In modern vehicles, Wheel Speed Sensors (WSS) serve as the fundamental data source that enables critical safety systems like Anti-lock Braking Systems (ABS) and Traction Control Systems (TCS) to function effectively. These unassuming components, often hidden behind wheels or integrated into transmission components, play a pivotal role in vehicle dynamics control, accident prevention, and overall driving safety. This comprehensive technical analysis explores the complete ecosystem of WSS technology, their engineering principles, implementation strategies, and transformative impact on automotive safety systems.
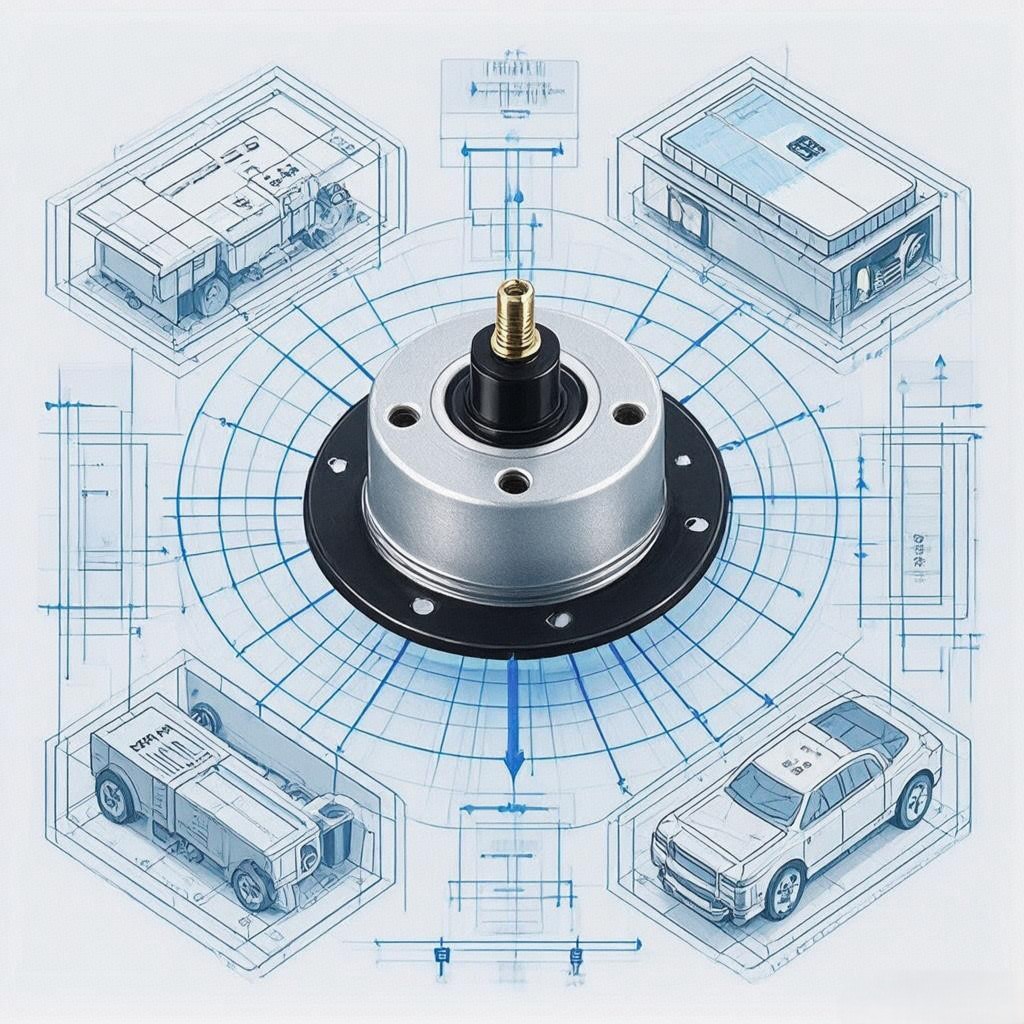
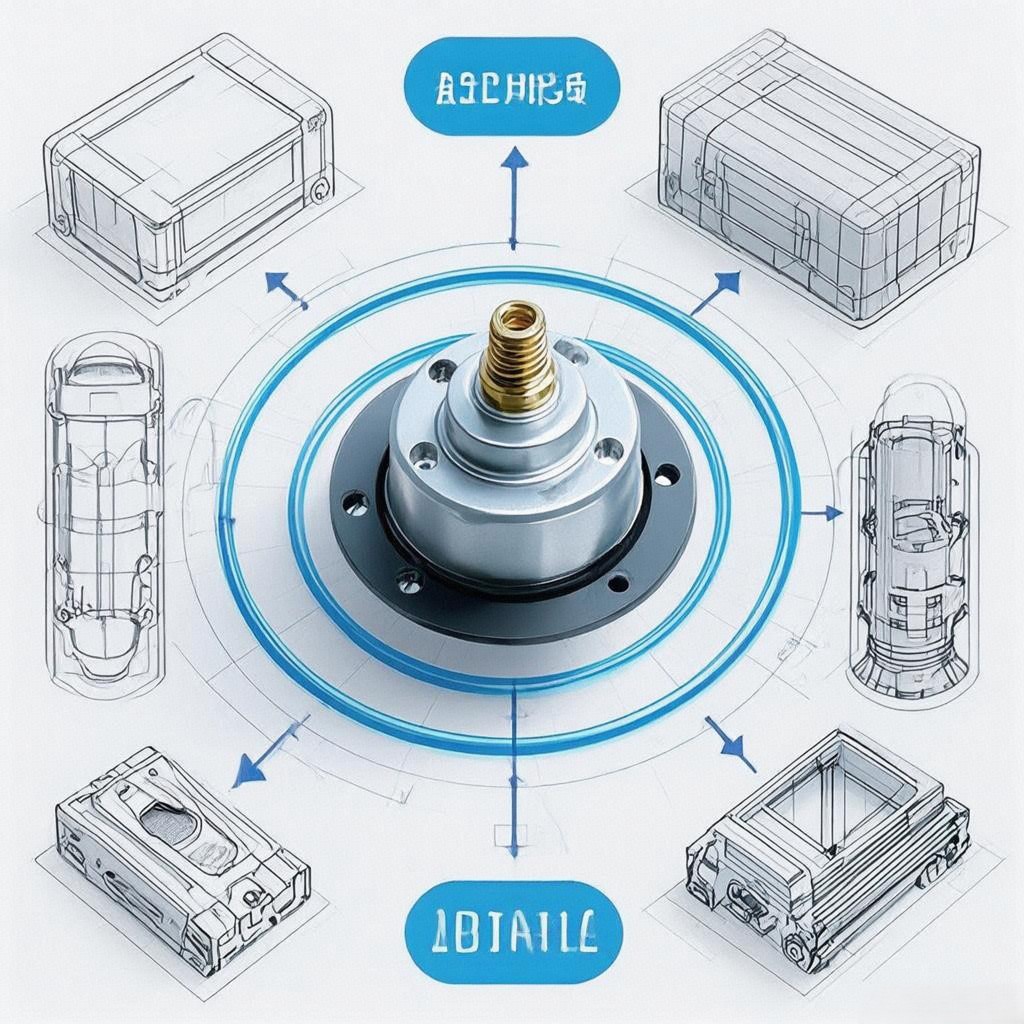
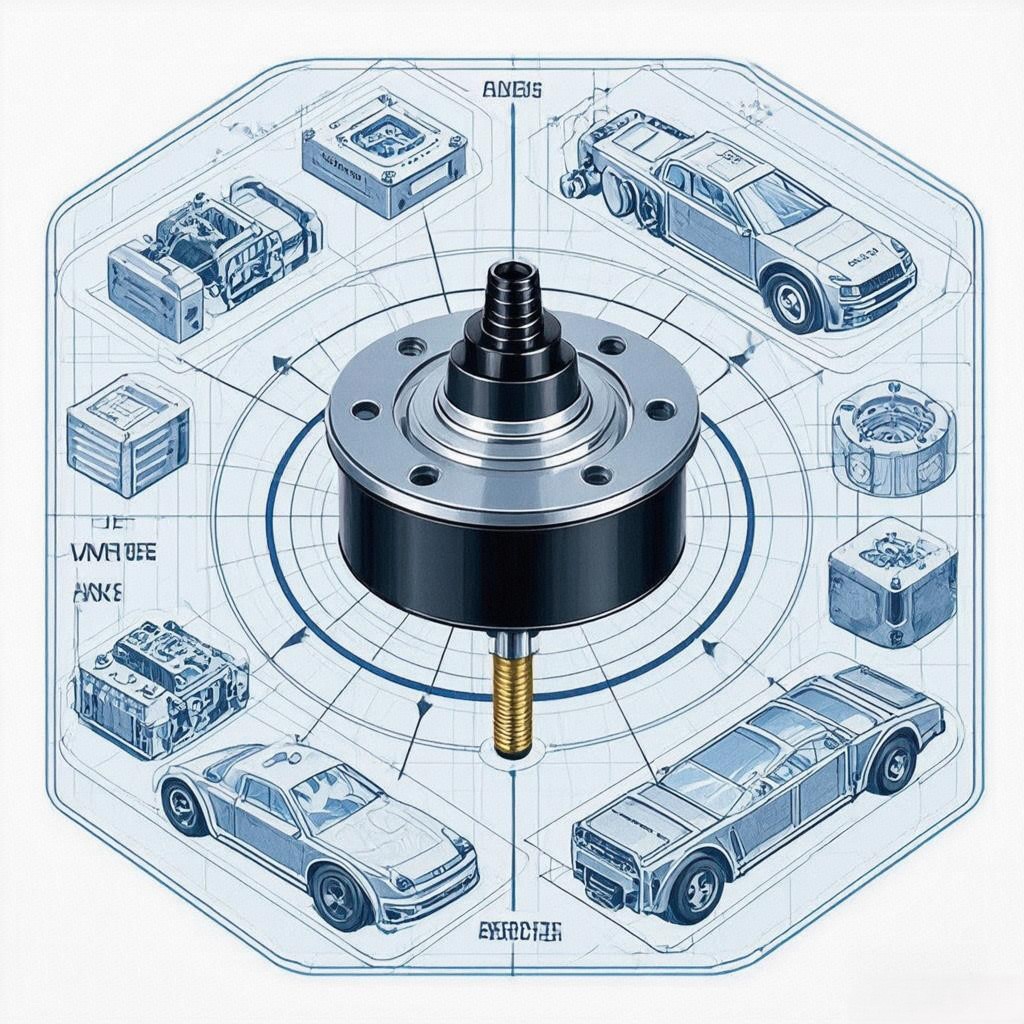
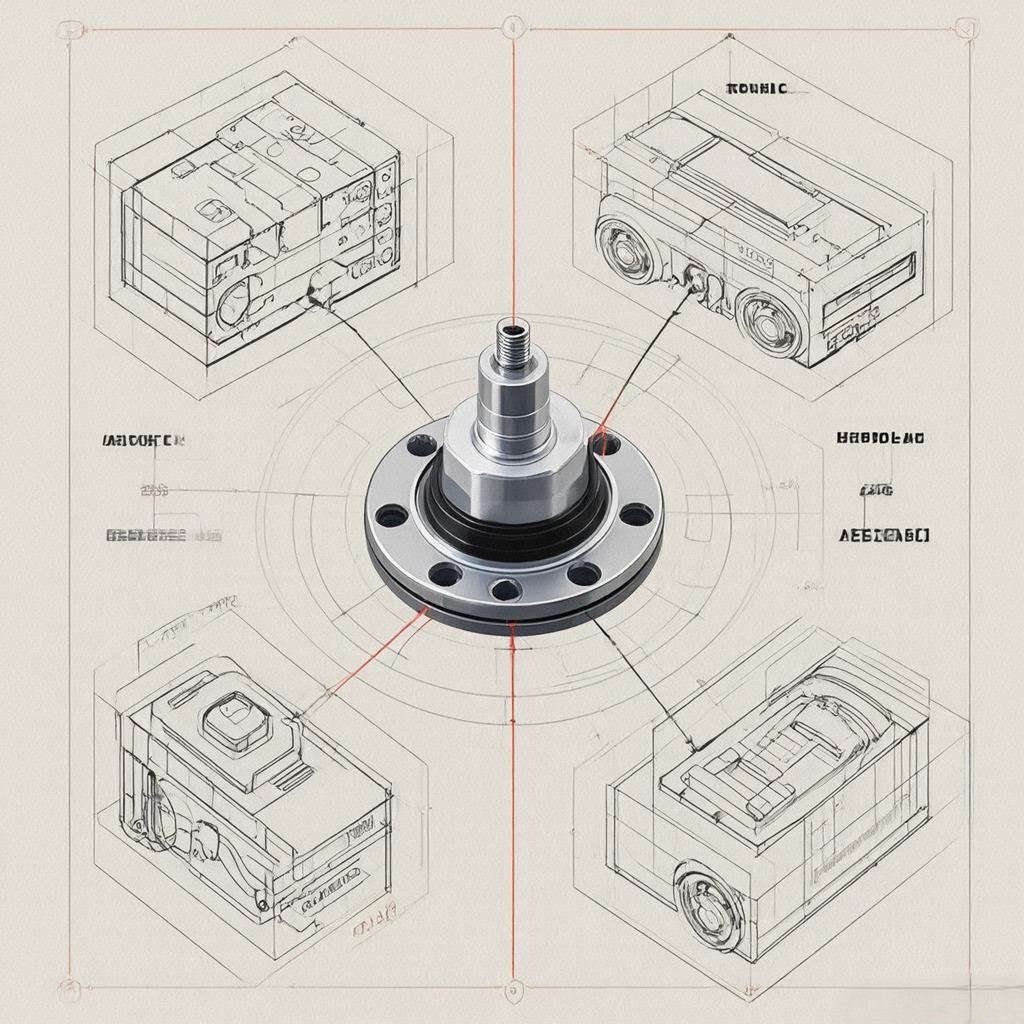
​​1. Fundamental Principles and Technical Significance​​
Wheel Speed Sensors form the foundational layer of vehicle dynamics control systems, providing real-time rotational velocity data that enables sophisticated electronic control systems to:
- ​​Prevent wheel lockup​​ during braking (ABS)
- ​​Optimize traction​​ under varying surface conditions (TCS)
- ​​Maintain vehicle stability​​ during extreme maneuvers (ESP)
- ​​Enable advanced driver assistance​​ functions (ADAS)
- ​​Support autonomous driving​​ algorithms
​​Technical specifications​​:
- Measurement range: 0-30,000 RPM (typical for passenger vehicles)
- Accuracy: ±0.5% of reading or ±1 RPM (whichever is greater)
- Output signal: Hall-effect (digital) or variable reluctance (analog)
- Operating temperature: -40°C to +150°C
- Response time: <1ms for signal processing
​​Industry impact​​: WSS contribute to a 30-50% reduction in accident rates through ABS and ESP systems, while enabling Level 2+ autonomous driving capabilities through precise vehicle dynamics control.
​​2. Core WSS Components and Functional Architecture​​
​​2.1 Sensor Types and Operating Principles​​
​​Hall-effect sensors​​:
- ​​Digital output​​: Square wave signal generation
- ​​Magnetic field detection​​: Immune to magnetic field variations
- ​​Signal processing​​: Integrated circuit for noise immunity
- ​​Power supply​​: Typically 5V from vehicle ECU
​​Magnetic reluctance sensors​​:
- ​​Analog output​​: Sine wave signal generation
- ​​Passive operation​​: No external power required
- ​​Signal conditioning​​: Required external amplification
- ​​Cost-effectiveness​​: Lower manufacturing costs
​​Inductive sensors​​:
- ​​Variable reluctance principle​​: Changing magnetic field detection
- ​​Simple construction​​: Fewer components than Hall-effect
- ​​Environmental resistance​​: Good durability characteristics
​​Key components​​:
- ​​Signal generation ring (tone wheel)​​:
- Ferrous or toothed wheel design
- Precision-machined teeth (0.5-2mm pitch)
- Material: Hardened steel or composite
- ​​Sensor element​​:
- Hall-effect IC with signal conditioning
- Permanent magnet for magnetic field generation
- Protection housing (IP67/IP69K rated)
​​Performance metrics​​:
- Signal frequency range: 0-10kHz (typical)
- Output voltage: 0.5-4.5V (Hall-effect), 0.1-5V (reluctance)
- Air gap tolerance: 0.5-1.5mm (varies by design)
​​2.2 Signal Processing and Integration​​
​​Sensor interface modules​​:
- ​​Analog-to-digital conversion​​: 10-16 bit resolution
- ​​Noise filtering​​: Digital signal processing (DSP) algorithms
- ​​Signal validation​​: Plausibility checks and cross-validation
​​ECU integration​​:
- ​​Dedicated wheel speed ECUs​​: For ABS/TCS systems
- ​​Integrated chassis control units​​: For ESP and ADAS systems
- ​​CAN/LIN communication​​: Standardized vehicle network protocols
​​Data processing algorithms​​:
- ​​Frequency analysis​​: RPM calculation from signal period
- ​​Noise rejection​​: Moving average and median filtering
- ​​Failure detection​​: Signal loss and implausible value monitoring
​​2.3 System Redundancy and Safety Features​​
​​Dual-channel architectures​​:
- ​​Independent sensor paths​​: For critical safety systems
- ​​Cross-channel validation​​: Comparison of redundant signals
- ​​Fail-operational modes​​: Graceful degradation
​​Diagnostic capabilities​​:
- ​​Open-circuit detection​​: Continuity monitoring
- ​​Short-circuit detection​​: Current sensing
- ​​Signal plausibility checks​​: Range and rate-of-change validation
​​Safety standards compliance​​:
- ​​ISO 26262 ASIL B/C​​: Functional safety requirements
- ​​SAE J2534​​: Reprogramming and diagnostics
- ​​U.S. FMVSS 126​​: Electronic stability control mandates
​​3. Advanced WSS Implementations and Innovations​​
​​3.1 High-Resolution Wheel Speed Sensing​​
​​Advanced sensor technologies​​:
- ​​Magneto-resistive sensors​​: Higher resolution than traditional reluctance sensors
- ​​GMR (Giant Magneto-Resistance)​​: Nanometer-scale magnetic field detection
- ​​TMR (Tunneling Magneto-Resistance)​​: Ultra-high sensitivity (1-2% of magnetic field)
​​Benefits of high-resolution sensing​​:
- ​​Improved ABS performance​​: More precise slip control
- ​​Enhanced TCS operation​​: Better traction on low-friction surfaces
- ​​Advanced ESP functionality​​: Finer stability corrections
- ​​Support for autonomous driving​​: Centimeter-level vehicle positioning
​​Performance metrics​​:
- Resolution: <0.1 RPM (high-end systems)
- Update rate: >1kHz for dynamic applications
- Signal-to-noise ratio: >60dB
​​3.2 Integrated Chassis Sensing Systems​​
​​Multi-functional sensor hubs​​:
- ​​Combined wheel speed and inertial measurement​​: 6-DOF sensing
- ​​Integrated temperature compensation​​: Ambient condition adjustment
- ​​Embedded signal processing​​: Local data filtering
​​Cooperative sensing approaches​​:
- ​​Wheel speed + steering angle​​: Enhanced yaw rate estimation
- ​​Wheel speed + accelerometer​​: Improved road grade detection
- ​​Wheel speed + suspension sensors​​: Better load transfer modeling
​​System benefits​​:
- ​​Redundant vehicle dynamics estimation​​: Cross-validation of sensor inputs
- ​​Improved fault tolerance​​: Graceful degradation modes
- ​​Enhanced safety​​: Multiple independent data sources
​​3.3 Smart Wheel Speed Systems​​
​​Predictive maintenance features​​:
- ​​Sensor health monitoring​​: Signal quality tracking
- ​​Remaining useful life prediction​​: Based on usage patterns
- ​​Proactive diagnostics​​: Early fault detection
​​Adaptive calibration​​:
- ​​Tire size compensation​​: Automatic adjustment for different tires
- ​​Temperature compensation​​: Magnetic property adjustments
- ​​Aging compensation​​: Sensor drift correction
​​Cybersecurity measures​​:
- ​​Secure communication protocols​​: Encrypted data transmission
- ​​Intrusion detection​​: Anomaly monitoring
- ​​Fail-safe mechanisms​​: Secure shutdown protocols
​​4. System Integration and Vehicle Applications​​
​​4.1 Safety Systems Integration​​
​​Anti-lock Braking System (ABS)​​:
- ​​Individual wheel control​​: Prevents lockup during hard braking
- ​​Pulse-width modulation​​: Modulates brake pressure
- ​​Hydraulic unit coordination​​: Fast-acting solenoid valves
​​Traction Control System (TCS)​​:
- ​​Wheel slip detection​​: Compares driven vs. non-driven wheels
- ​​Torque reduction​​: Engine and transmission intervention
- ​​Brake modulation​​: Selective wheel braking
​​Electronic Stability Program (ESP)​​:
- ​​Yaw rate control​​: Compares actual vs. desired vehicle path
- ​​Individual wheel braking​​: Targeted stabilization
- ​​Engine torque management​​: Power reduction when needed
​​Advanced driver assistance systems (ADAS)​​:
- ​​Electronic brake assist (EBA)​​: Emergency braking support
- ​​Hill start assist​​: Prevents rollback on inclines
- ​​Cornering brake control (CBC)​​: Optimized braking during turns
​​4.2 Autonomous Driving Applications​​
​​Vehicle localization​​:
- ​​Wheel speed integration​​: Dead reckoning positioning
- ​​High-resolution odometry​​: Centimeter-level accuracy
- ​​Sensor fusion​​: GPS, IMU, and wheel speed combination
​​Motion planning​​:
- ​​Precise speed control​​: Smooth acceleration/deceleration
- ​​Trajectory tracking​​: Lane-keeping and path following
- ​​Dynamic obstacle avoidance​​: Real-time adjustments
​​Redundant sensing​​:
- ​​Cross-validation​​: Comparison with other vehicle dynamics sensors
- ​​Fault tolerance​​: Graceful degradation modes
- ​​Safety monitoring​​: Continuous system health checks
​​4.3 Commercial Vehicle Applications​​
​​Heavy-duty truck systems​​:
- ​​Retarder control​​: Engine and exhaust braking coordination
- ​​Trailer stability assist​​: Anti-sway control for trailers
- ​​Load sensing​​: Adaptive brake force distribution
​​Off-highway equipment​​:
- ​​Implement control​​: Hydraulic system coordination
- ​​Grade control​​: Automatic depth maintenance
- ​​Articulated steering​​: Wheel speed synchronization
​​Specialized vehicles​​:
- ​​Firefighting apparatus​​: Pump and brake coordination
- ​​Military vehicles​​: Blast-resistant sensor designs
- ​​Agricultural equipment​​: Variable terrain compensation
​​5. Design Challenges and Engineering Solutions​​
​​5.1 Signal Integrity in Harsh Environments​​
​​Electromagnetic compatibility (EMC)​​:
- ​​Shielded sensor designs​​: Protection against EMI
- ​​Filtered signal processing​​: Noise rejection algorithms
- ​​Grounding schemes​​: Single-point grounding for EMI control
​​Mechanical durability​​:
- ​​Vibration-resistant mounting​​: Isolation from road-induced vibrations
- ​​Temperature-resistant materials​​: Wide operating range
- ​​Sealing systems​​: IP67/IP69K protection
​​Chemical resistance​​:
- ​​Fuel and oil resistance​​: Durable housing materials
- ​​Corrosion protection​​: Electroless nickel plating
- ​​Environmental sealing​​: Against water and dust ingress
​​5.2 Calibration and Adaptation​​
​​Initial calibration​​:
- ​​Tire size learning​​: Automatic detection of installed tires
- ​​Zero-speed offset​​: Baseline signal adjustment
- ​​Sensor alignment​​: Proper positioning verification
​​Adaptive compensation​​:
- ​​Temperature compensation​​: Magnetic property adjustments
- ​​Aging compensation​​: Sensor drift correction
- ​​Load compensation​​: Vehicle weight adaptation
​​Diagnostic capabilities​​:
- ​​Signal quality monitoring​​: Continuous performance tracking
- ​​Fault code storage​​: Historical error logging
- ​​Service alerts​​: Predictive maintenance indicators
​​5.3 Cost and Manufacturing Efficiency​​
​​Production optimizations​​:
- ​​Automated assembly​​: Robotic sensor installation
- ​​Just-in-time manufacturing​​: Reduced inventory costs
- ​​Modular designs​​: Common components across platforms
​​Material cost management​​:
- ​​Recyclable materials​​: End-of-life considerations
- ​​Alternative materials​​: Cost-effective substitutes
- ​​Process improvements​​: Reduced waste in manufacturing
​​Quality control efficiencies​​:
- ​​Automated inspection​​: Vision systems for 100% testing
- ​​Statistical process control​​: Real-time quality monitoring
- ​​Digital twins​​: Virtual testing before physical production
​​6. Testing and Validation Methodologies​​
​​6.1 Component-Level Testing​​
​​Sensor performance tests​​:
- ​​Signal output verification​​: Frequency and amplitude accuracy
- ​​Magnetic field response​​: Linearity and sensitivity
- ​​Environmental testing​​: Temperature and humidity cycling
​​Electrical characteristics​​:
- ​​Insulation resistance​​: High-voltage testing
- ​​Current consumption​​: Power efficiency measurement
- ​​EMC immunity​​: Radiated and conducted immunity
​​Mechanical durability​​:
- ​​Vibration testing​​: 15g RMS, 10-2,000Hz
- ​​Shock testing​​: 100g half-sine pulses
- ​​Salt spray exposure​​: 1,000 hours for corrosion resistance
​​6.2 System-Level Validation​​
​​Vehicle dynamics testing​​:
- ​​ABS performance​​: Stopping distance and wheel lock prevention
- ​​TCS effectiveness​​: Traction maintenance on slippery surfaces
- ​​ESP stability​​: Yaw rate control during evasive maneuvers
​​Environmental validation​​:
- ​​Temperature extremes​​: -40°C to +50°C operation
- ​​Altitude testing​​: Up to 4,000m elevation performance
- ​​Water ingress testing​​: IP67/IP69K verification
​​Endurance testing​​:
- ​​1,000-hour durability​​: Continuous operation
- ​​100,000km road testing​​: Real-world conditions
- ​​Thermal cycling​​: -40°C to +125°C, 1,000 cycles
​​6.3 Virtual Validation​​
​​Simulation tools​​:
- ​​SPICE models​​: Electronic circuit simulation
- ​​MATLAB/Simulink​​: Control algorithm validation
- ​​ANSYS Maxwell​​: Magnetic field analysis
​​Test scenarios​​:
- ​​10,000+ virtual test cases​​ covering all operating conditions
- ​​Edge case testing​​: Extreme loads and temperatures
- ​​Long-term durability simulation​​: 10-year equivalent cycles
​​7. Market Trends and Future Developments​​
​​7.1 Electrification and Autonomous Driving​​
​​Key innovations​​:
- ​​High-resolution sensing​​: For precise vehicle localization
- ​​Integrated sensor fusion​​: Combining with IMU and GPS data
- ​​Predictive maintenance​​: AI-based fault prediction
​​Technical challenges​​:
- ​​System redundancy​​: Fail-operational requirements
- ​​Cybersecurity​​: Secure communication protocols
- ​​Energy efficiency​​: Low-power sensor designs
​​7.2 Advanced Materials and Manufacturing​​
​​Innovative approaches​​:
- ​​MEMS-based sensors​​: Miniaturized designs
- ​​3D-printed housings​​: Complex geometries without tooling
- ​​Additive manufacturing​​: Rapid prototyping capabilities
​​Sustainability focus​​:
- ​​Recyclable materials​​: End-of-life considerations
- ​​Energy-efficient manufacturing​​: Reduced carbon footprint
- ​​Smart materials​​: Self-diagnostic capabilities
​​7.3 Smart and Connected Vehicle Systems​​
​​Emerging technologies​​:
- ​​Over-the-air updates​​: Software improvements without service visits
- ​​Digital twin technology​​: Predictive maintenance and performance monitoring
- ​​AI-based learning algorithms​​: Personalized driving profiles
​​User benefits​​:
- ​​Reduced maintenance​​: Predictive service alerts
- ​​Improved performance​​: Continuous optimization
- ​​Enhanced safety​​: Real-time diagnostics
​​8. Case Studies: Real-World Implementations​​
​​Case Study 1: Premium Electric Vehicle WSS System​​
A leading EV manufacturer implemented a high-resolution WSS system with:
- 0.01% speed measurement accuracy
- Integrated temperature compensation
- Predictive maintenance features
​​Results​​:
- 20% improvement in ABS performance
- 15% better traction control on slippery surfaces
- Extended sensor lifespan
​​Case Study 2: Autonomous Driving Test Vehicle​​
An autonomous vehicle developer created a specialized WSS system with:
- Redundant sensor architecture
- High-speed data processing
- Advanced signal filtering
​​Results​​:
- Centimeter-level localization accuracy
- Reliable operation in complex environments
- Seamless integration with other vehicle sensors
​​Conclusion: The Precision Foundation of Vehicle Dynamics​​
Wheel Speed Sensors represent the critical interface between vehicle dynamics and electronic control systems, combining mechanical precision with advanced electronics to deliver optimal safety and performance. As vehicles become more sophisticated with electrification and autonomy, these systems will continue evolving to meet new challenges while maintaining their core function of precise rotational speed measurement.
​​Key takeaways:​​
- Modern WSS combine high-resolution sensors with sophisticated signal processing
- Advanced materials and manufacturing enable higher precision and durability
- System integration with electrification and autonomy requires new engineering approaches
- Sustainability and digitalization are transforming WSS design
​​Final thought​​: In the era of autonomous driving and electric mobility, WSS have become the unsung heroes of vehicle dynamics control. The next generation of these systems will need to balance unprecedented precision requirements with the demands of alternative powertrains, connectivity, and environmental sustainability, making them one of the most critical areas of automotive innovation today.
​​Call to Action​​
đź”§ Upgrading your vehicle’s WSS system?
⚙️ Explore our advanced sensor solutions for improved safety and performance
📊 Request technical specifications and performance data for your specific application
#WheelSpeedSensor #AutomotiveEngineering #ADAS #ABS #TCS #VehicleSafety #Electrification #SmartMobility #FutureOfTransportation #FunctionalSafety