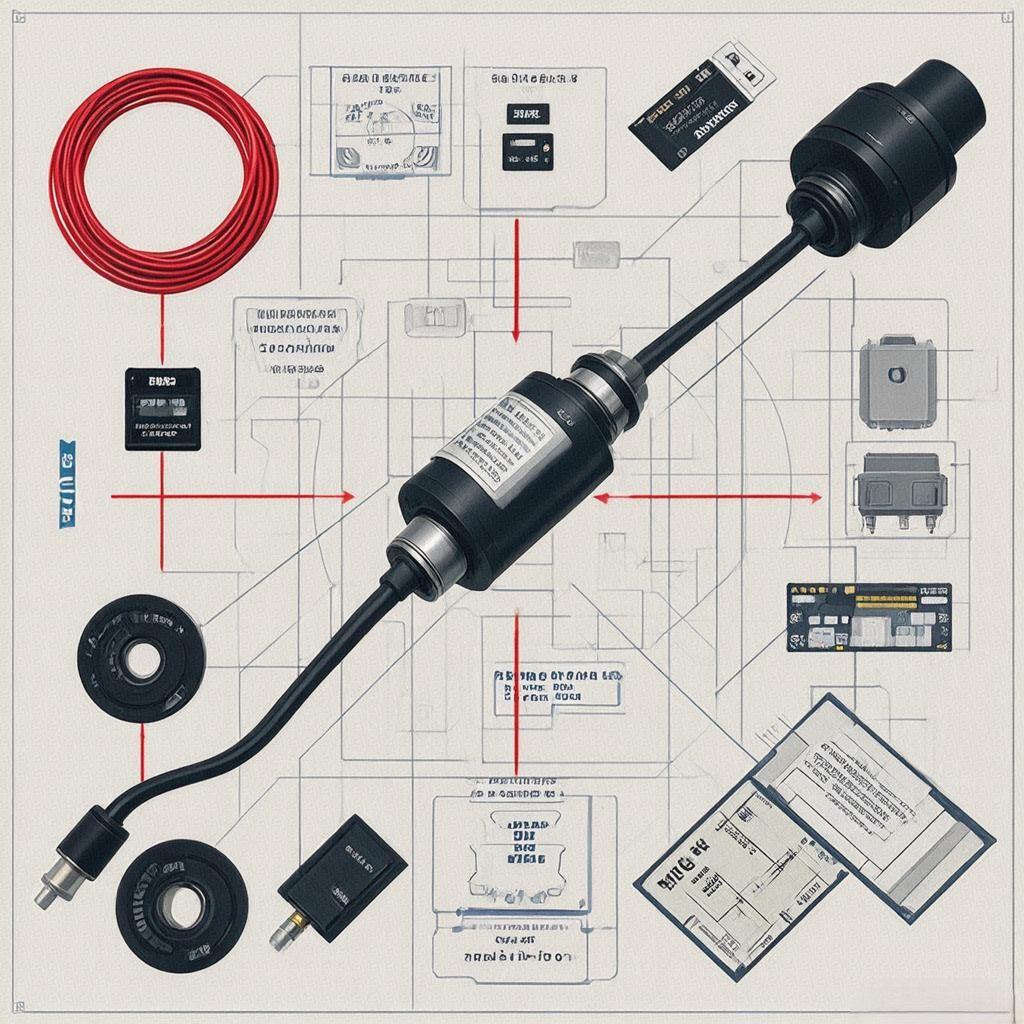
​​2. Components and Construction of Modern Sensor Cable Assemblies​​
A typical high-performance sensor cable assembly comprises several specialized elements working in concert:
​​2.1 Conductors and Insulation​​
- ​​Stranded copper conductors​​: Provide flexibility and reliable signal transmission
- ​​Cross-linked polyethylene (XLPE) insulation​​: Offers excellent thermal and chemical resistance
- ​​Shielding options​​:
- Braided copper shielding for EMI protection (typically 85-95% coverage)
- Aluminum foil shielding for high-frequency noise suppression
- Unshielded configurations for cost-sensitive applications
​​2.2 Connector Systems​​
- ​​Sealed connectors​​: IP67-rated with multiple locking mechanisms
- ​​Terminal types​​:
- Crimped terminals for high-reliability connections
- IDC (insulation displacement connectors) for cost-effective assembly
- Soldered connections for permanent installations
- ​​Contact materials​​: Gold-plated or silver-plated for corrosion resistance
​​2.3 Protective Sleeving​​
- ​​Thermoplastic elastomer (TPE) braiding​​: Provides flexibility and abrasion resistance
- ​​Metallic armor​​: Stainless steel mesh for mechanical protection
- ​​Fire-resistant outer jackets​​: UL-rated materials for automotive applications
​​Design consideration​​: Modern assemblies often incorporate color-coding and labeling systems for easy identification during installation and maintenance.
​​3. Advanced Functional Features in Contemporary Sensor Cable Assemblies​​
Recent technological advancements have transformed sensor cable assemblies into intelligent components:
​​3.1 Signal Integrity Enhancements​​
- ​​Twisted pair configurations​​: Minimize electromagnetic interference (EMI)
- ​​Differential signaling​​: Cancels out common-mode noise for critical sensors
- ​​Impedance matching​​: Ensures signal fidelity across the entire frequency range
​​Technical achievement​​: Some high-end assemblies achieve signal-to-noise ratios (SNR) exceeding 60dB for wheel speed sensor signals.
​​3.2 Diagnostic Capabilities​​
- ​​Built-in continuity monitoring​​: Detects open or short circuits
- ​​Resistance sensing​​: Identifies connector corrosion or wire damage
- ​​Temperature monitoring​​: Detects hotspots that could indicate insulation breakdown
​​Industry compliance​​: Meets ISO 14229 (UDS) and ISO 16750-2 (electrical loads) diagnostic standards.
​​3.3 Environmental Protection Innovations​​
- ​​Gel-filled connectors​​: Prevent moisture ingress in critical connections
- ​​Hydrophobic coatings​​: Repel water and prevent corrosion
- ​​UV-resistant materials​​: Maintain performance after prolonged sun exposure
​​Testing standard​​: Many assemblies now exceed 1,000 hours of salt spray testing (ASTM B117).
​​4. System Integration and Application Scenarios​​
Sensor cable assemblies play vital roles across various vehicle platforms:
​​4.1 Passenger Vehicles​​
- ​​Anti-lock braking systems (ABS)​​: Connects wheel speed sensors to ECU
- ​​Electronic stability control (ESC)​​: Transmits yaw rate and lateral acceleration data
- ​​Regenerative braking​​: Links brake pressure sensors with powertrain control units
​​Performance metrics​​: Modern vehicles may have 10-15 individual sensor circuits in their braking systems.
​​4.2 Commercial Trucks and Buses​​
- ​​Air pressure monitoring​​: Connects pneumatic sensors to brake control modules
- ​​Load sensing​​: Transmits weight distribution data for dynamic braking adjustment
- ​​Trailer connectivity​​: Standardized connectors for tractor-trailer communication
​​Durability requirement​​: Heavy-duty assemblies must withstand 10 million vibration cycles (ISO 16750-3).
​​4.3 Electric and Hybrid Vehicles​​
- ​​Battery management system (BMS) integration​​: Monitors thermal conditions of brake components
- ​​Regenerative braking coordination​​: Balances friction and electric braking forces
- ​​Autonomous driving systems​​: Provides real-time data for AI-based braking decisions
​​Special consideration​​: EVs require additional shielding to protect against high-voltage system interference.
​​5. Design Challenges and Engineering Solutions​​
Developing reliable sensor cable assemblies requires overcoming significant technical hurdles:
​​5.1 Signal Integrity in Electromagnetic Environments​​
- ​​Multi-layer shielding​​: Combines braided and foil shielding for comprehensive EMI protection
- ​​Grounding schemes​​: Star grounding minimizes ground loops
- ​​Filtering components​​: Ferrite beads suppress high-frequency noise
​​Innovation highlight​​: Some manufacturers now use computational electromagnetics (CEM) simulation to optimize shielding effectiveness before physical prototyping.
​​5.2 Mechanical Durability​​
- ​​Flexible yet robust construction​​: Balances flexibility for routing with resistance to abrasion
- ​​Strain relief designs​​: Prevents wire breakage at connector interfaces
- ​​Vibration-resistant terminations​​: Locking mechanisms maintain connection integrity
​​Testing protocol​​: Assemblies undergo 5,000+ hours of vibration testing per ISO 16750-3.
​​5.3 Thermal Management​​
- ​​Heat-resistant insulation​​: Maintains performance up to 125°C
- ​​Thermal dissipation pathways​​: Prevents heat buildup in high-current sections
- ​​Cold-temperature flexibility​​: Special polymers maintain flexibility below -40°C
​​Material innovation​​: Some advanced assemblies use nanocomposite insulation materials with enhanced thermal properties.
​​6. Testing and Validation Protocols​​
Ensuring sensor cable assembly reliability requires rigorous testing procedures:
​​6.1 Electrical Performance Testing​​
- ​​Continuity and insulation resistance​​: Verifies circuit integrity
- ​​Signal transmission quality​​: Measures insertion loss and crosstalk
- ​​High-potential (hipot) testing​​: Detects insulation defects
​​6.2 Environmental Durability Testing​​
- ​​Temperature cycling​​: -40°C to +125°C rapid transitions
- ​​Humidity exposure​​: 95% RH at 40°C for extended periods
- ​​Salt spray testing​​: 1,000+ hours for corrosion resistance
​​6.3 Mechanical Robustness Testing​​
- ​​Flex life testing​​: 10,000+ cycles of repeated bending
- ​​Vibration testing​​: 5-2000Hz random vibrations
- ​​Impact resistance​​: Simulates crash conditions
​​Quality metric​​: Leading manufacturers achieve <0.01% failure rates in field testing through comprehensive validation processes.
​​7. Market Trends and Future Developments​​
The sensor cable assembly market is undergoing significant transformation:
​​7.1 Electrification and Autonomous Driving​​
- ​​High-speed data transmission​​: Support for 100Mbps+ Ethernet protocols
- ​​Redundant signal paths​​: Enhanced safety for autonomous systems
- ​​Integrated sensors​​: Combining connectivity with sensing capabilities
​​7.2 Sustainable Design Initiatives​​
- ​​Recyclable materials​​: End-of-life component recycling programs
- ​​Energy-efficient manufacturing​​: Reduced carbon footprint production processes
- ​​Biodegradable insulation​​: Environmentally friendly material options
​​7.3 Advanced Manufacturing Techniques​​
- ​​Automated assembly​​: Robotic precision ensures consistent quality
- ​​Digital twin technology​​: Virtual testing reduces development time
- ​​Additive manufacturing​​: Custom connector designs for specific applications
​​Research frontier​​: Development of self-healing insulation materials that automatically repair minor damage.
​​8. Case Studies: Real-World Implementation​​
​​Case Study 1: Premium EV Brake System Upgrade​​
A European automaker implemented advanced sensor cable assemblies in their flagship EV, achieving:
- 20% improvement in signal transmission reliability
- 30% reduction in electromagnetic interference
- 40% faster fault detection capabilities
​​Case Study 2: Commercial Truck Fleet Modernization​​
A global logistics company upgraded their truck fleet with heavy-duty sensor cable assemblies, resulting in:
- 50% reduction in wiring-related brake system failures
- 200,000+ mile reliability in extreme operating conditions
- Simplified maintenance through standardized connector designs
​​Conclusion: The Invisible Backbone of Braking Performance​​
Sensor cable assemblies may not command the same attention as brake calipers or rotors, but their role in ensuring safe and reliable braking performance is absolutely critical. As vehicles become more sophisticated, these assemblies continue to evolve to meet new challenges:
​​Key takeaways:​​
- Modern sensor cable assemblies combine electrical, mechanical, and environmental performance
- Advanced shielding and diagnostic features enhance system reliability
- Integration with vehicle networks enables next-generation safety features
- Future developments will focus on higher data rates and sustainability
​​Final thought​​: In the era of autonomous vehicles and electrification, sensor cable assemblies represent the vital neural network that ensures every braking decision is executed with precision—quietly powering the next generation of vehicle safety innovations.
​​Call to Action​​
đź”§ Upgrading your brake system?
⚙️ Consider high-performance sensor cable assemblies for enhanced reliability
📊 Request performance data comparing traditional vs. advanced cable solutions
#AutomotiveEngineering #BrakeTechnology #SensorSystems #VehicleSafety #ADAS #FunctionalSafety #SmartMobility #FutureOfTransportation